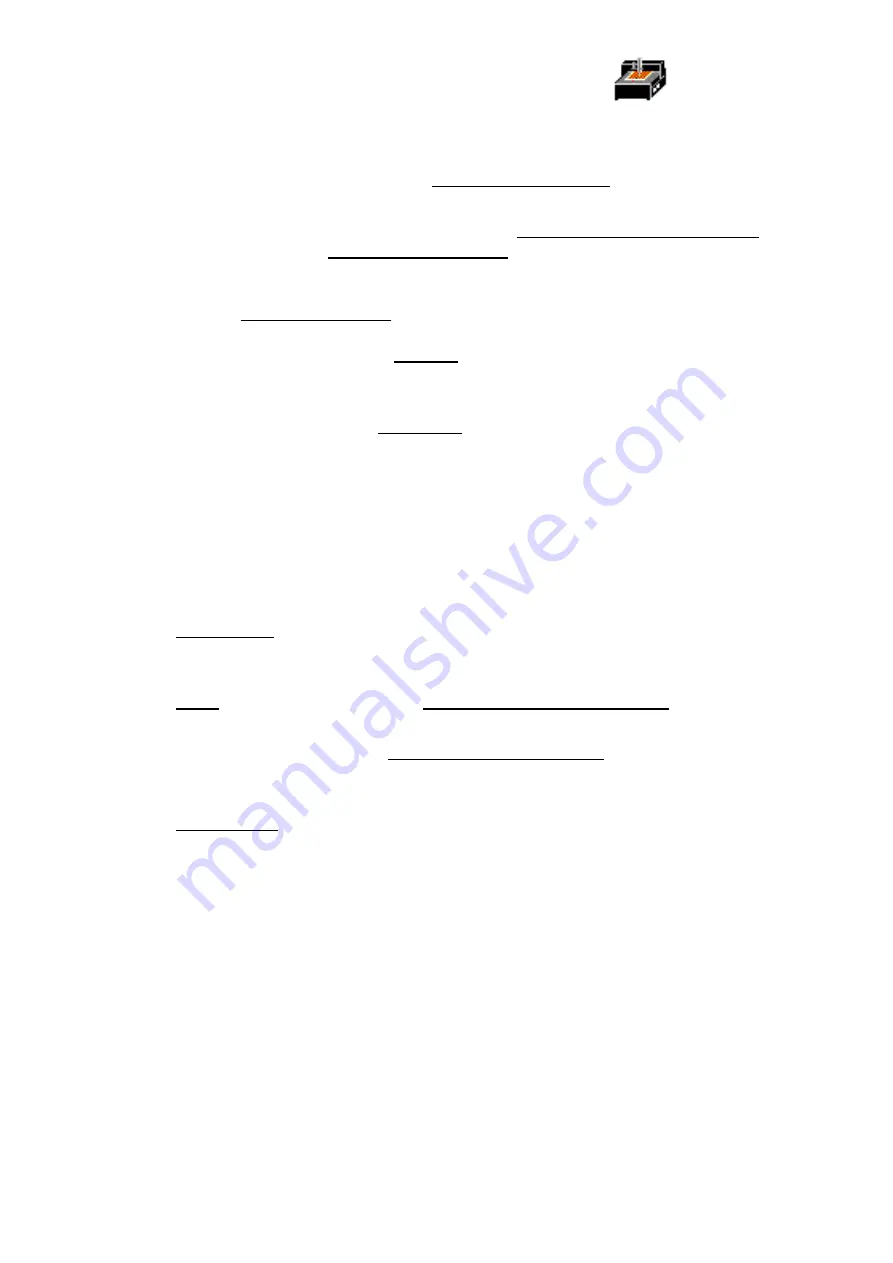
LPKF ProtoMat 93s Manual
47
7.12 Practical tips
•
Set the milling depth such that
engraving is too deep
rather than too shallow.
Insufficient depth when engraving promotes milling tool wear.
•
There can be a number of causes of
uneven milling width (depth)
. It is
important that the
machine bed is clean.
Residues of adhesive tape or such
like can adversely affect milling depth quite considerably. Also, milling swarf
between the machine bed, drilling support and PCB can reduce precision.
Greatly
distorted materials
bend such that the sag shows underneath; in this
case, secure the edges well with adhesive tape. Another important point for
precise milling depth is the
removal
of milling and drilling chips.
•
Hooks can occur between the milling channels if the incorrect milling direction
was specified , in particular with circles. If a circle is to be milled with a tool
which rotates clockwise,
fine hooks
can arise between the copper areas if the
milling tracks should overlap. The reason for this is that the cutting speed on
the outer edges is reduced.
The solution lies in selecting the right milling direction. When isolating
conductor paths with LPKF isolate, the solder side should be mirrored before
isolating as the isolation algorithm itself works in a clockwise direction. The
standard postprocessing is already designed for this. CircuitCAM allows the
user to select the direction of the milling tool and therefor mirroring prior to
isolation is not necessary.
•
Milling burrs
can be caused by blunt tools or incorrect speeds of movement. If
possible with the structure to be milled, deeper settings can be the answer.
Otherwise, change the tool.
•
Burrs
when contour milling or
cut edges which are not clean
occur either due
to a blunt tool or incorrect advance speed.
•
With some materials, the
color of the milled channel
gives some indication of
the state of the tool. With epoxy materials, dark isolation paths indicate a sharp
tool, while lighter ones indicate a blunter tool.
•
Drilling burrs
occur either because the tool is blunt or the head lowering speed
is excessive. In the first case, change the tool. In the second case, the tool
height over the material must be reduced.