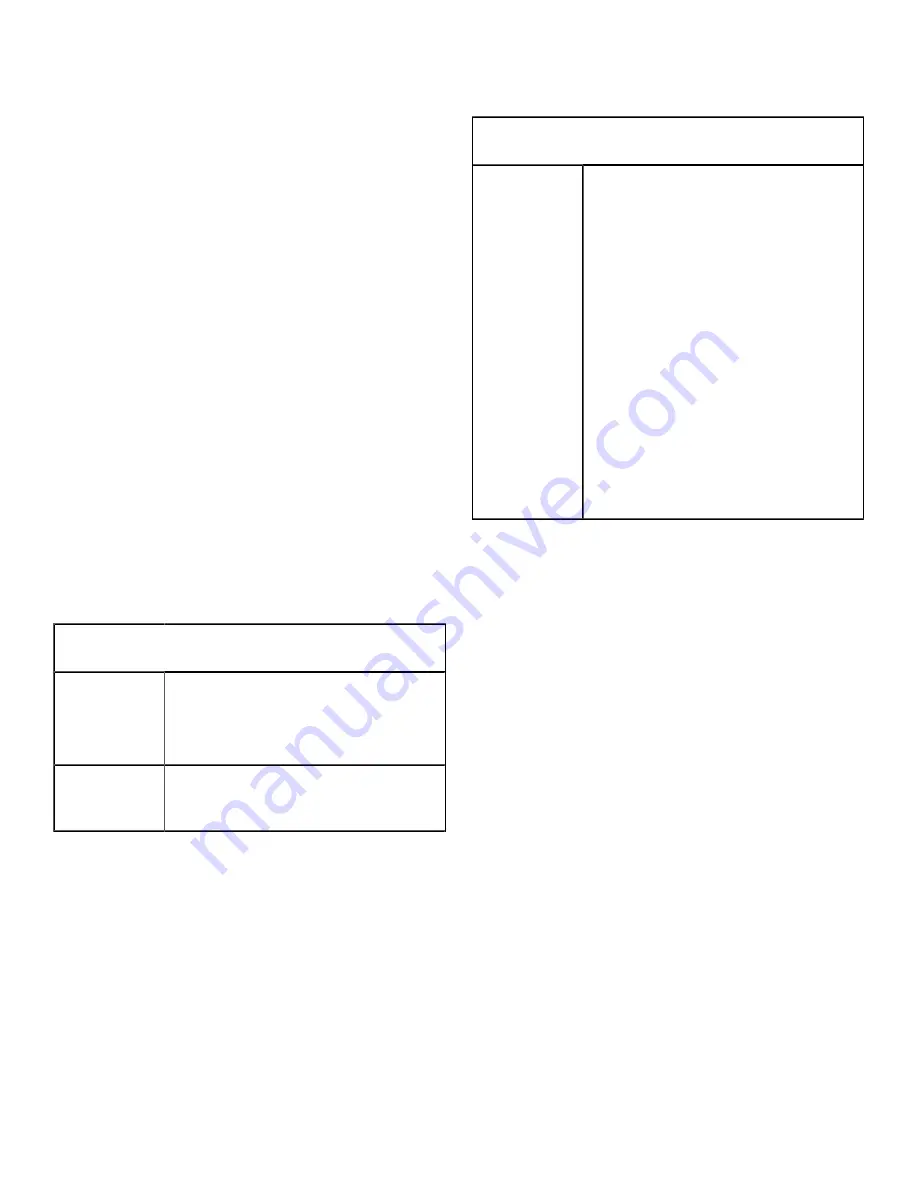
Installation
Part No. 70476501ENR7
25
Installation
Pre-Installation Inspection
Upon delivery, visually inspect the crate, carton and parts for
any visible shipping damage. If the crate, carton, or cover is
damaged or signs of possible damage are evident, have the
carrier note the condition on the shipping papers before the
shipping receipt is signed, or advise the carrier of the condition
as soon as it is discovered.
Remove the crate and protective cover as soon as possible and
check the items listed on the packing list. Advise the carrier of
any damaged or missing articles as soon as possible. A written
claim should be filed with the carrier immediately if articles are
damaged or missing.
IMPORTANT: Remove the shipping tape from the two
back draft dampers located in the exhaust outlet.
IMPORTANT: Warranty is void unless tumble
dryer is installed according to instructions in this
manual. Installation should comply with minimum
specifications and requirements detailed in this
manual and applicable local gas fitting regulations,
municipal building codes, water supply regulations,
electrical wiring regulations, and any other relevant
statutory regulations. Due to varied requirements,
applicable local codes should be thoroughly
understood and all pre-installation work arranged for
accordingly.
Materials Required (Obtain Locally)
All Models
One Single Pole fused disconnect switch
or circuit breaker on 1 Phase models.
Circuit breaker on 3 Phase models.
Gas Models
One gas shut-off valve for gas service line
to each tumble dryer.
Materials Required (Obtain Locally)
Steam Models
One steam shut-off valve for steam service
line to be connected upstream of solenoid
steam valve.
Two steam shut-off valves for each
condensate return line.
Flexible steam hoses with a
125 psig (pounds per square inch gauge)
(8.79 kg/sq. cm) working pressure for
connecting steam coils. Refer to Figure
21 120 Series Tumble Dryers and Figure
22 170 and 200 Series Tumble Dryers for
sizing and connection configurations.
Two steam traps for steam coil outlets to
condensate return line.
Optional – Two vacuum breakers for
condensate return lines.
IMPORTANT: 3 Phase Only – Each tumble dryer
must be connected to its own individual branch
circuit breaker, not fuses, to avoid the possibility of
“single phasing” and causing premature failure of the
motor(s).
Location Requirements
The tumble dryer must be installed on a level floor. Floor
covering materials such as carpeting or tile should be removed.
To assure compliance, consult local building code requirements.
The tumble dryer must not be installed or stored in area where it
will be exposed to water and/or weather.
IMPORTANT: DO NOT block the airflow at the rear
of the tumble dryer with laundry or other articles.
Doing so would prevent adequate air supply to the
combustion chamber of the tumble dryer.
A typical tumble dryer enclosure is shown in Figure 2 .
IMPORTANT: Install tumble dryers with sufficient
clearance for servicing and operation, refer to
.
Содержание LDR-900-S
Страница 2: ......