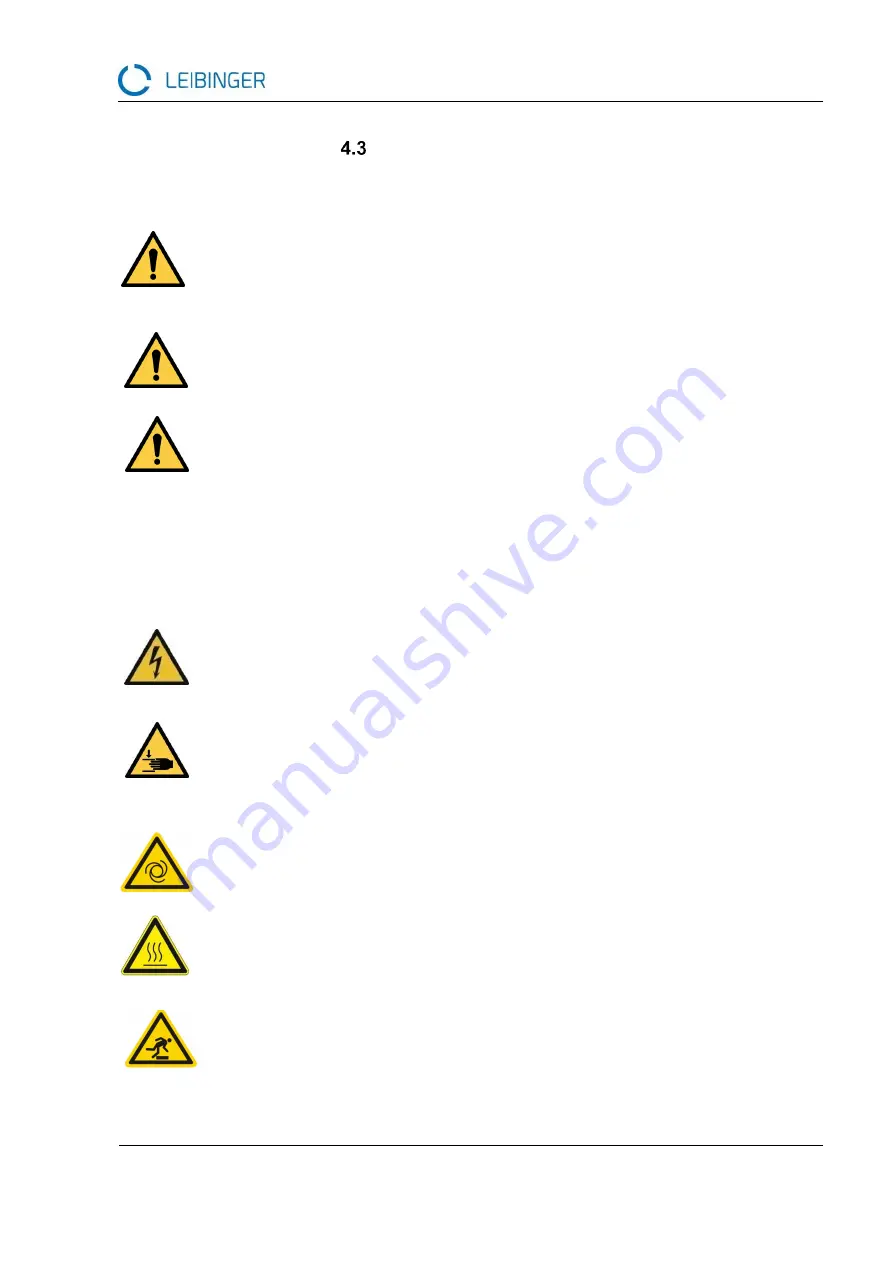
2020-02
CANVASA II + II can filling machine operating manual
11
Safety information
The safety information is designated on the basis of the severity of the danger as follows:
Danger!
Indicates an immediate hazard involving a high degree of risk that directly results in death
or extremely serious injury.
Warning!
Indicates a hazard involving a moderate degree of risk that results in death or serious injury.
Caution!
Indicates a hazard involving a low degree of risk that results in minor or moderate injury or
material damage.
Types of hazards
The following types of hazards may occur during the installation, operation, repair and disposal of
electrical devices and components:
Risk of death from electric shock
Disconnect the machine from the power supply and secure it against reconnection prior to
opening electrical devices
Risk of injury due to crushing
Ensure the proper positioning of all covers before operating the machine!
Risk of injury due to automatic start-up
The automatic sequence inside the machine begins automatically once the can has been in-
serted. Do not reach into insertion or discharge openings!
Risk of burns due to hot parts
Parts heat up and can cause burns. Wear suitable protective clothing.
Risk of tripping due to cables and hoses
The left and rear sides in particular pose an increased risk of stumbling.