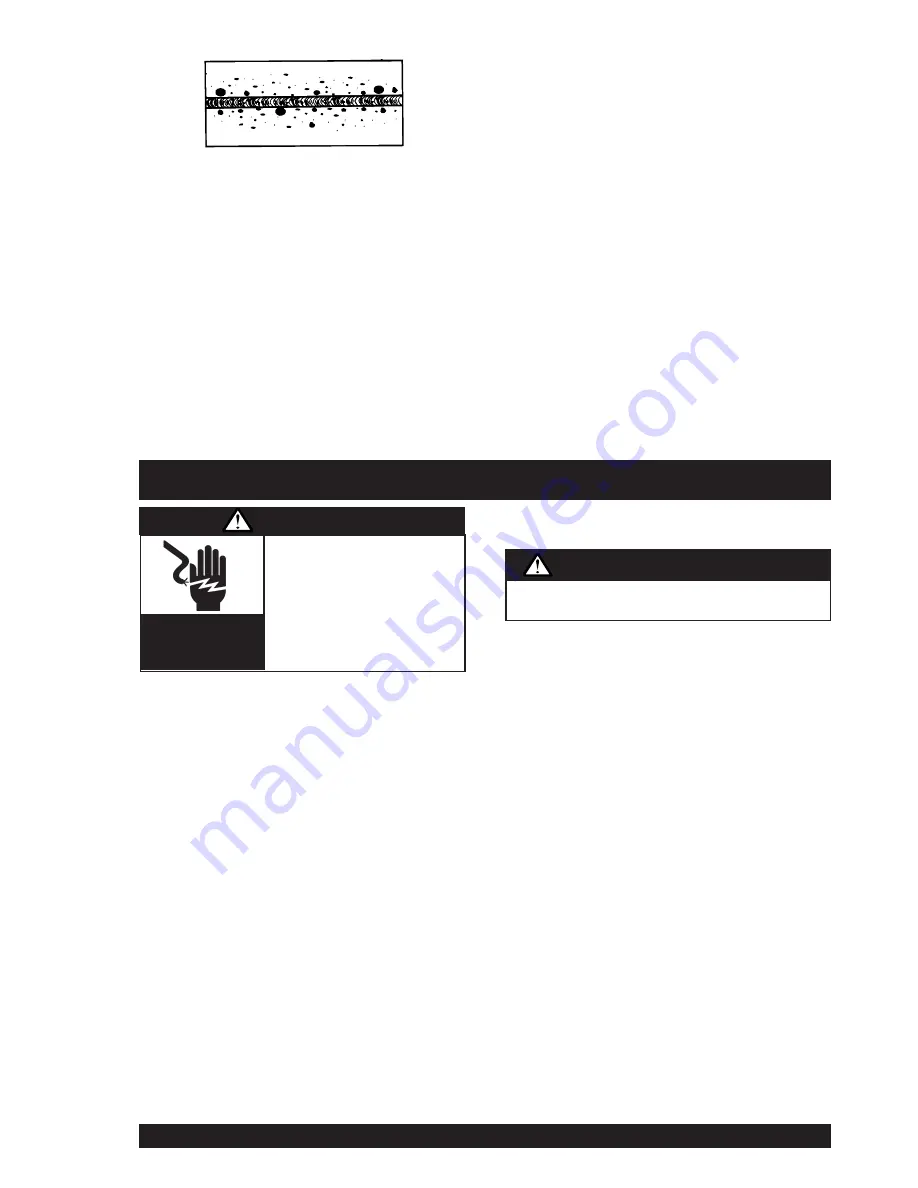
IM6016
REDI-MIG
®
Plus 215C, 255C, 255S
Page 21
To Reduce Spatter
(in order of importance):
1. Increase voltage.
2. Increase torch angle.
3. Decrease stickout.
4. Increase WFS (wire feed speed).
5. Decrease travel speed.
6. Check for correct gas, if used.
To Correct Poor Penetration
(in order of importance):
1. Decrease stickout.
2. Increase WFS (wire feed speed).
3. Increase voltage.
4. Decrease speed.
5. Decrease torch angle.
6. Check for correct gas, if used.
If Arc Blow Occurs
(in order of importance):
Note:
Try different ground connection locations before
adjusting procedures.
