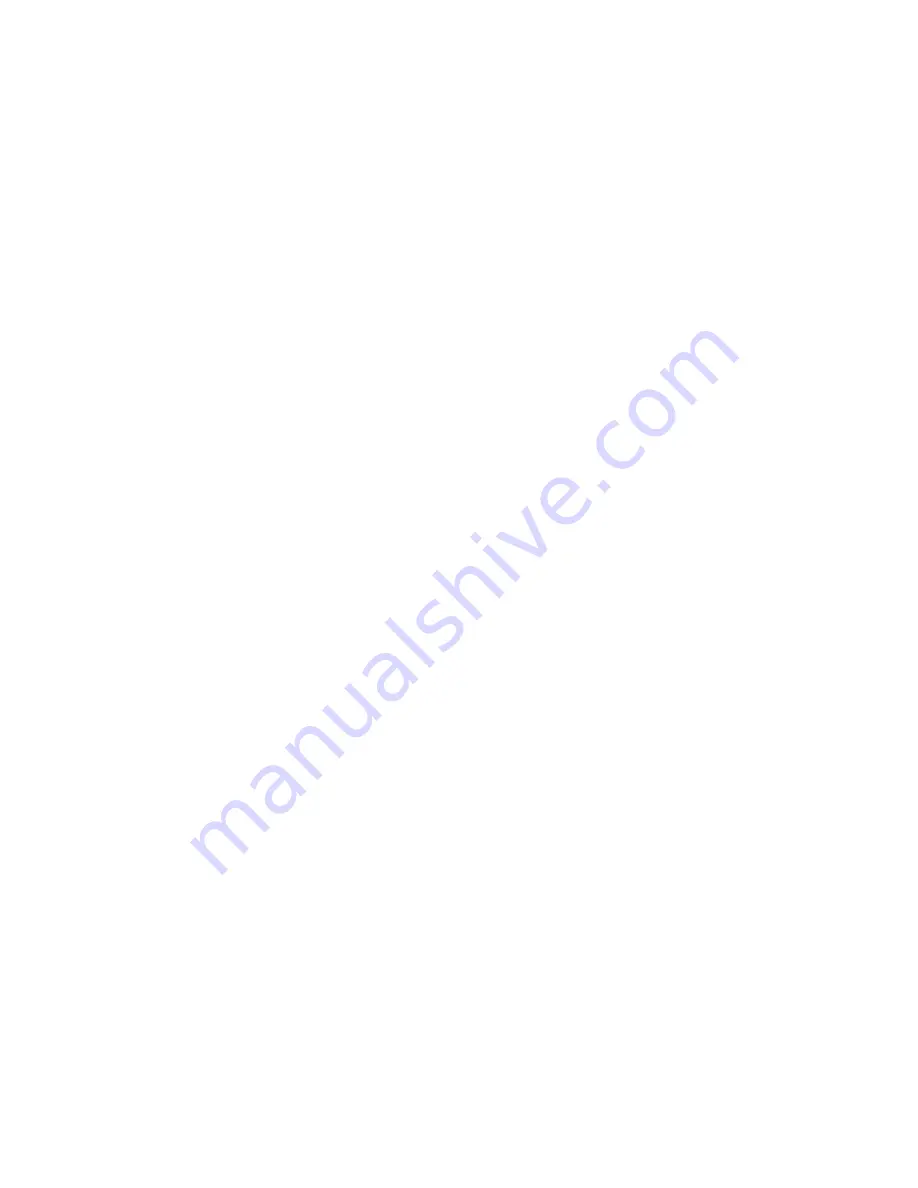
29
SENSOR
TROUBLESHOOTING
AND
REPLACEMENT
When
a
sensor
is
disconnected
or
no
longer
in
proper
working
condition,
an
error
message
is
displayed
on
the
controller
(see
complete
error
list
starting
on
page
24).
If
this
sensor
is
on
the
master
printed
circuit
board
(PCB)
then
the
error
will
be
accompanied
by
a
flashing
red
LED
light
on
the
overlay.
TURN
OFF
POWER
TO
THE
NUCLEUS
CONTROL
BOX
BEFORE
TROUBLESHOOTING
OR
REPLACING
ANY
WIRES
AND
SENSORS.
USE
ELECTROSTATIC
DISCHARGE
SAFE
TOOLS
WHEN
WORKING
INSIDE
OF
THE
CONTROL
BOX!
1. Determine
if
the
sensor
is
truly
broken
and
not
a
simple
disconnection.
Identify
the
appropriate
sensor
wires
inside
of
the
control
box
(see
wiring
diagram
on
page
28).
Check
the
connection
by
pulling
gently
on
the
wire,
best
done
with
needle
nose
pliers.
If
the
wire
can
be
easily
removed
from
the
connector,
reinstall
and
tighten
connection
with
small
flathead
screwdriver.
For
pressure
sensors
ensure
that
the
sensor
and
wire
harness
are
properly
connected
as
well.
2. If
the
sensor
is
properly
connected
to
the
controller
and
the
condition
persists,
then
the
sensor
needs
to
be
replaced.
Identify
the
appropriate
sensor
wires
inside
of
the
control
box
(see
wiring
diagram
on
page
28).
Using
an
flathead
screwdriver,
loosen
the
connections
between
the
board
and
wires.
Remove
the
wires
from
the
connectors.
3. Remove
the
disconnected
wires
from
the
control
box.
Begin
by
loosening
the
cable
gland
nut
on
the
bottom
of
the
box.
Motor
wires,
T1,
T2,
T3,
T4,
P1,
P2
wires
run
through
the
right
‐
side
cable
gland,
while
all
other
sensors
run
through
the
left
‐
side
cable
gland.
Open
the
cable
sleeve
and
fully
remove
the
defective
wires.
4. Shut
down
hot,
cold
and
outlet
ball
valves
and
depressurize
the
pipes.
Remove
the
defective
sensor
from
the
piping
and
install
new
sensor
in
its
place.
For
RTD
probes
new
compression
fittings
are
required.
Do
not
overtighten
compression
nuts
before
re
‐
pressurizing
valve
(See
Page
30).
Replacement
pressure
sensors
will
also
include
a
new
harness.
5. Snake
new
sensor
wires
through
the
cable
gland.
Install
replacements
wires
to
their
corresponding
connectors
on
the
PCB.
Refer
to
wiring
diagram
on
page
28
for
the
correct
configuration.
6. Bundle
any
loose
wires
from
the
new
sensor
and
place
into
the
cable
sleeve.
Place
end
of
the
cable
sleeve
into
the
cable
gland
and
tighten
the
gland
nut
to
secure
the
sleeve
in
place.
Take
care
to
not
put
excess
strain
on
the
end
of
the
sensor’s
wires.
7. Open
hot,
cold
and
outlet
ball
valves
to
pressurize
valve.
Introduce
power
to
the
Nucleus
control
box
and
confirm
that
the
replacement
sensor
is
providing
proper
feedback
and
data.