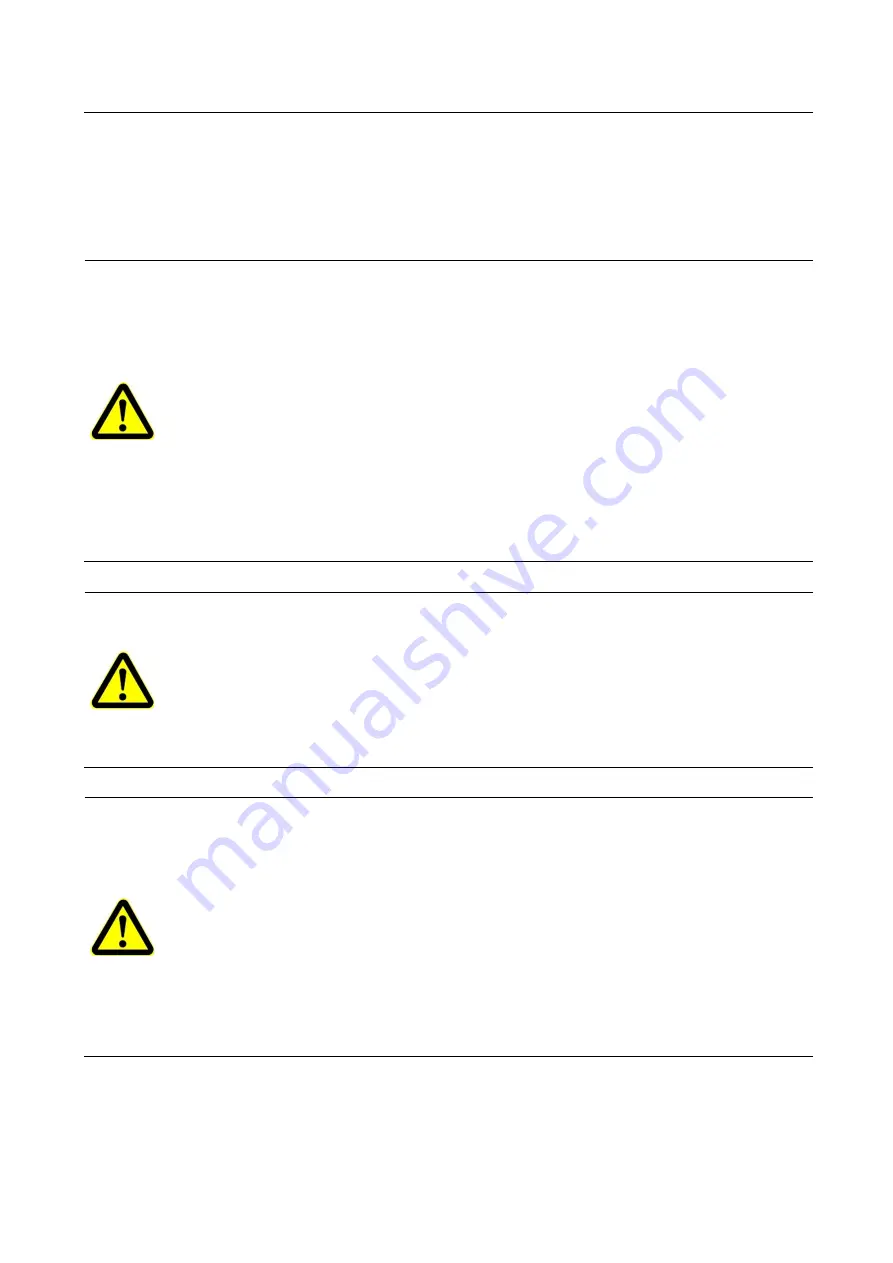
44
BA053101-en
Pos: 149 /Technis che Dok umentation/A lle G eräte/ Überschr iften/Üb erschriften 1/ B/Überschrift 1: Beschreib ung der SINAMICS- Komp onenten @ 14\mod_ 1241599608976_ 75.docx @ 371799 @ 1 @ 1
3
Description of the SINAMICS Components
Pos: 150 /Technis che Dok umentation/A lle G eräte/ Überschr iften/Üb erschriften 1.1/S/ Überschr ift 1.1: Spez ielle Sicher heitshinweis e für SINAMICS-Komponenten @ 14\m od_1241599671359_ 75.docx @ 371825 @ 2 @ 1
3.1
Special Safety Instructions for the SINAMICS Components
Pos: 151 /Technis che Dok umentation/ Leis tungsmesstechnik/POWE RDYNO/053101 M SR/ BA/Inhalt: 0531 SINAMICS Spezielle Sicherheitshinw eis e @ 24\m od_1305785790028_75.d ocx @ 1009623 @ @ 1
Commissioning shall not start until you have ensured that the machine in which the components
described here are to be installed complies with Directive 2006/42/EC.
SINAMICS S equipment must only be commissioned by suitably qualified personnel.
The personnel must take into account the information provided in the technical customer docu-
mentation for the product, and be familiar with and observe the specified danger and warning no-
tices.
When electrical equipment and motors are operated, the electrical circuits automatically conduct a
dangerous voltage.
Dangerous mechanical movements may occur in the system during operation.
All work on the electrical system must be performed after the system has been switched off and
disconnected from the power supply.
SINAMICS S equipment with three-phase motors may only be connected to the line system via
residual current devices (RCDs) if compatibility of the SINAMICS equipment with the RCD has
been ensured as specified in EN 50178, Subsection 5.2.11.2.
Correct and safe operation of SINAMICS S equipment assumes correct transportation, storage,
setup, and installation, as well as careful operation and maintenance.
The details in the catalogs and proposals also apply to the design of special equipment versions.
In addition to the danger and warning information provided in the technical customer documenta-
tion, the applicable national, local, and system-specific regulations and requirements must be tak-
en into account.
Only protective extra-low voltages (PELVs) that comply with EN 60204-1 must be connected to all
connections and terminals between 0 and 48 V.
A hazardous voltage will be present in the component for a further 5 minutes after the system has
been shutdown. Work cannot be carried out until this time has elapsed.
Before starting work, you should also measure the voltage after the 5 minutes have elapsed.
The voltage can be measured on DC link terminals DCP and DCN.
The clearances above, below, and in front of the component, which are specified in the dimension
drawings, must be observed.
The DC link discharge time hazard warning must be affixed to the component, in the local lan-
guage.
In a supply system without regenerative capability (e.g. diesel generator), the regenerative feed-
back capability of the Active Line Module must be deactivated via a parameter (see Description of
Functions). The braking energy must then be dissipated via an additional Braking Module with a
braking resistor in the drive line-up.