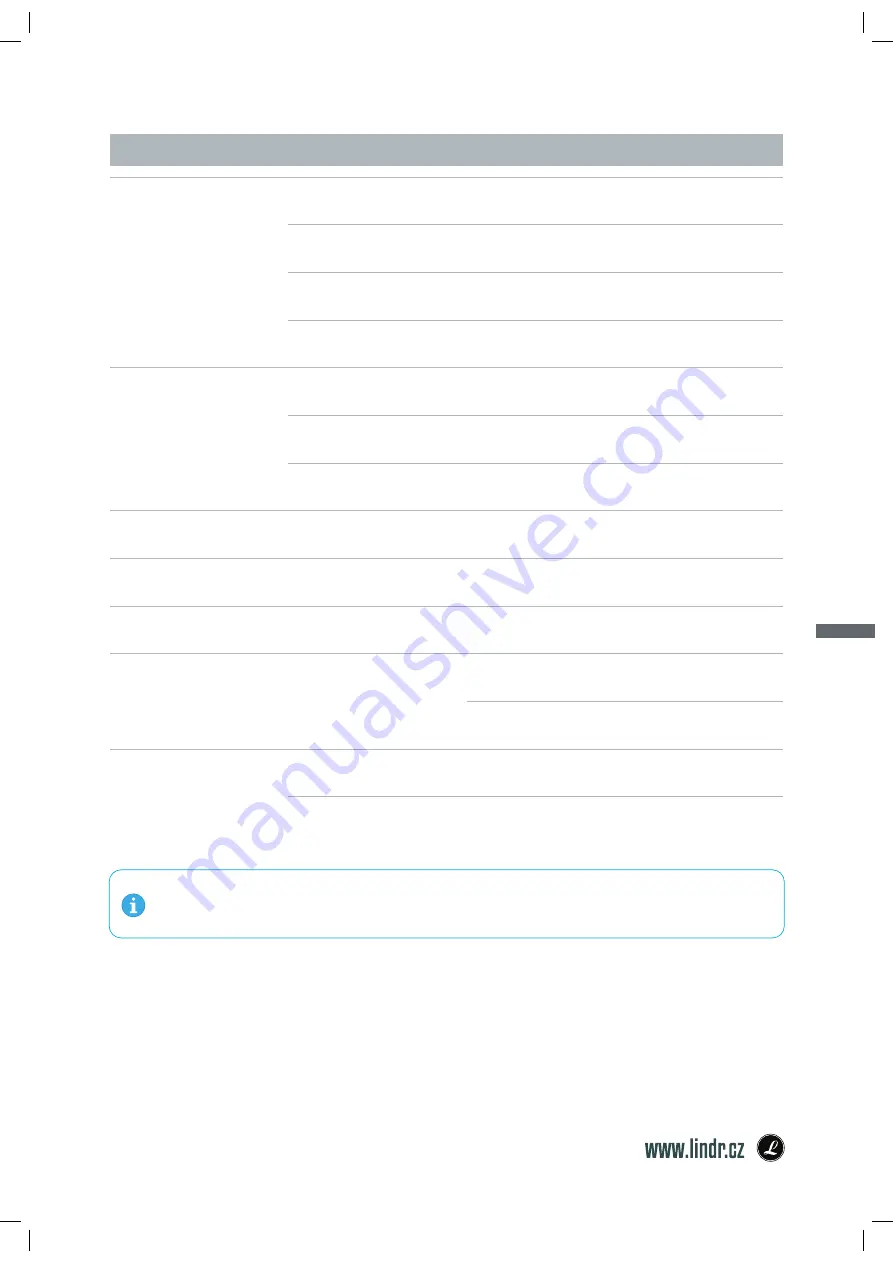
cont
ac
t-cooled dispensing s
ys
tem
17
NOTE:
If the defect persists even after the above steps are taken, contact a service centre.
18. TABLE OF MALFUNCTIONS
Malfunction
Cause
Removal
beverage does not
fl
ow
keg tapped incorrectly
check that the keg coupler lever is pushed down
device with built-in compressor - turn on the switch
water from sanitation froze
turn o
ff
the device; then wait until the beverage starts
fl
owing again (may take a few minutes, or hours!)
compensator is closed
move the compensator lever on the tap
beverage cooled insu
ffi
-
ciently
incorrect thermostat setting turn the thermostat knob to the right towards
number 7
poor air circulation
check the cleanliness of condenser plates
device overheats
place the device in a colder environment
tap jerks, drink sprays out
pressure too high
reduce delivery medium supply, reduce pressure in
the keg
air compressor does not
switch on
press the switch on the cooler
air compressor does not
switch o
ff
leakage
pull out and reinsert the air hose, tighten the nuts
on the keg coupler
beer foams excessively
reduce beverage temperature - turn the thermostat
knob to the right
regulate
fl
ow rate by pushing the compensator lever
up
speed
fi
ttings leaking
hose poorly inserted
pull out the hose, check that the end of the hose is
fl
at (not at an angle), level o
ff
with a knife if needed
scratches on the hose
pull out the hose and shorten by ca. 2 cm
Do not forget to specify the following:
• type of defect
• product type
• production year
• product's serial number (found on the machine plate)