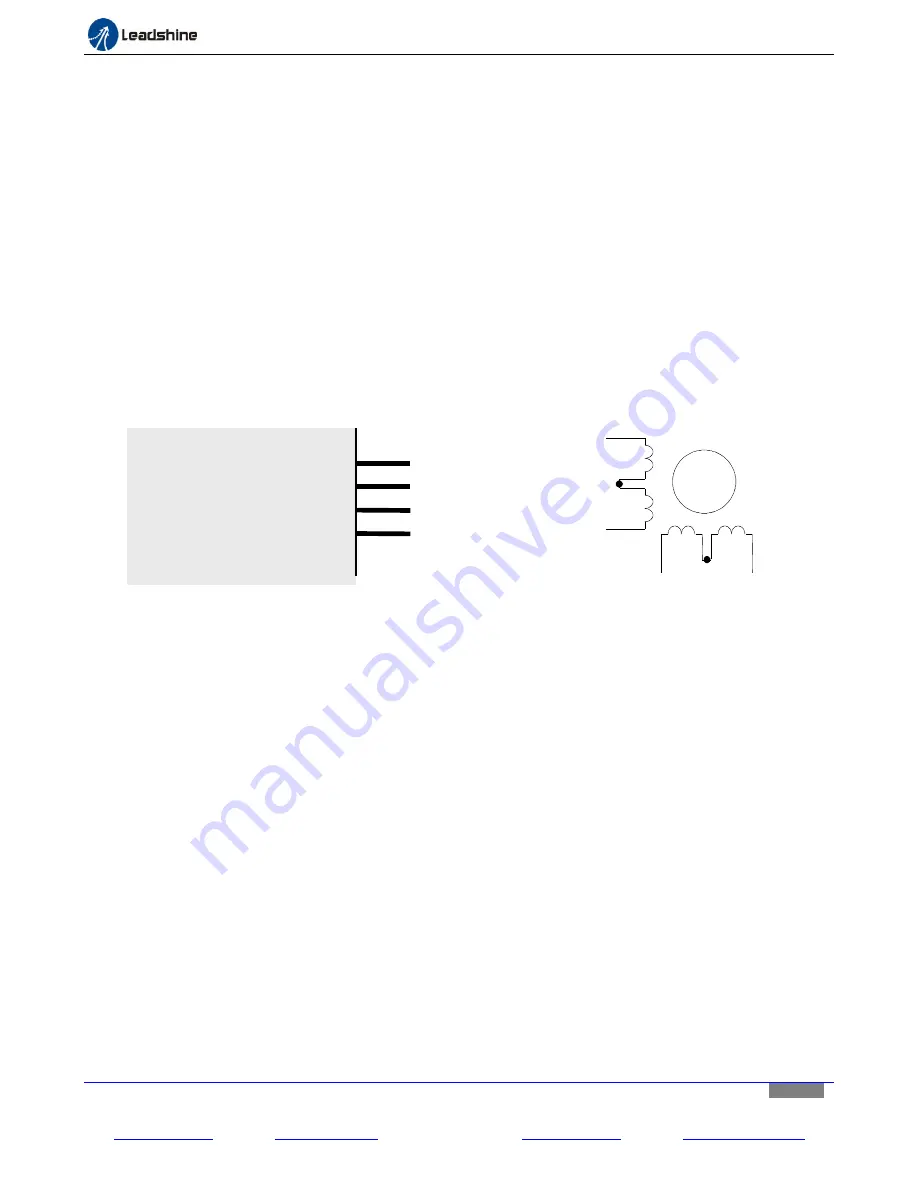
Hardware
installation manual of the multi-axis drive MX4660
Leadshine Technology Co., Ltd
Leadshine America, Inc.
Page 10/28
3/F, Block 2, Nanyou Tianan Industrial Park, Shenzhen, China
25 Mauchly, Suite 318, Irvine, CA 92618, USA
Tel: 86-755-26409254
Fax: 86-755-26402718
Tel: 1-949-608-7270
Fax: 1-949-608-7298
Web:
www.leadshine.com
Email:
Web:
www.leadshine.com
Email:
Connecting a 8-Lead Stepper Motor
The MX4660 can drive an 8-lead stepper motor in either series connection or parallel connection. Before the
connection, please read the datasheet of your stepper motor.
Connecting a 8-Lead Stepper Motor in series connection
Refer to the wiring diagram of your stepper motor datasheet. Figure 8 illustrates how to connect an 8-lead
stepper motor to the MX4660 in series connection.
An 8-lead stepper motor in series connection requires less current, so the motor coils can be charged quicker
and achieves peak output torque faster than the same motor connected in parallel connection. This makes series
connection preferable for applications that require higher torque at lower speed. But on the other side, because
of its higher inductance, 8-lead stepper motor in series connection generates more motor heating and its higher
speed torque performance is not good as a parallel connected stepper motor. It is recommended for not setting
drive current no more than 70% of its rated current to prevent too much heating for a series connected 8-lead
stepper motor, but what current to set is application dependent and at a user’s choice.
Figure 8
Connecting an 8-lead stepper motor in series connection
Connecting a 8-Lead Stepper Motor in Parallel Connection
Refer to the wiring diagram of your stepper motor datasheet. Figure 9 illustrates how to connect an 8-lead
stepper motor to the MX4660 in parallel connection.
Due to the lower inductance for an 8-lead stepper motor in parallel connection, its high speed torque drops
slower (“better high-speed torque”) than in series connection during higher speed motor rotation. This makes
parallel connection preferred for applications runs in high speeds constantly such as CNC routers. Due to the
parallel connected stepper motor will draw more current, thus it also has high requirements for the powering
stepper drive. Fortunately, the maximum 6.0A output for each of four stepper drive module will allow MX4660
to drive stepper motors up to NEMA 34 in parallel connection.
Theoretically, to get the maximum torque of a parallel connected 8-lead stepper motor, you should multiply the
phase current by 1.4. But it is suggested to set a “just enough” lower value to prevent too much heating from
your stepper motor.
A+
A-
B+
B-
MX4660
A+
A-
B+
B-
8-lead Stepper Motor
8 Leads
A+
A-
B +
B -