1. Decrease torch angle.
2. Increase stickout.
3. Decrease voltage.
4. Decrease WFS (wire feed speed.
5. Decrease travel speed.
To Eliminate Stubbing* (in order of importance):
1. Increase voltage
2. Decrease WFS (wire feed speed)
3. Decrease stickout
4. Increase torch angle
* Stubbing occurs when the electrode drives through the
molten puddle and hits the bottom plate tending to push
the gun up.
Proper Gun Handling
Most feeding problems are caused by improper handling of
the gun cable or electrodes.
1. Do not kink or pull the gun around sharp corners
2. Keep the gun cable as straight as practical when
welding.
3. Do not allow dolly wheels or trucks to run over the
cables.
4. Keep the cable clean.
5. Use only clean, rust-free electrode. Lincoln electrodes
have proper surface lubrication.
6. Replace contact tip when it becomes worn or the end is
fused or deformed.
6.1 Routine Maintenance
General
In extremely dusty locations, dirt may clog the air passages
and cause the welder to run hot. Blow dirt out of the welder
with low-pressure air at regular intervals to eliminate
excessive dirt and dust build-up on internal parts.
The fan motor has sealed ball bearings which require no
service.
Welding Thermal Overload Protection
The REDI-MIG
®
Plus and Powerplus units have built-in
protective thermostats that respond to excessive
temperature. They open the wire feed and welder output
circuits if the machine exceeds the maximum safe operating
temperature because of a frequent overload, or high
ambient temperature plus overload. The over temperature
light on the control panel glows if thermostats open. The
thermostats automatically reset when the temperature
reaches a safe operating level. The fan will stay on when
the machines welding and feeding are disabled during
thermostatic over temperature protection.
6.2 Gun and Cable Maintenance
Cable Cleaning
Clean cable liner after using approximately 150kg of
electrode. Remove the cable from the wire feeder and lay
it out straight on the floor. Remove the contact tip from
the gun. Using an air hose and approx. 350 kPa (50psi)
pressure, gently blow out the cable liner from the gas
diffuser end.
Flex the cable over its entire length and again blow out the
cable. Repeat this procedure until no further dirt comes out.
6.3 Gun Tips and Nozzles
The gun tip should be replaced when worn. Replace with
the correct size for the wire type and diameter. Too large
a tip for the electrode wire will cause arcing within the gun
cable and possible jamming of the wire within the cable .
Remove spatter from inside of gas nozzle and from tip after
each 10 minutes of arc time or as required.
Drive Rolls and Guide Tubes
After every coil of wire, inspect the wire drive mechanism.
Clean it as necessary by blowing with low pressure
compressed air. Do not use solvents for cleaning the idle
roll because this may wash the lubricant out of the bearing.
All drive rolls are stamped with the wire sizes they will feed.
If a wire size other than that stamped on the roll is to be
used, the drive roll must be changed.
Avoiding Wire Feeding Problems
Wire feeding problems can be avoided by observing the
following gun handling procedures:-
1. Do not kink or pull gun cable around sharp corners.
2. Keep the gun cable as straight as possible when
welding or feeding electrode through cable.
3. Keep gun cable clean by following maintenance
instructions.
4. Use only clean, rust-free electrode. Lincoln Electric
electrode has proper surface lubrication.
5. Replace contact tip when the arc starts to become
unstable or the contact tip end is fused or deformed.
6.4 Input Lead
If the supply cord is damaged, it must be replaced with a
special cord. Refer spare part list.
Excessive pressure at the start may cause dirt to form
a plug.
CAUTION
WARNING
ELECTRIC
SHOCK
can kill
• Have an electrician install and
service this equipment.
• Turn the input power off at the
fuse box, or unplug input lead
before working on equipment.
• Do not touch electrically hot
parts.
Section 6 - MAINTENANCE