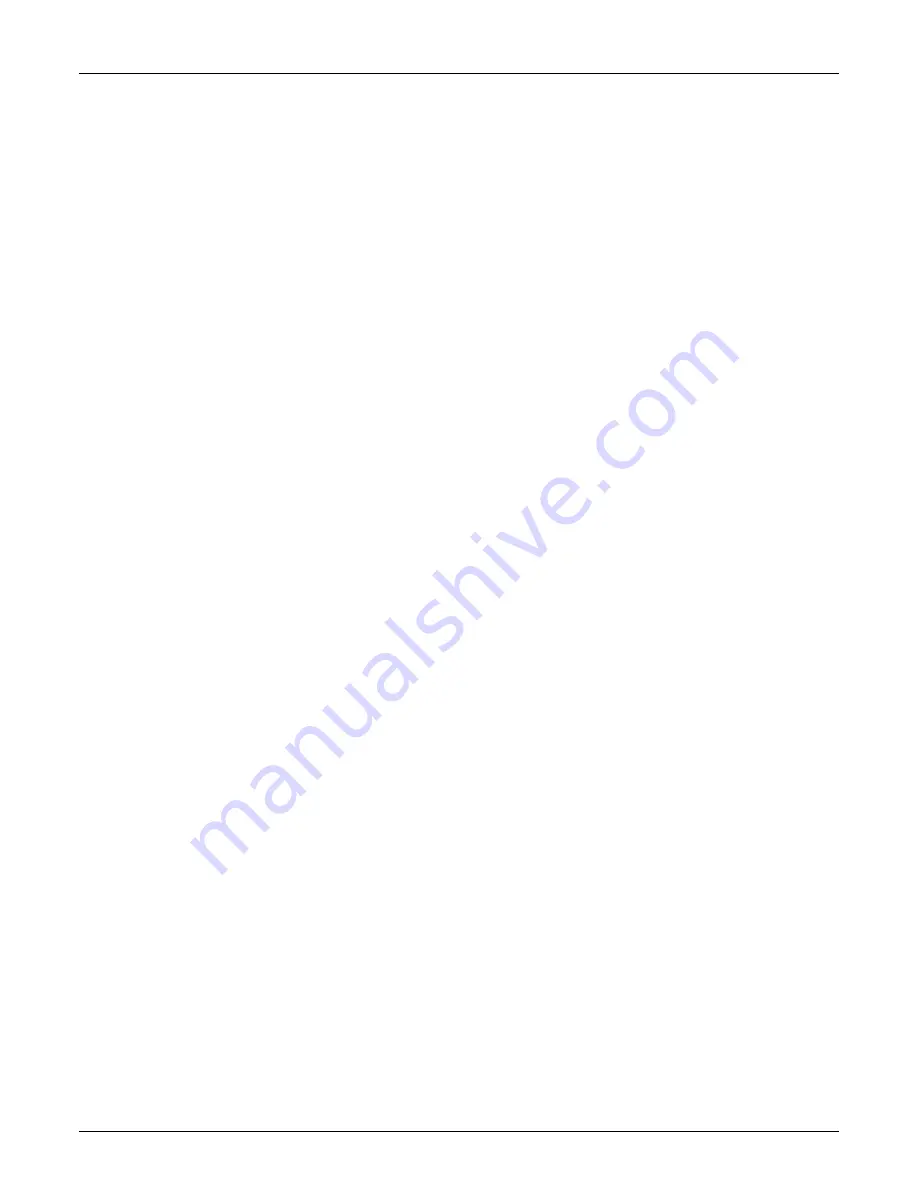
Spirit II User’s Manual
Section 4: Operation with Automatic Gas Console
This information is subject to the controls of the Export Administration Regulations [EAR]. This information shall not be provided to
non-U.S. persons or transferred by any means to any location outside the United States contrary to the requirements of the EAR.
4-9
Cut Quality
Before the optimum cutting condition can be achieved on a particular material type and
thickness, the machine operator must have a thorough understanding of the cutting
characteristics of the Spirit system. When the cut quality is not satisfactory, the cutting
speed, torch height, or gas pressures may need to be adjusted in small increments until
the proper cutting condition is obtained. The following guidelines should be useful in
determining which cutting parameter to adjust.
Note: Before making any parameter changes, verify that the torch is square to
the workpiece. Also, it is essential to have the correct torch parts in place and to
ensure that they are in good condition. Check the electrode for excessive wear
and the nozzle and shield cap orifices for roundness. Also, check the parts for
any dents or distortions. Irregularities in the torch parts can cause cut quality
problems.
1. A positive cut angle (top dimension of piece smaller than the bottom dimension)
usually occurs when the torch standoff distance is too high, when cutting too fast, or
when excessive power is used to cut a given plate thickness.
2. A negative cut angle (top dimension of piece larger than the bottom dimension)
usually occurs when the torch standoff distance is too low or when the cutting speed
is too slow.
3. Top dross usually occurs when the torch standoff distance is too high.
4. Bottom dross usually occurs when the cutting speed is either too slow (slow-speed
dross) or too fast (high-speed dross). Low-speed dross is easily removed, while
high-speed dross usually requires grinding or chipping off. When using oxygen as
the shielding gas, bottom dross can sometimes be removed by increasing the shield
gas pressure. However, increasing the shield pressure too much can cause cut face
irregularities (see below). Bottom dross also occurs more frequently as the metal
heats up. As more pieces are cut out of a particular plate, the more likely they are to
form dross.
5. When using oxygen as a shielding gas, cut face irregularities usually indicate that
the shield gas pressure is too high or the torch standoff distance is too low.
6. A concave cut face usually indicates that the torch standoff distance is too low or the
shield gas pressure is too high. A convex cut face usually indicates that the torch
standoff distance is too high or the shield gas pressure is too low.
7. Note that different material compositions have an effect on dross formation.
8. If the material is not being completely severed, the likely causes are that the cutting
current is too low, the travel speed is too high, the gas pressures are incorrect, the
incorrect gas types are selected, the incorrect consumables are installed in the
torch, or the consumables are worn.