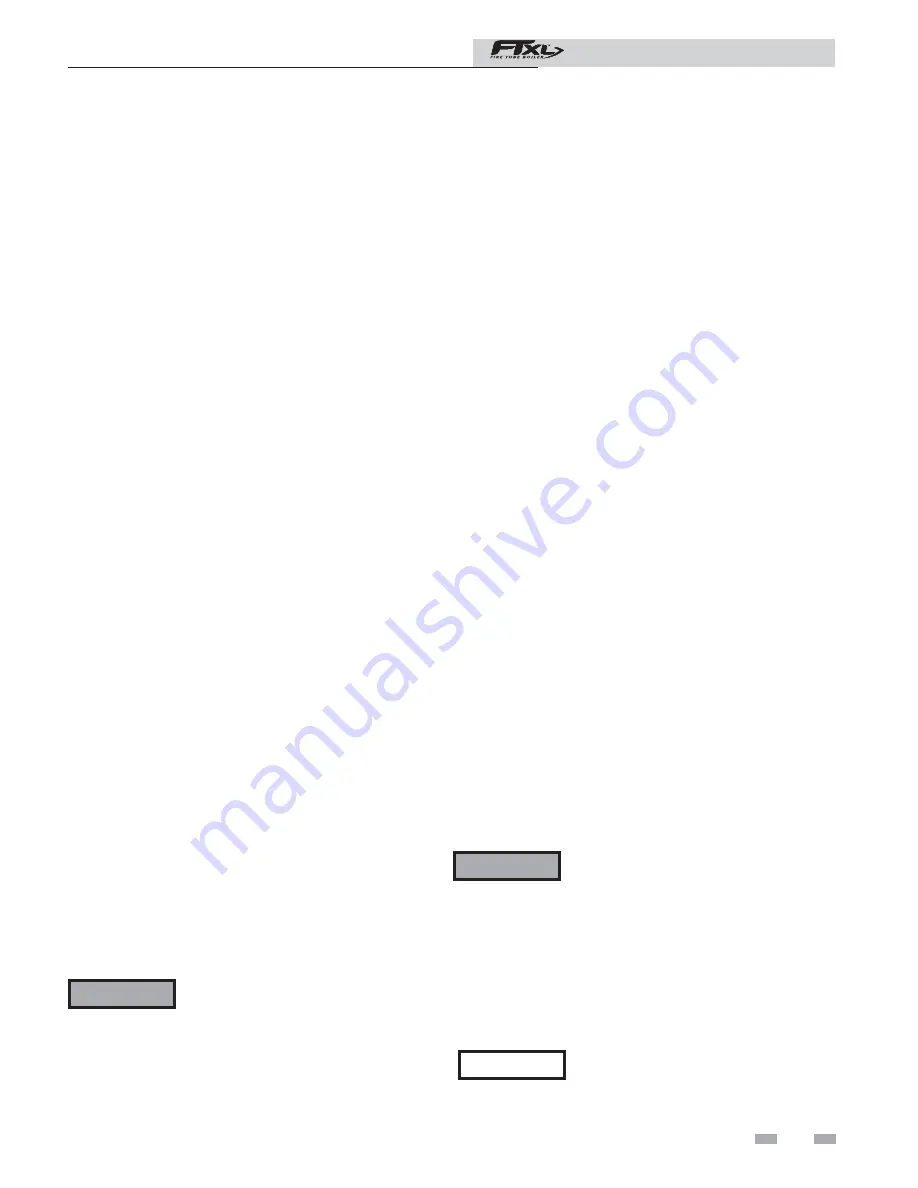
37
6
Hydronic piping
System water piping methods
The FTXL is designed to function in a closed loop system
pressurized to not less than 12 psi (83 kPa). A temperature
and pressure gauge is included to monitor system pressure
and outlet temperature and should be located on the boiler
outlet.
It is important to note that the boiler has a minimal amount
of pressure drop which must be accounted for when sizing
the circulators. Each boiler installation must have an air
elimination device, which will remove air from the system.
