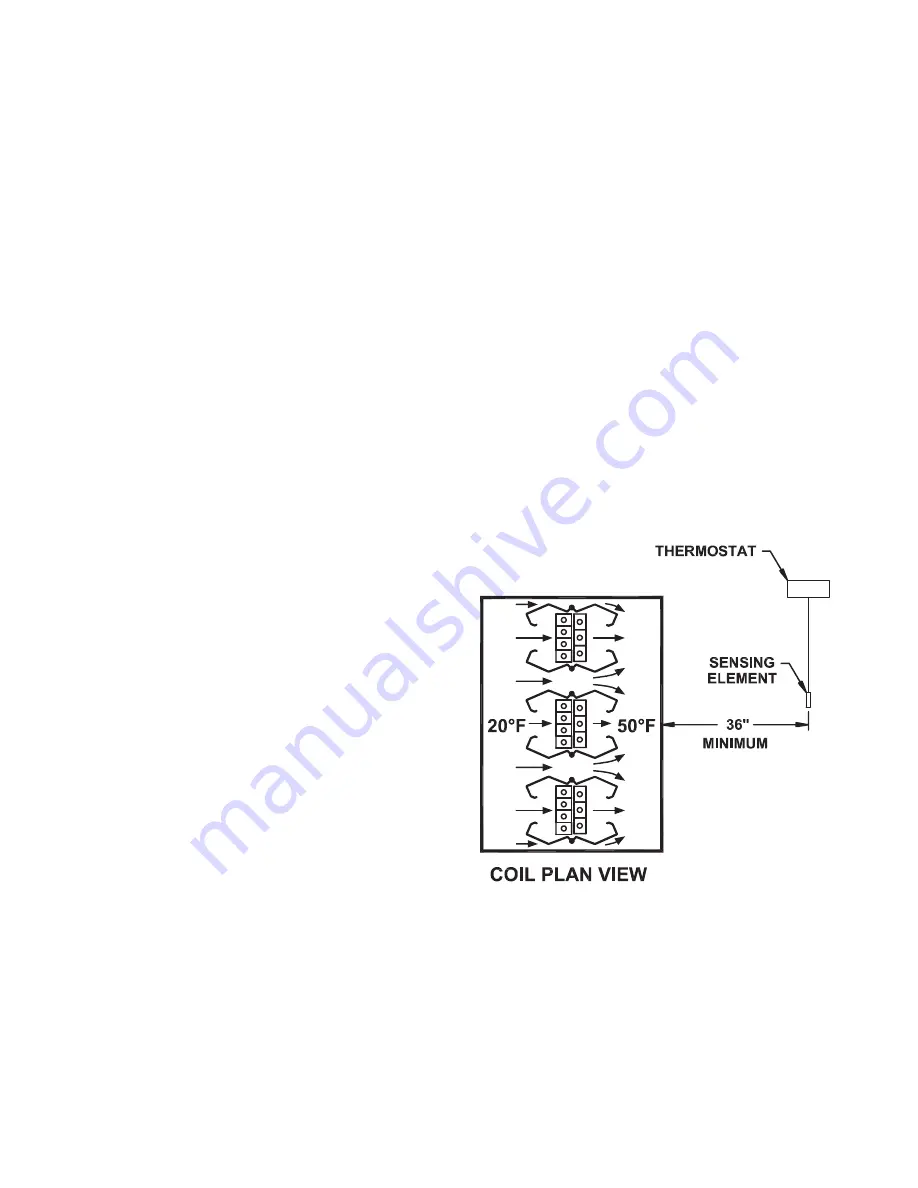
– 21 –
SECTION IX - START UP
A. Control Checks
1. On units with PNEUMATIC CONTROLS, take all
air pressure off. Dampers should go to full face
open position. Application of full air pressure will
close the dampers in the opposite direction. Adjust
the thermostat setting to be sure that when the
thermostat is calling for heat, the face opens and
the by-pass closes.
2. On units with electric controls, follow control
manufacturer’s instructions for shorting out
thermostat contacts to move the damper to close
the face one way, and then the by-pass. Adjust
thermostat setting to be sure operation is correct
so that when thermostat is calling for heat, the
face opens and the by-pass closes.
NOTE: On electric control units, since motors are
not spring return, dampers will remain in their last
operating position if the power is turned off.
B. Turning Steam On Unit
(Be sure lower header shipping bolts are removed)
1. Open all valves on return lines, including trap
valves and by-pass line around trap, to insure full
flow of condensate and steam from the coil.
2. Open all valves in drip trap line from steam main
before the coil to remove condensate and insure
dry steam in the main.
3. Open steam supply line to coil and blow through
coil with steam to purge coil of air and condensate.
4. Feel tube surfaces to assure even heating of all
surfaces before starting fans or opening outside
shutoff dampers.
5. Allow unit to “heat soak” at least 15 minutes as in
step #4.
6. Open dampers on the heating surface all the way
by adjusting thermostats or control air pressure to
units.
7. Open outside dampers.
8. Check coil surface for even heating as in step #4.
9. Slowly close by-pass around traps and check for
trap operation.
10. Adjust thermostat or control air pressure to normal
operating condition and start fan.
11. Set thermostat for desired temperature. Dampers
should position to produce required temperature
rise. Check traps for proper operation.
C. Turning Hot Water On Unit
(Be sure lower header(s) shipping bolts are removed)
1. Open return valve and supply valve. Purge all air
from coil and lines.
2. Feel surface to make sure unit is heating evenly
and that all air is purged from the coils.
3. Allow unit to “soak” for at least 10 minutes before
turning fan on.
4. Open outside air dampers and start fan.
5. Feel surface again to check for even heating as in
step #2.
6. Adjust balancing valve for desired GPM flow
through coil.
7. Set thermostat for desired temperature. Dampers
should position to produce required temperature
rise.
Figure 12 - Thermostat Location (C000677A)
Содержание MV
Страница 7: ... 7 Photo of Direct Coupled VIFB Entering Air Side Photo of Direct Coupled VIFB Leaving Air Side ...
Страница 8: ... 8 SECTION VI PARTS DRAWING Enlarged View C Section A A Section D D Elevation ...
Страница 11: ... 11 STEAM PIPING VIFB Coil Piping Diagram 15 psig and below W12A ...
Страница 12: ... 12 STEAM PIPING VIFB Coil Piping Diagram Above 15 psig W33B ...
Страница 13: ... 13 HOT WATER PIPING VIFB Coil Piping Diagram One or Three Row Coils W13B ...
Страница 14: ... 14 HOT WATER PIPING VIFB Coil Piping Diagram Two Row Coil W32B ...
Страница 15: ... 15 STEAM PIPING MV Coil Piping Diagram 15 psig and below W27A ...
Страница 16: ... 16 STEAM PIPING MV Coil Piping Diagram Above 15 psig W28A ...
Страница 17: ... 17 HOT WATER PIPING MV Coil Piping Diagram Two Row Coil W29A ...
Страница 19: ... 19 ELECTRIC AND PNEUMATIC CONTROLS D000756A ...
Страница 23: ... 23 ...
Страница 24: ...4830 TRANSPORT DRIVE DALLAS TX 75247 TEL 214 638 6010 www ljwing com ...