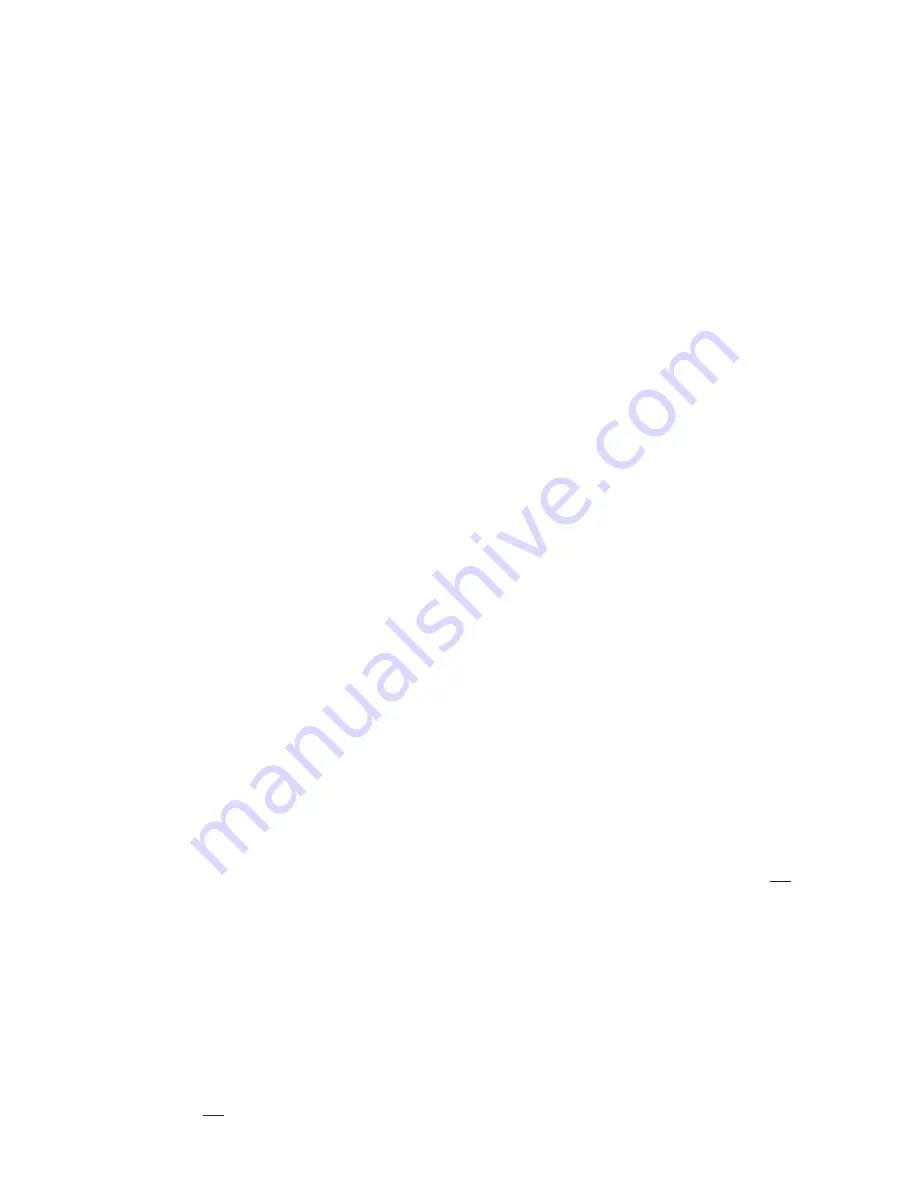
– 10 –
SECTION VII - PIPING
12. Each coil in a coil bank or in series should be
individually trapped and vented. MV coils require
two traps.
13. The steam trap should have provisions for air
venting. If the trap is non-venting, proper air vents
should be provided for each coil section to eliminate
condensable gases. All air vent lines should be
minimum one-inch diameter and properly pitched to
assure free venting of air. The venting device should
be located at least 12 inches above the bottom of the
coil casing. In low-pressure steam systems (15 psig
and below) in which a non-venting trap is used for
condensate removal, a thermostatic air trap should
be installed in a one-inch diameter air line bypassing
the condensate trap to the atmospheric return main.