Install the boiler so the gas ignition system components
are protected from water (dripping, spraying, etc.) during
appliance operation or basic service of circulator replacement,
valves, and others.
Observe a minimum of 1/4 inch (6 mm) clearance around all
un-insulated hot water pipes when openings around the pipes
are not protected by non-combustible materials.
Low water cutoff device
This boiler comes equipped with a low water cutoff device.
On a boiler installed above radiation level, some states and
local codes require a low water cutoff device at the time of
installation.
Chilled water system
If the boiler supplies hot water to heating coils in air handler
units, fl ow control valves or other devices must be installed to
prevent gravity circulation of heater water in the coils during
the cooling cycle. A chilled water medium must be piped in
parallel with the heater.
Freeze protection
Freeze protection for new or existing systems must use
glycol that is specially formulated for this purpose. This
includes inhibitors, which prevent the glycol from attacking
the metallic system components. Make certain to check that
the system fl uid is correct for the glycol concentration and
inhibitor level. The system should be tested at least once
a year and as recommended by the producer of the glycol
solution. Allowance should be made for the expansion of the
glycol solution in the system piping.
General piping information
Basic steps are listed below along with illustrations on the
following pages (FIG.’s 6-5 through 6-10), which will guide you
through the installation of the FTXL (reference FIG.’s 6-3A and
6-3B).
1. Connect the system return marked “Inlet”.
2. Connect the system supply marked “Outlet”.
3. Install purge and balance valve or shutoff valve and drain
on system return to purge air out of each zone.
4. Install
a
backfl ow preventer on the cold feed make-up water
line.
5. Install a pressure reducing valve on the cold feed make-up
water line, (15 psi (103 kPa) nominal). Check temperature
and pressure gauge (shipped separately), which should read
a minimum pressure of 12 psi (83 kPa).
6. Install a circulator as shown on the piping diagrams in this
section. Make sure the circulator is properly sized for the
system and friction loss.
7. Install an expansion tank on the system supply. Consult the
tank manufacturer’s instruction for specifi c information
relating to tank installation. Size the expansion tank for the
required system volume and capacity.
8. Install an air elimination device on the system supply.
9. Install a drain valve at the lowest point of the system.
Note:
The boiler cannot be drained completely of water
without purging the unit with an air pressure of 15 psi
(103 kPa).
10. This appliance is supplied with a relief valve sized in
accordance with ASME Boiler and Pressure Vessel Code,
Section IV (“Heating Boilers”). Pipe the discharge of the
safety relief valve to prevent injury in the event of pressure
relief. Pipe the discharge to a drain. Provide piping that is
the same size as the safety relief valve outlet. Never block
the outlet of the safety relief valve.
11. On any pre-existing system, it is good practice to install
a fi eld supplied strainer to prevent damage to the heat
exchanger.
See the piping illustrations included in this section, FIG.’s 6-5
and 6-10 for suggested guidelines in piping the FTXL.
Please note that these illustrations are
meant to show system piping concept only,
the installer is responsible for all equipment
and detailing required by local codes.
Use only inhibited propylene glycol
solutions, which are specifi cally formulated
for hydronic systems. Ethylene glycol is
toxic and can attack gaskets and seals used
in hydronic systems.
WARNING
NOTICE
Installation & Operation Manual
WARNING
The relief valve, tee and any other necessary
fi ttings are shipped in the install kit with the
boiler and are to be fi eld installed (FIG.’s 6-1
and 6-2).
Содержание 500
Страница 55: ...55 8 Field wiring continued Figure 8 3 Low Voltage Field Wiring Connections Installation Operation Manual ...
Страница 60: ...60 Figure 10 2 Operating Instructions 10 Start up Installation Operation Manual ...
Страница 78: ...78 Figure 13 1 Wiring Diagram 13 Diagrams Installation Operation Manual ...
Страница 79: ...Figure 13 2 Ladder Diagram 13 Diagrams continued 79 Installation Operation Manual ...