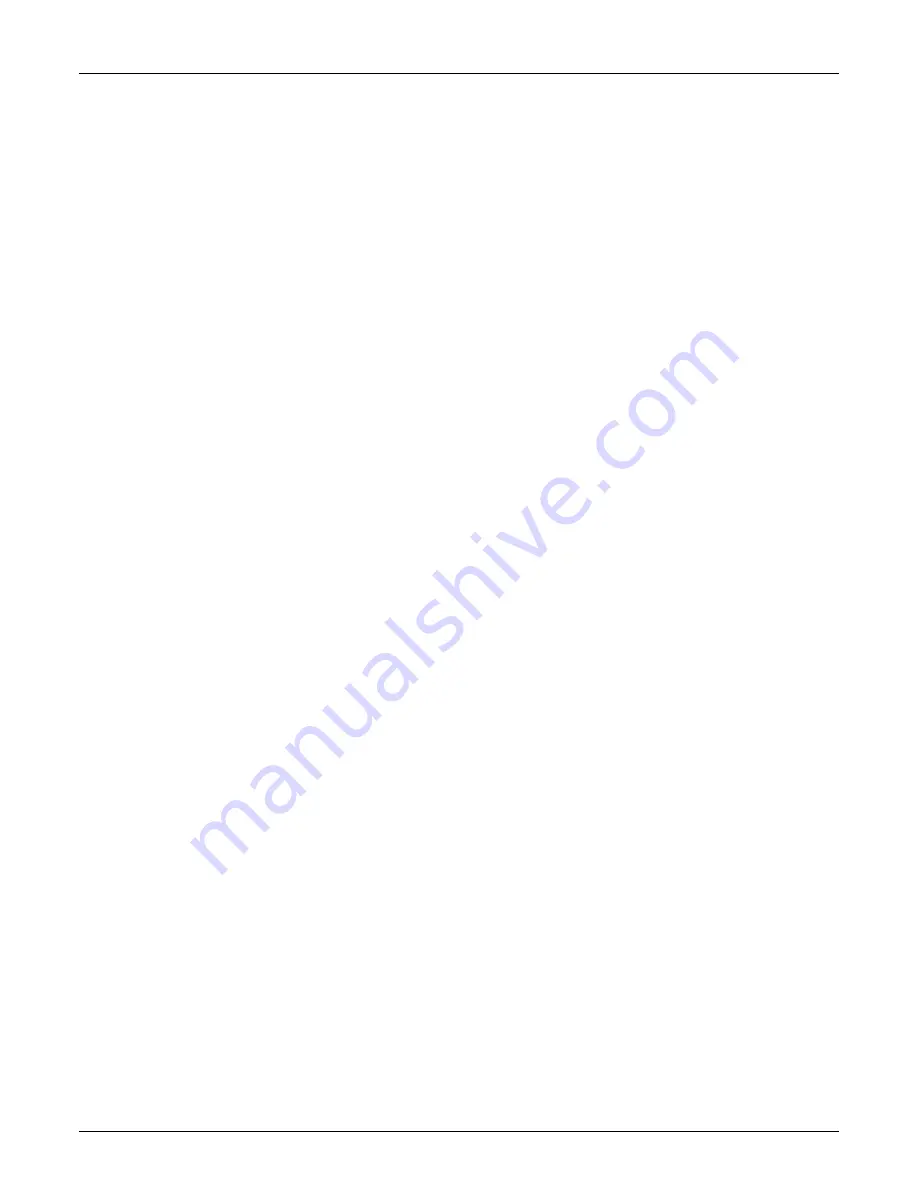
Spirit II User’s Manual
Appendix A: Electromagnetic Compatibility (EMC)
This information is subject to the controls of the Export Administration Regulations [EAR]. This information shall not be provided to
non-U.S. persons or transferred by any means to any location outside the United States contrary to the requirements of the EAR.
A-1
Appendix A:
Electromagnetic Compatibility (EMC)
Background
The 380V 50/60Hz and 415V 50/60Hz CE marked Spirit plasma cutting systems are
manufactured to comply with the European standard EN 60974-10 (Electromagnetic
compatibility (EMC) – Product standard for arc welding equipment). The system has
been tested in accordance with CISPR 11, EMC classification – Group 2 ISM (Class A).
The limits used in this standard are based on practical experience. However, the ability
of plasma cutting equipment to work in a compatible manner with other radio and
electronic systems is greatly influenced by the manner in which it is installed and used.
For this reason, it is important that the plasma cutting equipment be installed and used
in accordance with the information below if electromagnetic compatibility is to be
achieved.
Plasma cutting equipment is primarily intended for use in an industrial environment.
There may be potential difficulties in ensuring electromagnetic compatibility in other
environments.
Installation and Use
The user is responsible for installing and using the plasma cutting equipment according
to the manufacturer’s instructions. If electromagnetic disturbances are detected then it
shall be the responsibility of the user of the plasma cutting equipment to resolve the
situation with the technical assistance of the manufacturer. In some cases this remedial
action may be as simple as earthing the plasma cutting circuit, see Note. In other cases
it could involve constructing an electromagnetic screen enclosing the plasma power
source and the work, complete with associated input filters. In all cases,
electromagnetic disturbances shall be reduced to the point where they are no longer
troublesome.
Note: The plasma cutting circuit may or may not be earthed for safety reasons.
Changing the earthing arrangements should only be authorized by a person who is
competent to assess whether the changes will increase the risk of injury, e.g. by
allowing parallel plasma cutting current return paths which may damage the earth
circuits of other equipment. Further guidance is given in IEC 974-13
Arc welding
equipment – Installation and use.