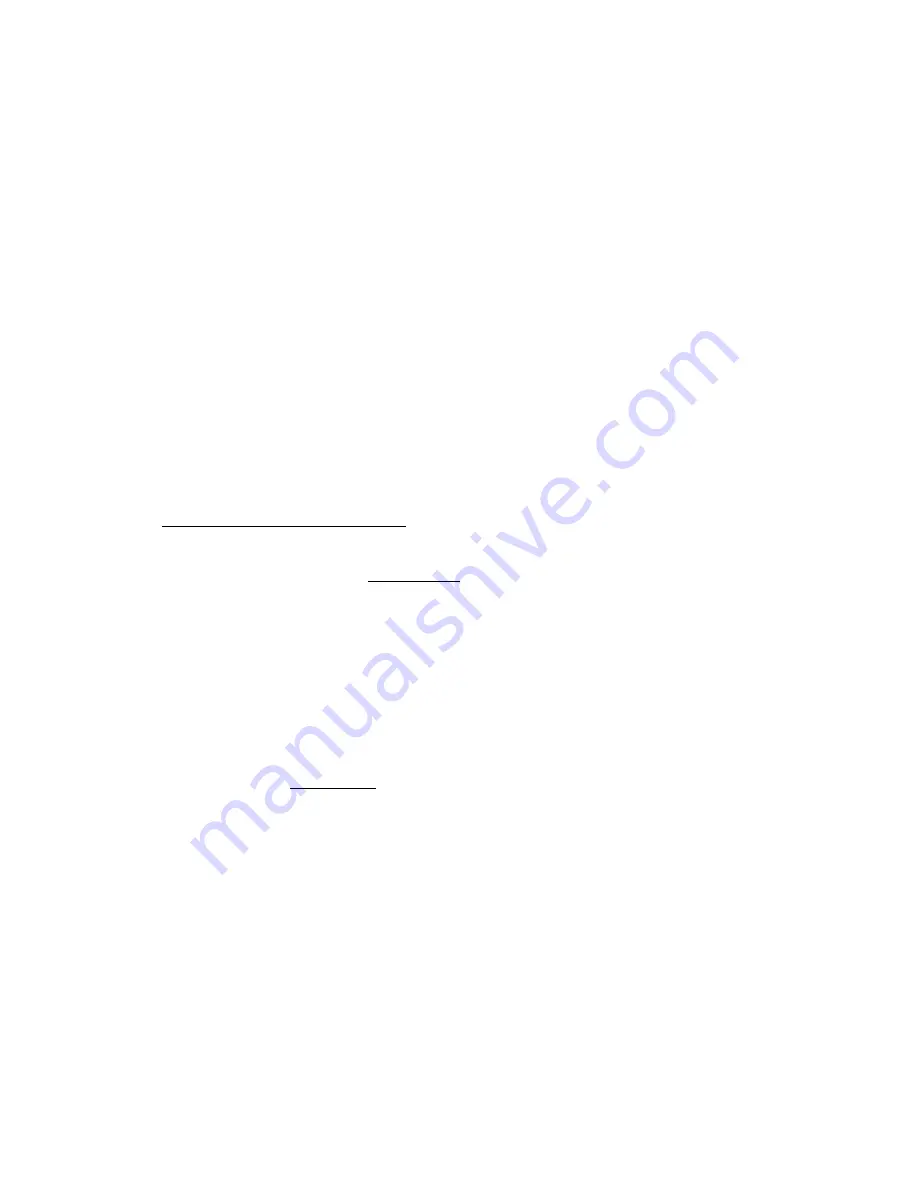
MacDonald Steel Limited
BREWERY SYSTEMS DIVISION
27
REV 00
Shuttle Forward Prox Fault
The front proximity switch on the shuttle is not being detected. . If the machine does not start or
the crowner will not operate the switch must be checked and adjusted or replaced. If the machine
cycles then the timing of the shuttle is too slow and the flow control on the cylinder must be
adjusted.
Shuttle Back Prox Fault
The back proximity switch on the shuttle is not being detected. . If the fill heads will not lower the
switch must be checked and adjusted or replaced. If the machine cycles then the timing of the
shuttle is too slow and the flow control on the cylinder must be adjusted.
Head up Prox Switch
The proximity switch on the head cylinder is not being detected. . If the machine does not start
or the shuttle will not come forward the switch must be checked and adjusted or replaced. If the
machine cycles then the timing of the head cylinder is too slow and the flow control on the
cylinder must be adjusted.
Head Disabled
This message appears when the fill head has been disabled.
TROUBLESHOOTING - other
Auto Level Detection
As noted above in the section "Head Bridged" , the fill tube and vent tube are used to determine
the proper level. Wires from each tube go from the fill head to the PLC input. Contact between
the wires and the tubes are through the set screws in the fill head. These set screws must make
contact with the metal tubes. If one of the screws becomes loose or the wiring at the fill head
breaks, the level detection will not function. To test the level sensor:
- remove the teflon filling tube from the fill head by unscrewing it.
- remove the bottle from the shuttle base.
- use the manual control screen and lower the fill head.
- go to the I/O check screen
- use a small screwdriver or other metal object (paper clip etc) and gently short the vent tube and
the metal fill tube together.
- observe the input "Level Probe" for the appropriate fill head on the I/O screen. If the circuit to
the PLC is intact, the LED should turn to green. If circuit is broken the LED will remain red.
- If there is no green LED at the fill & vent tubes, then remove the short from the tubes and place
it across the two set screws instead. This will check the actual wiring from the fill head to the
PLC.
- If the LED remains red then the problem is most likely in the wiring. If the LED turns to green
with this check, then the problem is lost contact between one of the set screws and one of the
tubes.
- to determine which set screw has lost contact, short the lower set screw to the fill tube. You
may need a piece of wire to perform this test. A red LED indicates contact has been lost at the fill
tube (upper) set screw. A green LED indicates lost contact at the vent (lower) set screw.
- Once it has been determined which set screw has lost contact, loosen the appropriate lock nuts
while holding the set screw with an Allen key
and gently turn the set screw CW very slightly.
Tightening the set screw too much can damage the tube. Perform the tests again to determine if
contact has been made. Tighten the locknut up against the fill head
while holding the set
screw with an Allen key.