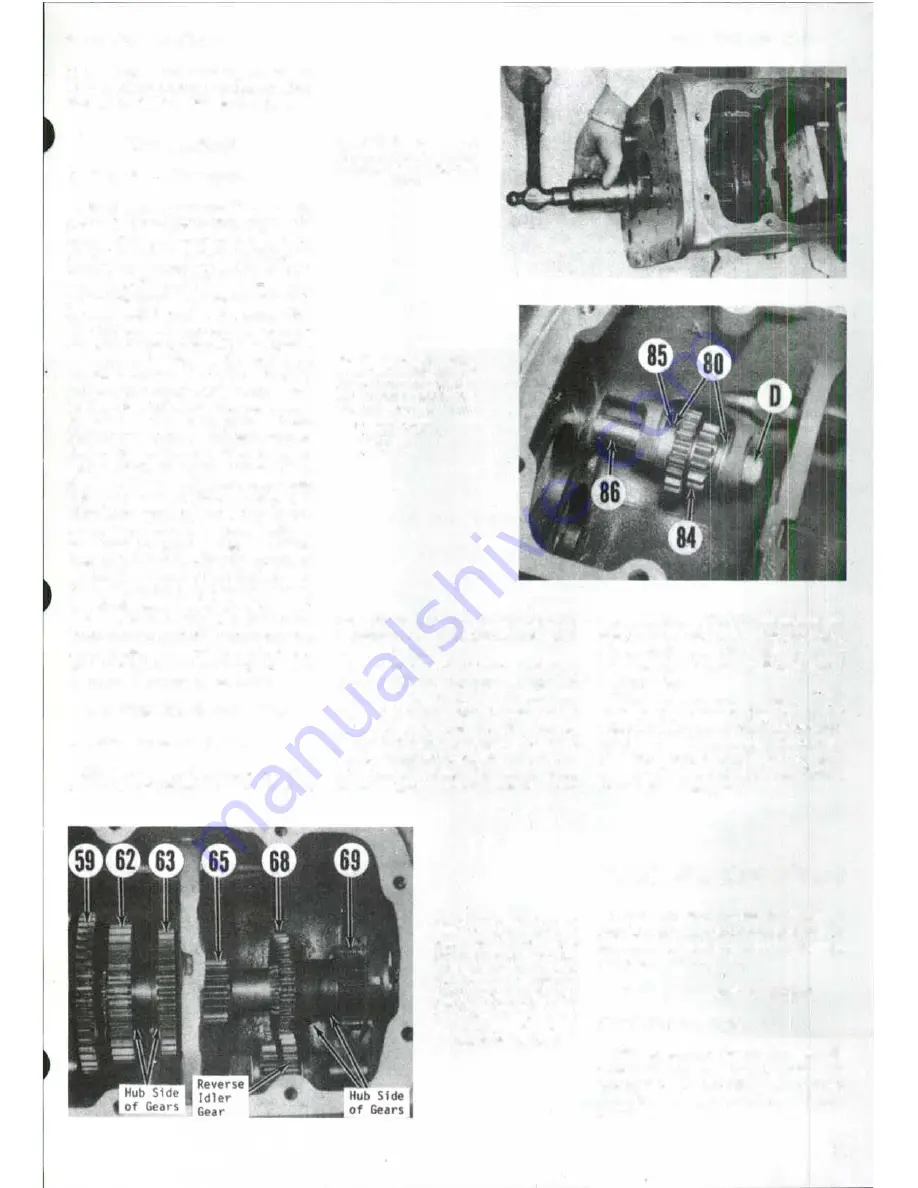
SERVICE MANUAL
131. Apply nonhardening sealer to
threads of retaining cap screws, then
tighten to 60
N
·
m (45 ft..-lbs.) torque.
COUNTERSHAFT
All Models So Equipped
134.
1b
remove countershaft (65-Fig.
129) and related gears, first remove pto
lower shaft and gear as outlined in
paragraph 133 and mainshaft and gears
as outlined in paragraph 132. Remove
snap rings (61 and 71) from front and
rear of countershaft. Tap countershaft
forward until free of rear bearing (70),
then tap bearing real'ward out of hous
ing. Unseat snap ring (67) from groove
in shaft and slide it forward onto
unsplined section of shaft. Slide shaft
rearward and remove two geat·s (62 and
63) from front of shaft, then move shaft
forward and remove two gears (68 and
69) from rear of shaft. Withdraw counter
shaft with front bearing from housing.
1b
reinstall, insert countershaft from
the front while installing rear geru-s with
hubs positioned as shown in Fig. 132.
Slide shaft rearward until front gears
can be inst.alled making sure hubs are
positioned as shown in Fig. 132. Move
snap ring (67-Fig. 129) into its groove
in shaft. Position rear bearing (70) over
shaft with outer snap ring on bearing
towards the rear. Block front. of counter
shaft as shown in Fig. 133, then drive
bearing onto rear of shaft until snap ring
can be installed. Install snap ring onto
front of shaft. Complete installation by
reversing the removal procedure.
REVERSE IDLER ASSEMBLY
All Models So Equipped
135.
The
reverse idler gear (84-Fig.
129) and shaft (86) can be removed from
Fig. 133-Biock front of
countersheft as shown when
/nste/1/ng rear bearing onto
shaft.
Fig. 134-Use a dummy shaft
(D)
to hold needle rollers In
place In Idler when removing
and Installing reverse Idler
gear assembly. Refer to text.
80 Thrust
wosh"ro
84 Reverr.e
adler 11
e
a
r
85.
Spacer
86 Idler shof\
transmission housing after removing the
mainshaft (17) and gears as outlined in
paragraph 132.
The idler shaft is retained in housing
by a clip (87) and cap screw at rear face
of transmission case. The cluster gear
(84) contains two rows of loose needle
rollers (28 each row). Use of a dummy
shaft will facilitate removal and installa
tion by preventing needle rollers from
falling out of position. Dummy shaft can
be made from 25 mm (1 inch) diameter
Fig. 132-VIew of counter
shaft and gears correctly
assembled. Pto drive gear
and countershaft constant
mesh gears are shown at (59
and 62). First gear and sec
ond speed gears are shown at
(65 and 69). Gears (63 and 68)
are either third or fourth
speed depending upon
specific transmission.
Paragraphs
1 34-1 36
bru· stock 55 mm (2-3/16 inches) long. In
sert dummy shaft. <D-Fig. 134) into front
of gear to displace idler shaft, then lift.
out gear assembly, spacer (85) and thrust
washe1-s (80).
When reassembling, apply ltght
coating of petroleum jelly to needle
rollers and use dummy shaft.
to
hold com
ponents in position in gea
r
cluster. In
sert idler shaft thl'ough gear to push
dummy shafl out of the gear. Secw·e
shaft with locking clip.
MANUAL SHU TTLE
Models MF235, MF245 and MF250
may be equipped with a manual shuttle
transmission which provides six forward
and six reverse speeds.
TRANSMISSION REMOVAL
All Models So Equipped
136.
1b
remove the manual shuttle
transmission assembly, refer to
paragraph 127 and follow the general
procedure for eight-speed transmission
removal.
55