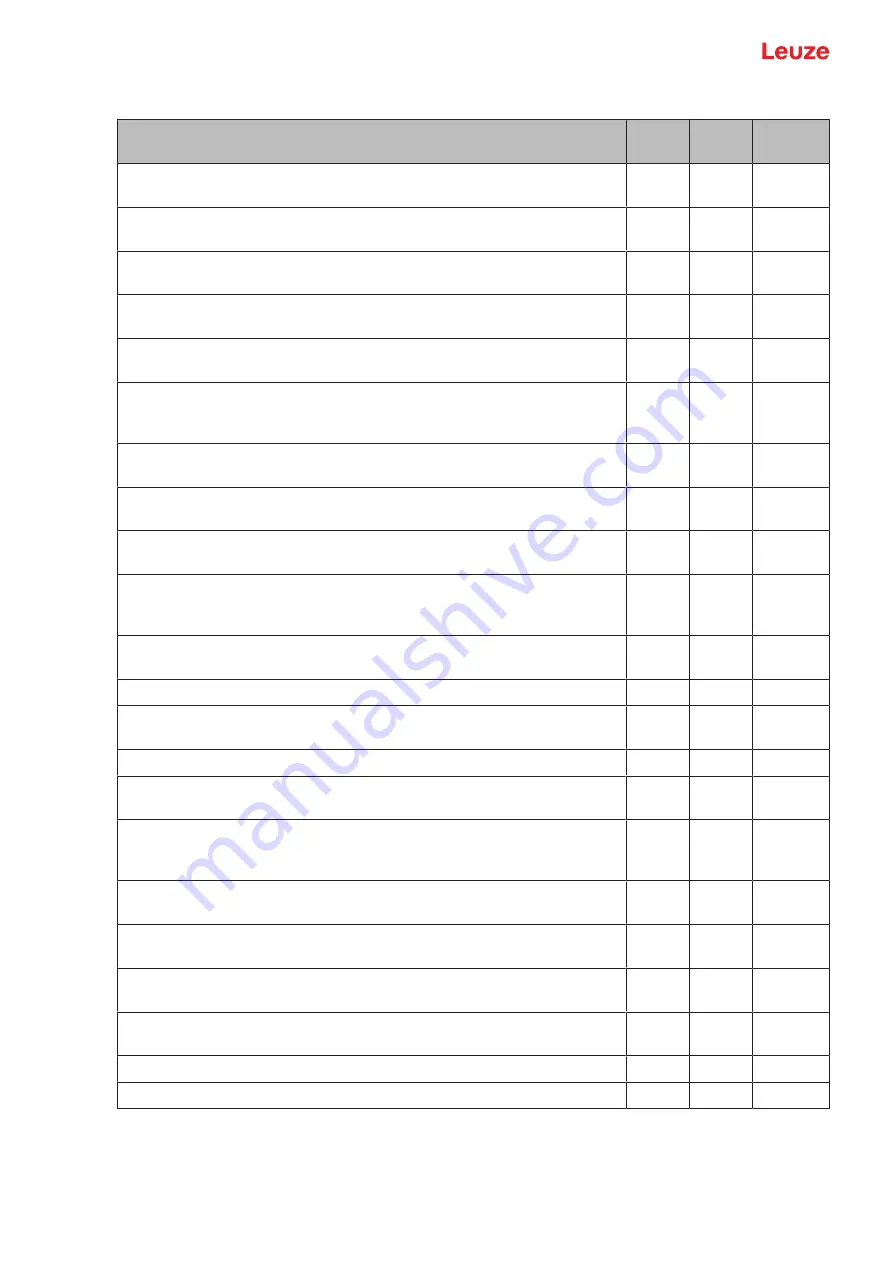
Testing
Leuze electronic GmbH + Co. KG
ELC 100
30
Tab. 8.1:
Checklist for integrator – to be performed prior to the initial start-up and following modifications
Check:
Yes
No
not ap-
plicable
Is the safety sensor operated acc. to the specific environmental conditions
that are to be maintained (see chapter 12 "Technical data")?
Is the safety sensor correctly aligned and are all fastening screws and con-
nectors secure?
Are safety sensor, connection cables, connectors, protection caps and
command devices undamaged and without any sign of manipulation?
Does the safety sensor satisfy the required safety level (PL, SIL, cate-
gory)?
Are both safety-related switching outputs (OSSDs) integrated in the down-
stream machine control acc. to the required safety category?
Are switching elements that are controlled by the safety sensor monitored
according to the required safety level (PL, SIL, category) (e.g., contactors
through EDM)?
Are all points of operation near the safety sensor accessible only through
the protective field of the safety sensor?
Are the necessary additional protective devices in the immediate surround-
ings (e.g., safety guard) properly mounted and secured against tampering?
If it is possible to be present undetected between the safety sensor and
point of operation: is an assigned start/restart interlock functional?
Is the command device for unlocking the start/restart interlock mounted in
such a way that it cannot be reached from within the danger zone and so
that the complete danger zone can be seen from the installation location?
Has the maximum stopping time of the machine been measured and docu-
mented?
Is the required safety distance maintained?
Does interruption with a test object intended for this purpose cause the
dangerous movement(s) to stop?
Is the safety sensor effective during the entire dangerous movement(s)?
Is the safety sensor effective in all relevant operating modes of the ma-
chine?
Is start-up of dangerous movements reliably prevented if an active light
beam or the protective field is interrupted with a test object intended for this
purpose?
Were distances to reflective surfaces taken into account during configura-
tion and no reflection bypasses subsequently detected?
Are notices for regular testing of the safety sensor legible to the operator
and are they located in a highly visible location?
Are settings that could result in an unsafe state possible only by means of
key, password or tool?
Are there incentives that pose stimulus for tampering?
Were the operators instructed prior to starting work?