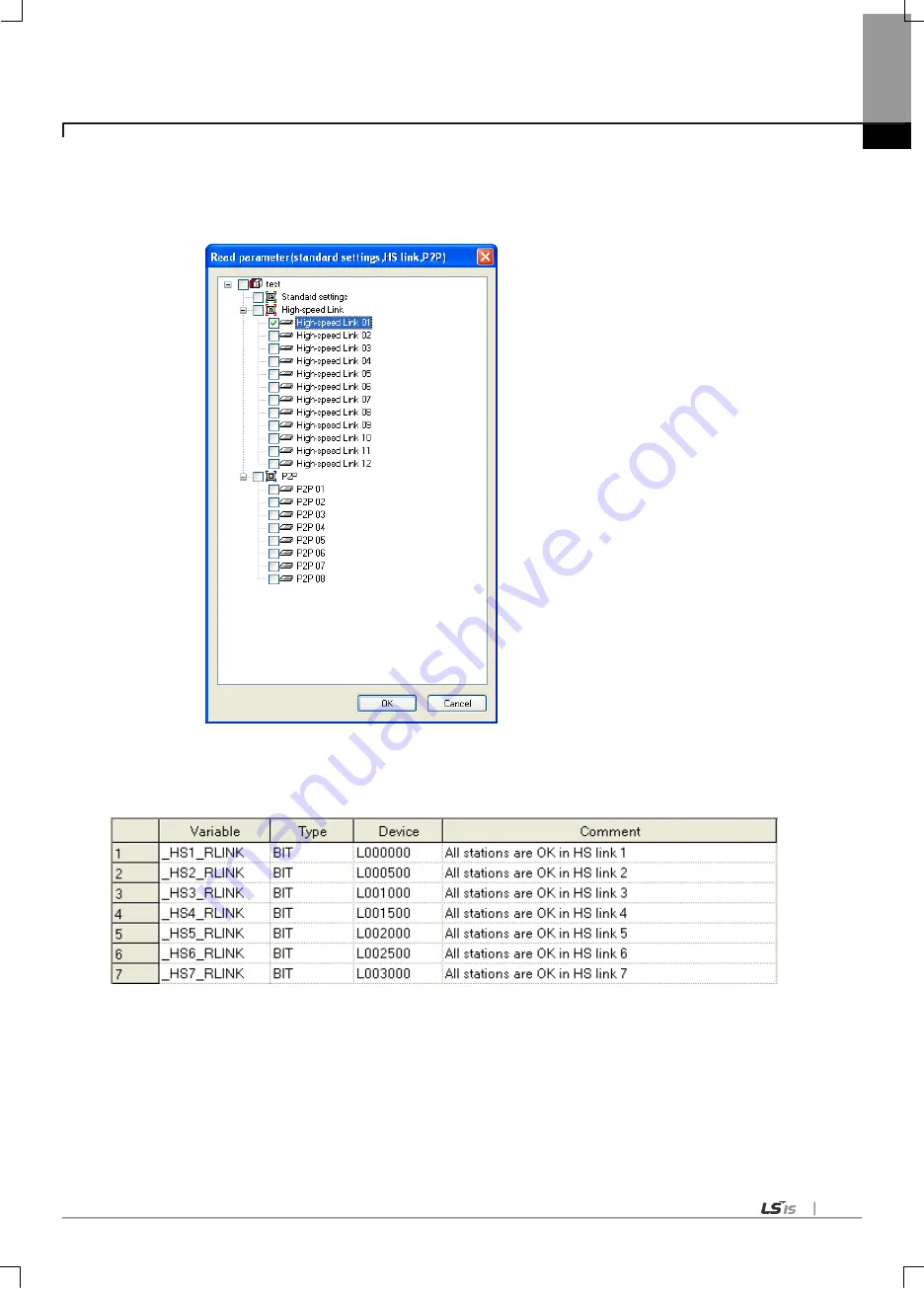
Chapter 5. Communication Parameters
5-25
(4) Read high speed parameter
Select „Read Parameter‟ from the Online menu. Check the desired parameter and click Confirm button to read the high
speed link parameter.
(5) High speed link information
The high speed link information is provided to the XG5000 user as user keyword for use in programming.
Type of high speed link flags
Содержание XBL-EIMT
Страница 153: ...Appendix A 17 A 3 Dimension Unit mm XGL EIMT EIMF EIMH ...
Страница 154: ...Appendix A 18 XOL EIMT EIMF ...
Страница 155: ...Appendix A 19 XBL EIMT ...