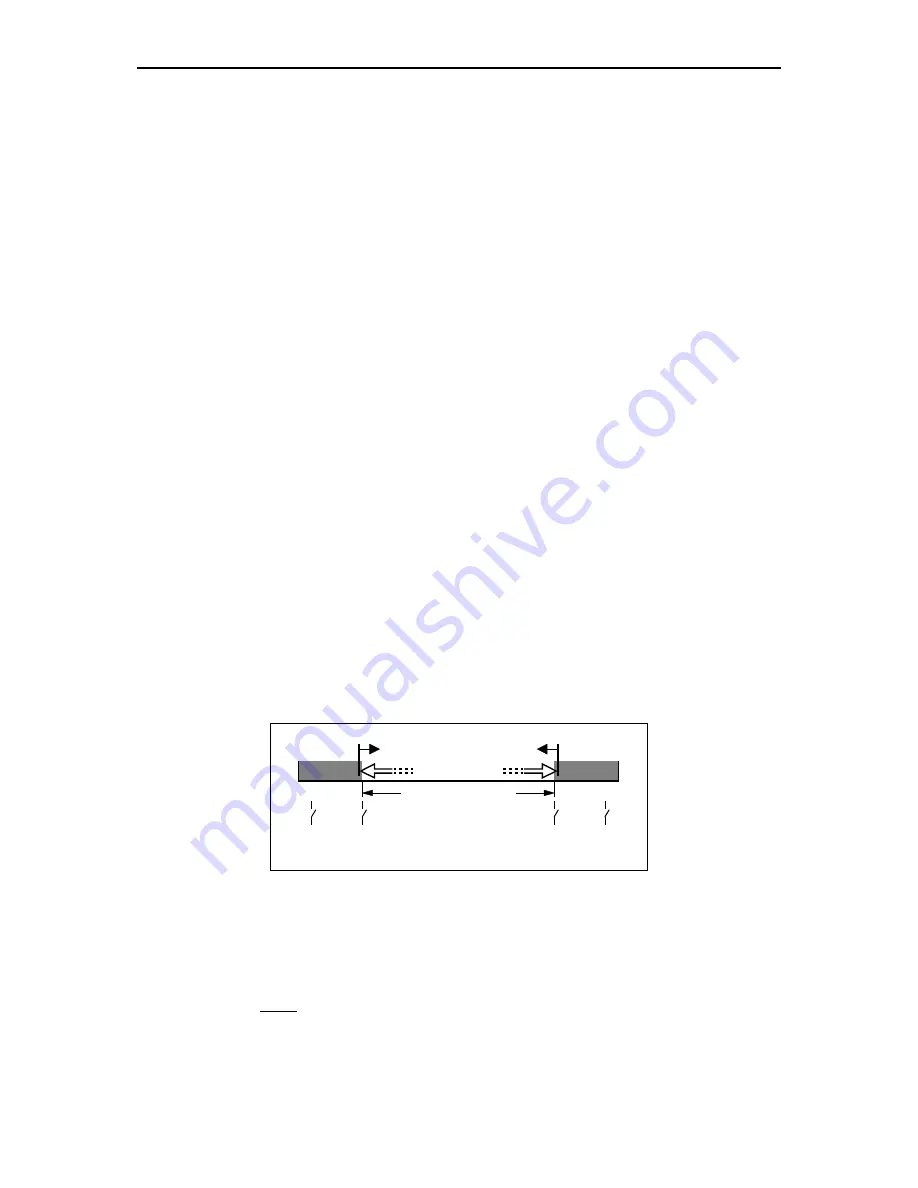
F
UNCTIONAL
D
ESCRIPTIONS
4.11 Limit switches
4-31
8310/8610-8
4.11 Limit switches
4.11.1 Software limit switches and input monitoring
The positioning range can be limited by programming two special position
values at the axis parameters:
•
Iower limit: 3/71 (»Pos. min«)
•
upper limit: 3/72 (»Pos. max«)
The »Pos. min« < »Pos. max« condition must be observed. Otherwise, this
causes a parameter error.
The programming of the limits effects the activation of the
−
input monitoring of all absolute position values within the programming
mode of nominal values and for the direct input modes,
−
−
software limit switch function if storage location 3/73 is programmed
accordingly (refer to below).
The actual position is controlled constantly during a positioning or parking
process, a manual positioning, or a reference search routine if a 1 (»driving«)
is programmed in storage location 3/73. Once the upper or lower limit is
exceeded,
−
a braking process is initiated,
−
the
/fault signal is output at terminal P
1
30 (level changes from High to Low),
−
the separation points in display B are flashing (only visible if the
corresponding axis is just displayed).
The drive can now be positioned only in the opposite direction.
max. positioning range
limit switch
software
mechan.
mechan.
software
limit switch
E2800059
The same also applies if a 2 (»
^
start«) is programmed at storage location
3/73. In addition, when specifying a
start signal the Controller first tests if the
nominal position of the new sentence would be beyond the limit values (this is
principally only possible for processing nominal lengths or if the limits have
been changed after programming of the nominal positions). In this case, the
limit switch will trigger including the effects described above.
Independent of the programming of storage location 3/73, the limit switch
function is always deactivated
Содержание GEL 8310
Страница 14: ......
Страница 122: ......
Страница 123: ...TROUBLE SHOOTING 6 8310 8610 8 i 6 Trouble shooting 6 1 6 1 Warning and error messages 6 1 6 2 Fault memory 6 12 ...
Страница 133: ......
Страница 152: ...A 18 STORAGE LOCATIONS FOR MACHINE PARAMETERS 8310 8610 8 Remarks ...
Страница 180: ......
Страница 210: ......
Страница 213: ...FORMS Appendix Y 8310 8610 8 i ...
Страница 226: ...UPDATE INFORMATION Appendix Z 8310 8610 8 i ...