An automatic air vent should be installed in a one-
inch diameter air line before the condensate trap
on systems with a vacuum return system. In high-
pressure steam systems (above 15 psig) in which a
non-venting trap is used for condensate removal, an
automatic air vent should be installed in a one- inch
diameter air line before the condensate trap. Do not
return vented air to the condensate return main.
14. A bypass line with valve should be installed around
the trap to permit operation of the coil during trap
maintenance. This feature will also provide better
coil start-up conditions when temperatures are
below freezing.
15. If condensate must be lifted above the coil return
level into overhead mains or if return mains are
pressurized, then a pump and receiver should be
installed between the condensate traps and return
mains.
16. Proper vacuum breakers should be furnished as
shown on the piping diagrams.
17. Swing check valves of 15-degree type should be
utilized to prevent condensate backup in the case
of steam system failure. Vertical lift check valves
or 45-degree swing check valves should not be
used as they require a higher head pressure of
water for opening.
Hot Water Systems
1. Install the casing level; tubes must be vertical.
2. Inlet and outlet mains should be anchored and
supported independently of the Wing coil.
3. Inlet piping must incorporate a flexible connector
to provide for at least 3/8" tube expansion and
contraction, and to allow the return header to float.
The integrity of the system depends in part on proper
piping. The following recommendations should be
diligently observed:
Steam Systems
1. All piping in contact with airflow or inside an air
hander should be insulated.
2. Install casing level; tubes must be vertical.
3. Full steam pressure must be supplied to the coil at
all times; modulating valves must not be used.
4. Steam mains, return mains and traps should be
anchored and supported independently of the
steam coil. Traps and condensate piping must be
supported on spring-loaded hangers or pads to
isolate forces from the return header.
5. Each return piping must incorporate a flexible
connector to insure at least 3/8" tube expansion and
contraction, and to allow the return header to float.
6. A drip trap should be installed in the steam supply
line and drip into the return main. This will prevent
steam line condensate from entering the unit with the
steam. Avoid dripping steam mains into the steam
coil or into the line between the steam coil and traps.
7. Use only bucket or thermostatic float traps for
condensate removal. Thermostatic traps should be
used for venting only.
8. Steam traps should be sized for three times the
calculated condensate loading at the coil design
conditions, based on the pressure differential across
the trap rather than the boiler pressure. Each trap
should be selected for the actual pressure differential
across the trap, not the boiler pressure. Pressure
differential is herein defined as the gauge pressure at
the trap minus the pressure in the return main.
9. The return connection should be full size of the
coil header and reduced at the trap. Use of a
reducing bushing on the coil return connection is not
recommended. (If shutoff valve, strainer and trap are
piped together with pipe nipples, then the pipe can
be reduced to the trap inlet size at the shutoff valve).
10. Strainers should be installed ahead of traps to
prevent dirt and sludge from affecting trap operation.
When the “closed circuit gravity return system” leads
directly to the boiler, the coil traps should be located
at least two feet above the water line of the boiler.
11. Risers should not be installed in condensate
return lines.
Содержание MV
Страница 7: ... 7 Photo of Direct Coupled VIFB Entering Air Side Photo of Direct Coupled VIFB Leaving Air Side ...
Страница 8: ... 8 SECTION VI PARTS DRAWING Enlarged View C Section A A Section D D Elevation ...
Страница 11: ... 11 STEAM PIPING VIFB Coil Piping Diagram 15 psig and below W12A ...
Страница 12: ... 12 STEAM PIPING VIFB Coil Piping Diagram Above 15 psig W33B ...
Страница 13: ... 13 HOT WATER PIPING VIFB Coil Piping Diagram One or Three Row Coils W13B ...
Страница 14: ... 14 HOT WATER PIPING VIFB Coil Piping Diagram Two Row Coil W32B ...
Страница 15: ... 15 STEAM PIPING MV Coil Piping Diagram 15 psig and below W27A ...
Страница 16: ... 16 STEAM PIPING MV Coil Piping Diagram Above 15 psig W28A ...
Страница 17: ... 17 HOT WATER PIPING MV Coil Piping Diagram Two Row Coil W29A ...
Страница 19: ... 19 ELECTRIC AND PNEUMATIC CONTROLS D000756A ...
Страница 23: ... 23 ...
Страница 24: ...4830 TRANSPORT DRIVE DALLAS TX 75247 TEL 214 638 6010 www ljwing com ...