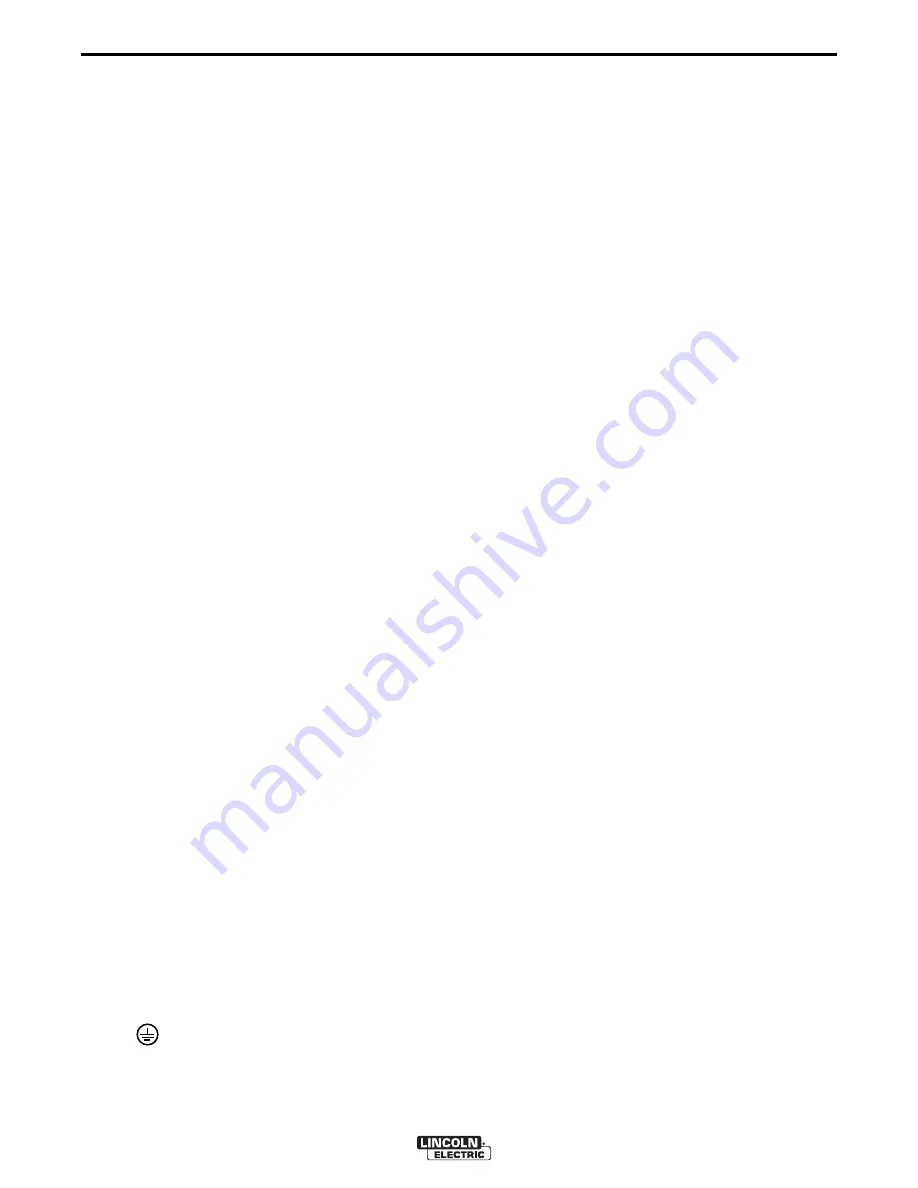
B-4
OPERATION
IDEALARC® DC-1000
B-4
TO SET POLARITY
Turn off the DC-1000 and connect the electrode cable
to the “Positive” or “Negative” studs depending upon
the electrode polarity desired. Connect the work cable
to the other stud. (See “Output Connections”).
Set the “Electrode Negative-Electrode Positive” switch
to correspond to the polarity of the electrode cable
connection. This switch setting is necessary for proper
operation of some Lincoln wire feeders and does not
change the welding polarity.
Starting the Machine -
The push button power “on”
switch at the extreme right side of the control panel
energizes and closes the three phase input contactor
from a 110 volt auxiliary transformer. This in turn
energizes the main power transformer.
The white light below the stop-start button indicates
when the input contactor is energized.
