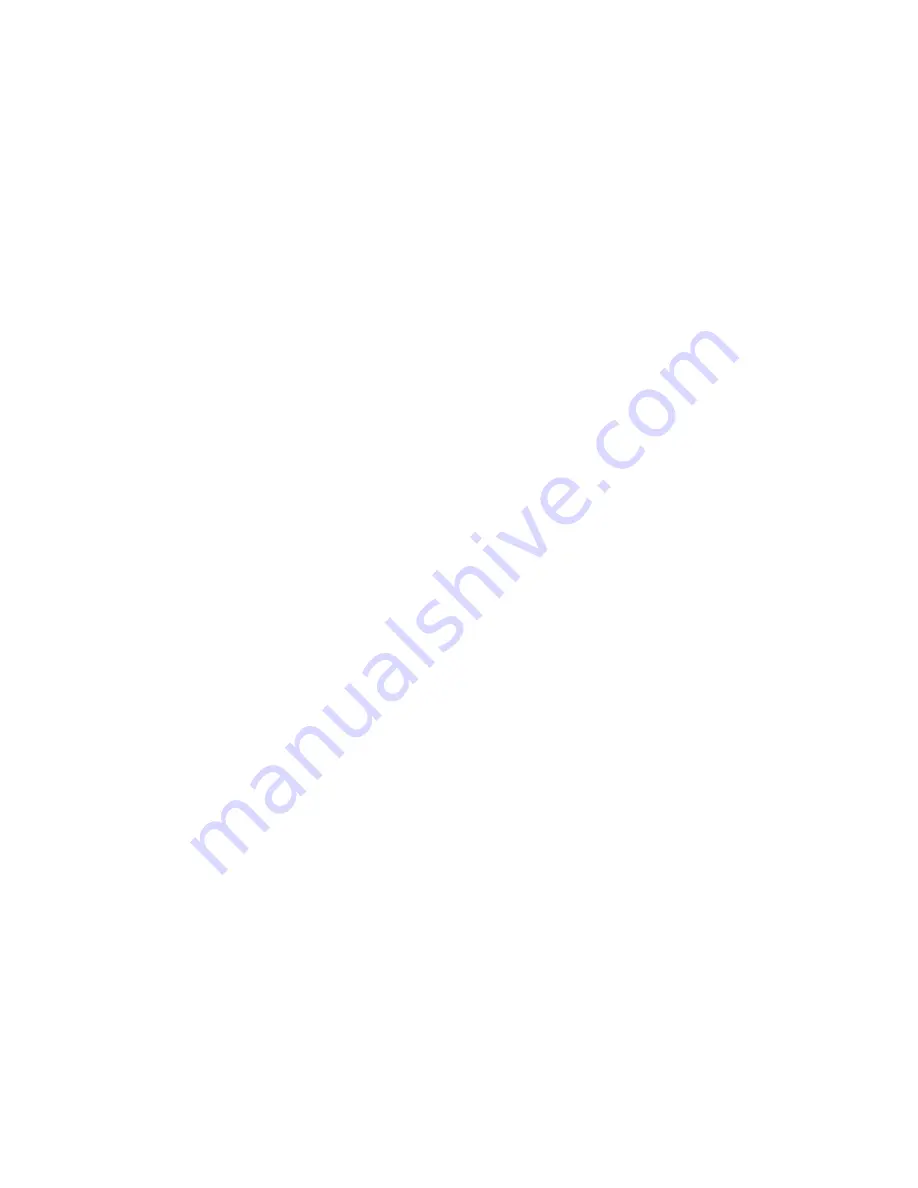
LAWSON ENGINEERS LTD Ref : PJ1682
Issue Date : 06.06.2006
Should an emergency stop occur, all PLC outputs will be de-energised and three-phase to
the power pack motors will be removed.
There are 3 No. Emergency Stop buttons located on the control system located in the
following positions.
•
Power Pack Remote I/O Panel.
•
On the winch, located on the opposite side of the winch to the control panels.
•
On the Cavotec Joy Stick Panel.
During the initial set up of the A Frame the system provides an “Mobilisation” key
switch, this facility only allows the 1
st
power pack motor to start and will remove the
emergency stop button functionality from the safety circuits, together with any other
interlocks which would normally prevent the system from operating.
7.2.3 Operation
The main operation of the R.O.V. Launch and Recovery system is described in detail in
Section 6. The following is a brief description of each control panel and its control
features.
Power Pack 415V Starter Control Panel
•
Mains 415V – 440V 60Hz Triple Pole Incoming isolator
•
2 x 75KW Star / Delta Hydraulic Power Pack Motor Starters
•
150W, 110Vac Anti-Condensation Heater and Thermostat
•
2KW 415V Oil Tank Heaters and Inline Thermostat
•
110V Transformer
•
24V 20A Power Supply
•
24V 5A Instrumentation Power Supply
Power Pack PLC Control Panel
•
150W 24Vdc Anti-Condensation Heater and Thermostat
•
Twido TWDLCAE40DRF Compact PLC Base Controller –24 Digital Inputs, 14
Relay Outputs, 2 Transistor Outputs
•
Emergency Safety Relay
•
Emergency Stop Button
•
Emergency Stop to Cavotec MC 3000 Box
- 31 -