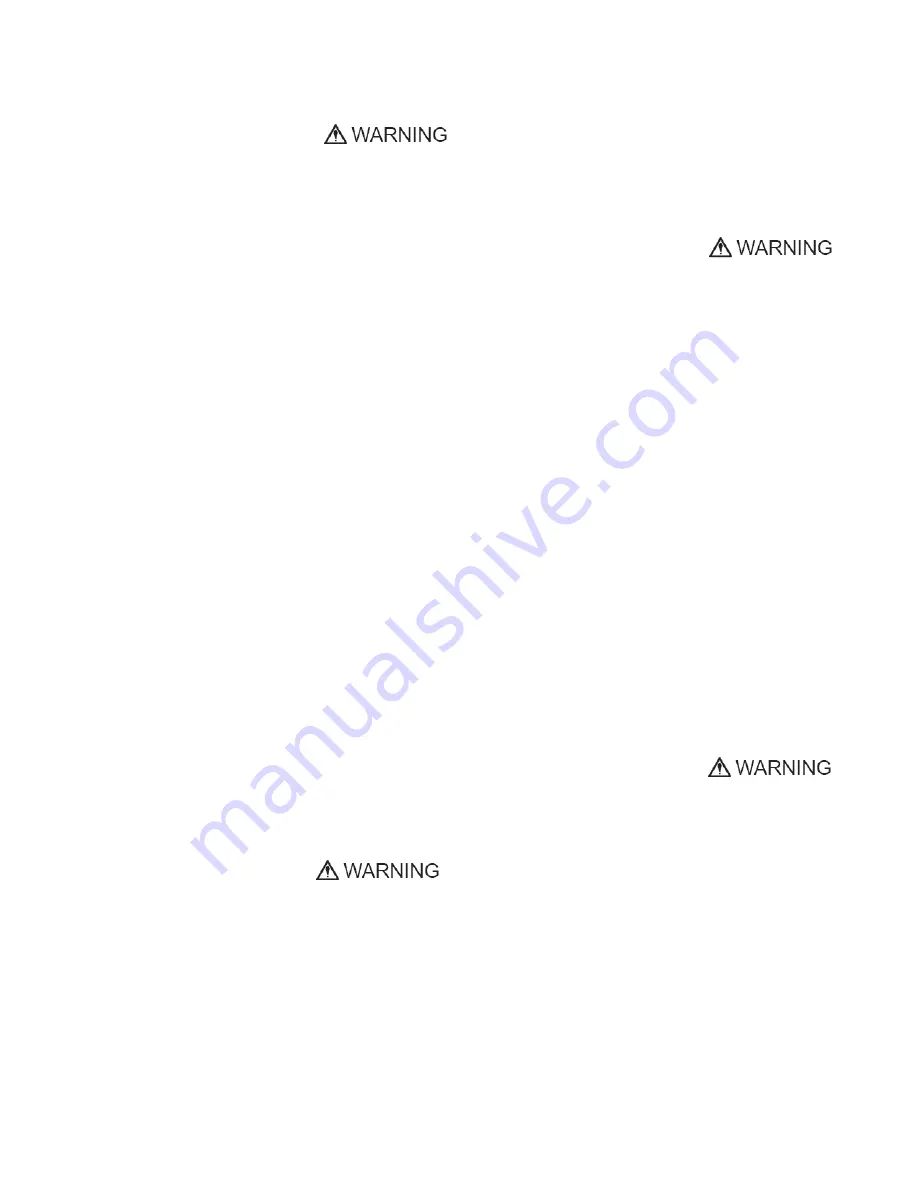
Superabrasive
User
Manual
Original
Language
Lavina®
30G
‐
S
6/2014
7
life
of
30
days,
depending
on
the
concentration
of
contaminants,
humidity,
and
temperature.
TESTING
There
are
a
great
number
of
instruments
offered
on
the
market
to
test
for
toxic
gases.
Only
those
designed
to
read
carbon
monoxide
resulting
from
combustion
engines
is
considered
acceptable
for
testing
exhaust
emissions
from
propane
powered
floor
machines.
Some
instruments
are
used
to
read
“ambient
air”
and
may
be
damaged
if
used
to
take
readings
in
the
muffler
or
tail
pipe.
Selecting
the
proper
instrument
is
an
important
part
of
meeting
the
testing
requirements.
Generally
speaking,
units
capable
of
reading
in
ppm,
(parts
per
million),
at
ranges
from
0
to
1000
are
adequate
for
checking
ambient
air
(air
in
the
breathing
zone
of
the
operator).
Instruments
capable
of
testing
carbon
monoxide
in
the
exhaust
should
be
able
to
read
from
0
to
at
least
2000
ppm
and
should
be
certified
by
the
manufacturer
for
that
purpose.
Some
instruments
and
systems
used
for
these
purposes
are:
1
) AMBIENT
AIR
MONITORING
DRAGER
Model
190:
Manufactured
by
National
Drager.