Output Control -
The output control in the center of
the control panel is a continuous control of the machine
output. The control may be rotated from min. to max.
while under load to adjust the machine output.
The machine is equipped with line voltage
compensation as a standard feature. This will hold the
output relatively constant except at maximum output of
the machine, through a fluctuation of +/- 10% of input
line voltage.
Output Control at DC-1000 or Output Control
Remote Switch
The toggle switch on the control panel labeled
“Panel” / “Remote” gives the operator the option of
controlling the output at the machine control panel or at
a remote station. For remote control, the toggle switch
is set in the “Remote” position and controlled at the
wire feed unit control or by connecting a K775 control
to the appropriate terminals (as indicated on the
connection diagram) on the terminal strip at the front of
the machine. For control at the machine
control panel, the toggle switch is set in the “Panel”
position.
Remote Output Control -
(Optional)
The K775 Remote Output Control consists of a control
box with 28 ft. (8.4m) of four conductor cable. This
connects to terminals 75, 76, 77 on the terminal strip,
and the case grounding screw so marked with the
symbol on the machine. These terminals are made
available by opening the terminal access cover on the
left side of the case front. This control will give the
same control as the output control on the machine.
Mode Switch
The toggle switch labeled CV Innershield, CV
Submerged Arc, CC Submerged Arc is used to select
the proper welder characteristics for the process being
used.
SET-UP FOR VARIOUS PROCEDURES
1.
Selection of mode switch position -
There are
several general rules to follow in the selection of
the mode switch position.
a. Use the CV Innershield mode for all FCAW
and GMAW processes. The CV Innershield
mode is also used for air carbon arc using
carbon rods up to and including 5/8”
(15.9mm) dia.
Welding with NR®-151, 202, 203 and other
electrodes below 20 volts, is not
recommended.
b. Use the CV Submerged Arc mode for all
submerged arc welding. This applies to both
low and high travel speeds.
c. The CC Submerged Arc mode is available for
high current large puddle submerged arc
procedures that cannot be done as well with
the constant voltage mode. CC mode should
be used for 3/16” (4.8mm) diameter electrode
and above where high current surges cause
machine shutdown when starting. This occurs
primarily when the slag ball is not cut from the
electrode prior to starting. (Also requires a
wire feeder that has a constant current mode
- i.e. NA-3S).
NOTE:
Some processes and procedures may be
better with the mode switch in the other CV position.
If the mode switch position initially selected is not
producing the desired results, then place the mode
switch in the other CV position and make a test weld.
Then use the CV mode switch position that gives the
desired results.
2.
NA-3 -
The NA-3 should be set for the mode being
used on the power source. If using either of the
CV modes, the NA-3 CC board switch should be
set for CV. If the power source is used in the CC
mode, then the NA-3 CC board mode switch
should be placed in the CC position.
Содержание IDEALARC DC-1000
Страница 7: ...7 NOTES IDEALARC DC 1000 7 ...
Страница 31: ...P 720 A jpg Index of Sub Assemblies 12480 2 DC 1000 12480 Printed 09 24 2015 at 08 32 31 Produced by Enigma ...
Страница 33: ...No Image Miscellaneous Items 4 DC 1000 12480 Printed 09 24 2015 at 08 32 31 Produced by Enigma ...
Страница 37: ...P 720 C_2 jpg Case Front Control Box 8 DC 1000 12480 Printed 09 24 2015 at 08 32 31 Produced by Enigma ...
Страница 40: ...P 720 D jpg Case Back Assembly DC 1000 12480 11 Printed 09 24 2015 at 08 32 31 Produced by Enigma ...
Страница 42: ...P 720 E jpg Base Fan Roof and Case Sides DC 1000 12480 13 Printed 09 24 2015 at 08 32 31 Produced by Enigma ...
Страница 44: ...P 720 F jpg Output Rectifier Choke Assembly DC 1000 12480 15 Printed 09 24 2015 at 08 32 31 Produced by Enigma ...
Страница 47: ...P 720 G jpg Lift Bale Transformer Assembly 18 DC 1000 12480 Printed 09 24 2015 at 08 32 31 Produced by Enigma ...
Страница 49: ...P 720 H jpg S78 Contactor 20 DC 1000 12480 Printed 09 24 2015 at 08 32 31 Produced by Enigma ...