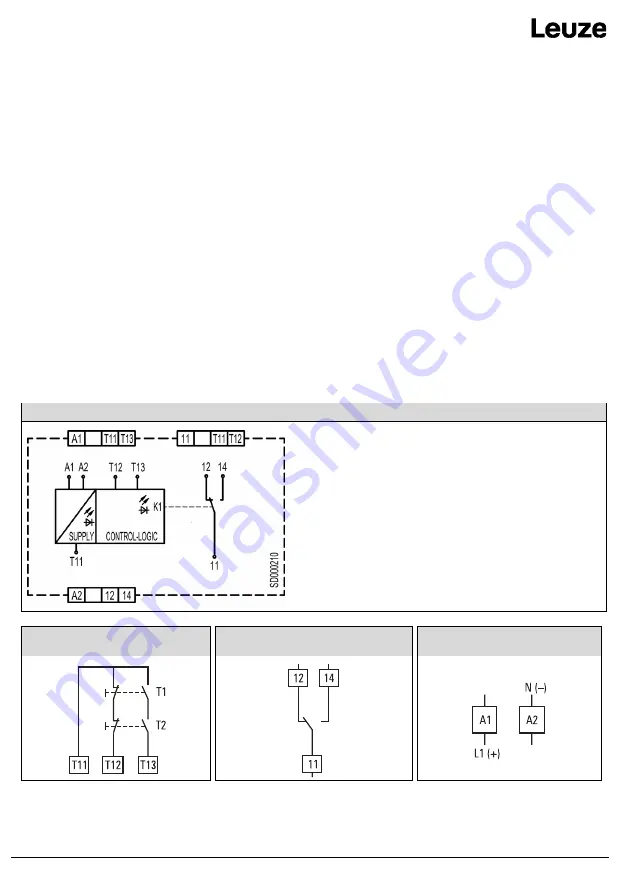
Leuze electronic GmbH + Co. KG
In der Braike 1 D-73277 Owen
We reserve the right to make changes
[email protected] • www.leuze.com
Tel. +49 (0) 7021 573-0
03/2020 - 50134631-02 - 5/20
Notes
•
The two-hand control device and the upstream and
downstream parts of the controller must conform to the
applicable VDE regulations and the safety requirements set
out in ISO 13851:2019, EN 692, and EN 693.
•
The performance level (PL) and safety category in
accordance with EN ISO 13849-1 depend on the external
wiring, the application case, the choice of control device
and how this is physically arranged on the machine.
•
The user must carry out a risk assessment in accordance
with ISO 14121-1.
•
The entire system/machine must undergo validation in
accordance with the applicable standards on the basis of
this.
•
The stated performance level will only be achieved if,
taking into account the prevailing device load (see
EN ISO 13849-1 Table C.1) and the application case, an
average number of switching cycles per year is not
exceeded (see EN ISO 13849-1, C.4.2 and Table K.1).
With an electrical service life of 1,000,000 switching cycles,
at 1 A (resistive load and 230 V AC), the maximum number
of cycles, for example, can be calculated as 1,000,000 /
0.1 x 39 = 256,410 switching cycles/year.
•
Correct functioning and monitoring of synchronous
operation must be checked at least once a year.
•
Only the enabling current path 11-14 may be used to
enabled hazardous movement. The current signalling path
11-12 is only permitted for non-safety-related tasks.
•
Operating the device other than specified can result in
malfunctions or destruction of the device.
•
The device must be installed so that there is no risk of
short circuits, in particular between T11 and T13.
•
The device must be checked to ensure it is in perfect
working order before commissioning, after replacement of
modules and/or in the case of changes to an installation
that has already undergone acceptance.
•
The expansion units of the MSI-SR-CM series or external
contactors with positively-driven contacts can be used for
duplicating the enabling current paths.
•
The contacts must be fused with maximum 4 A operating
class gG.
•
External loads must be equipped with a suitable
protection circuit for the load (e.g. RC elements, varistors,
suppressors, etc.) in order to reduce electromagnetic
interference and increase the service life of the output
switching elements.
•
The application-specific standards must be observed
when installing and operating the device.
•
The switch-on peak current must be considered when
connecting solenoid switches with reed contacts or
sensors with semiconductor outputs (see Technical data).
•
The safety functions have not been checked by UL. The
certification process has been carried out in accordance
with the requirements for general applications as
stipulated by UL508.
3
Connection diagrams
MSI-SR-2H1 AC/DC 24 V
1 Two-hand pushbuttons T1 and T2
2 - 1 changeover contact (enabling cur-
rent path and current signalling path)
3 - Power supply