SENSIDYNE
gas
sampling
system
with
YB
‐
11038
Sensidyne
dectector
tubes
DRAGER
gas
sampling
system
with
YB
‐
4620
Drager
detective
tubes
GAS
‐
TECH
Model
CO
‐
95
ENERAC
60:
Manufactured
by
Energy
Efficiency
System
2) ENGINE
EXHUAST
ANALYZERS
HORIBA
GAS
ANALYZER
ENERAC
2000
COMBUSTION
ANALYZER
ENERAC
60
3) DATA
LOGGERS
INDUSTRIAL
SCIENTIFIC
CORP.
MODEL
STX
‐
70
CO
MONITOR,
Data
‐
Logger
BIOSYSTEMS
INC.
“TEXILOG”
Data
‐
Logger
All
instruments
used
for
testing
must
be
calibrated
at
intervals
recommended
by
the
manufacturer.
The
monitor,
model
number
and
date
of
calibration
will
be
recorded
with
all
test
results.
OPERATOR
The
operator
must
know
the
machine’s
work
environment.
Only
one
operator
at
a
time
can
work
with
the
machine.
The
operator
must
be
properly
trained
and
well
instructed
prior
operating
the
machine.
The
operator
must
understand
all
the
instructions
in
this
manual.
The
operator
must
understand
and
interpret
all
the
drawings
and
designs
in
manual.
The
operator
must
know
all
sanitation
and
safety
regulations
pertaining
to
the
operation
of
The
operator
must
have
floor
grinding
experience.
The
operator
must
know
what
to
do
in
case
of
emergency.
The
operator
must
have
an
adequate
technical
knowledge
and
preparation.
The
operator
is
expected
to
operate
their
equipment
safely
and
responsibly.
They
are
responsible
for
the
proper
handling
and
storage
of
propane
cylinders,
identifying
potential
hazards
associated
with
his
job
and
avoiding
these
hazards
at
all
times.
PROPANE
CYLINDERS
The
Propane
cylinders
are
constructed
of
either
aluminum
or
steel.
We
recommend
aluminum
because
it
is
lighter
and
guards
against
rusting.
The
cylinder
used
on
propane
powered
floor
machines
is
classified
as
a
4E240
cylinder.
Its
rated
capacity
is
20
lbs.
and
this
designation
refers
to
the
model
of
the
cylinder.
Actual
propane
capacity
achieved
during
filling
can
be
less
than,
equal
to,
or
slightly
more
than
20
lbs.
Use
only
UL,
CTC/DOT
listed
cylinders.
The
propane
cylinder
used
on
the
floor
machine
is
a
motor
fuel
cylinder
as
listed
by
the
Department
of
Transportation.
Unlike
the
common
20
‐
lb
propane
outdoor
grill
cylinders
(which
are
not
legal
for
use
on
propane
floor
machines),
the
motor
fuel
cylinder
has
a
number
of
safety
systems
designed
into
it
to
ensure
your
safety
at
all
times.
There
are
two
types
of
20
lb.
motor
fuel
cylinders.
Liquid
draw
Vapor
draw
The
liquid
draw
cylinder
is
used
on
larger
vehicles
like
forklifts.
These
machines
have
special
vaporizing
carburetors
to
allow
the
propane
to
change
from
a
liquid
to
a
gas
before
being
burned
in
the
combustion
chamber.
The
vapor
draw
cylinder
is
used
on
small
machines
like
the
propane
powered
floor
care
machines.
The
vacuum
generated
by
the
engine
draws
up
the
Propane
gas
vapor
through
the
fuel
system.
The
propane
powered
floor
care
machine
does
not
have
an
evaporating
system
and
will
freeze
up
if
liquid
propane
is
introduced
to
it.
It
is
necessary
that
special
attention
be
paid
to
ensure
that
neither
the
liquid
nor
the
vapor
draw
cylinders
be
overfilled.
REFUELLING
CYLINDERS
The
proper
filling
of
propane
cylinders
is
a
subject
so
important
that
it
warrants
special
attention.
Propane
cylinders
should
only
be
filled
by
qualified
propane
dealers.
Most
important,
propane
cylinders
should
be
filled
no
more
than
80%
of
their
rated
capacity.
The
other
20%,
which
is
about
4”
(10
cm)
from
the
top
of
the
cylinder,
is
called
the
vapor
space
or
headspace.
This
vapor
can
be
compressed
without
causing
the
pressure
relief
valve
to
open
and
vent
gas
to
the
area
around
the
cylinder.
If
there
is
no
headspace
to
allow
for
fuel
expansion,
the
pressure
relief
valve
will
open,
releasing
propane
gas
into
the
atmosphere.
This
is
a
very
dangerous
and
volatile
situation
as
there
is
always
the
possibility
that
enough
of
the
vented
gas
could
find
its
way
down
to
the
floor
and
come
in
contact
with
a
pilot
light
from
a
furnace,
hot
water
heater,
or
other
source
of
ignition.