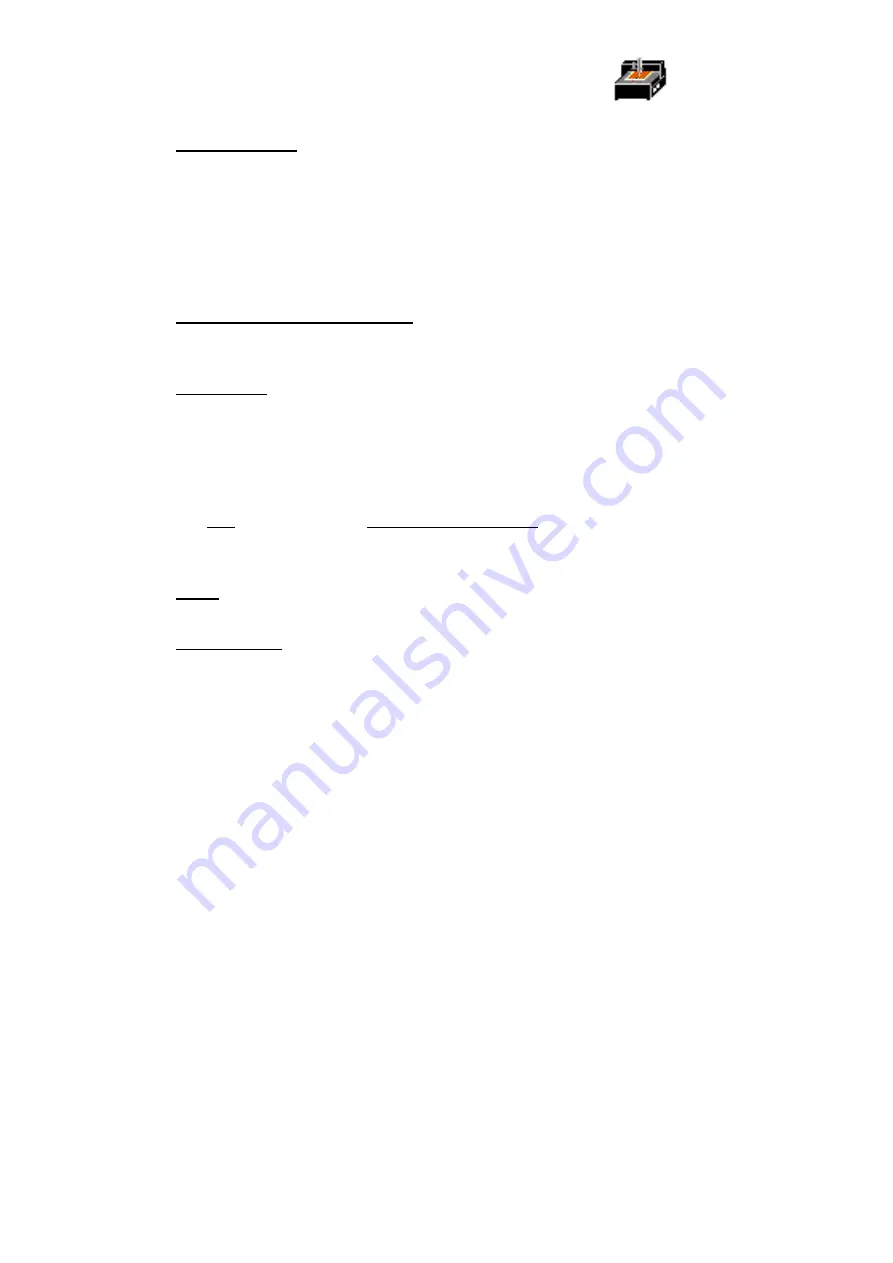
LPKF ProtoMat 93s Manual
48
•
Drill deflection
occurs in particular with thin tools which are no longer
absolutely sharp. However, this also depends on the surface structure of the
material. If, for example the glass fiber structure of FR4 materials penetrates
the copper, drill deflection cannot be avoided even with a sharp tool.
For materials with additional, removable copper film (FR4 material with 18 µm
or 9 µm
Cu coating), drill deflection is very slight.
•
Vitrification of the drilled hole
occurs where the drill stays in the hole too long
once the hole has been made. These holes then cause problems at
feedthrough stage. Reduce drilling times as appropriate.
•
Drills break
where the drilling base has already been used a number of times.
The drilling base should be changed for every new PCB. It is not really
possible to prevent breakage if a drill comes into contact with the edge of an
existing hole in the base. Broken tools must be removed from the PCB and the
drilling base. Drills can also break if the tool is too high above the material.
•
In film milling, milled channels are uneven if there is still air under the film. If
the
film
is secured with
elastic adhesive tape
, waves may form in the film after
a while. It is particularly important here that the milling base should be level
(LPKF film engraving base).
•
Burrs
are produced when milling films either because the tool is blunt or milling
was too deep.
•
Misalignment
of the solder and component sides occurs where the HOME
position is not accurately programmed.