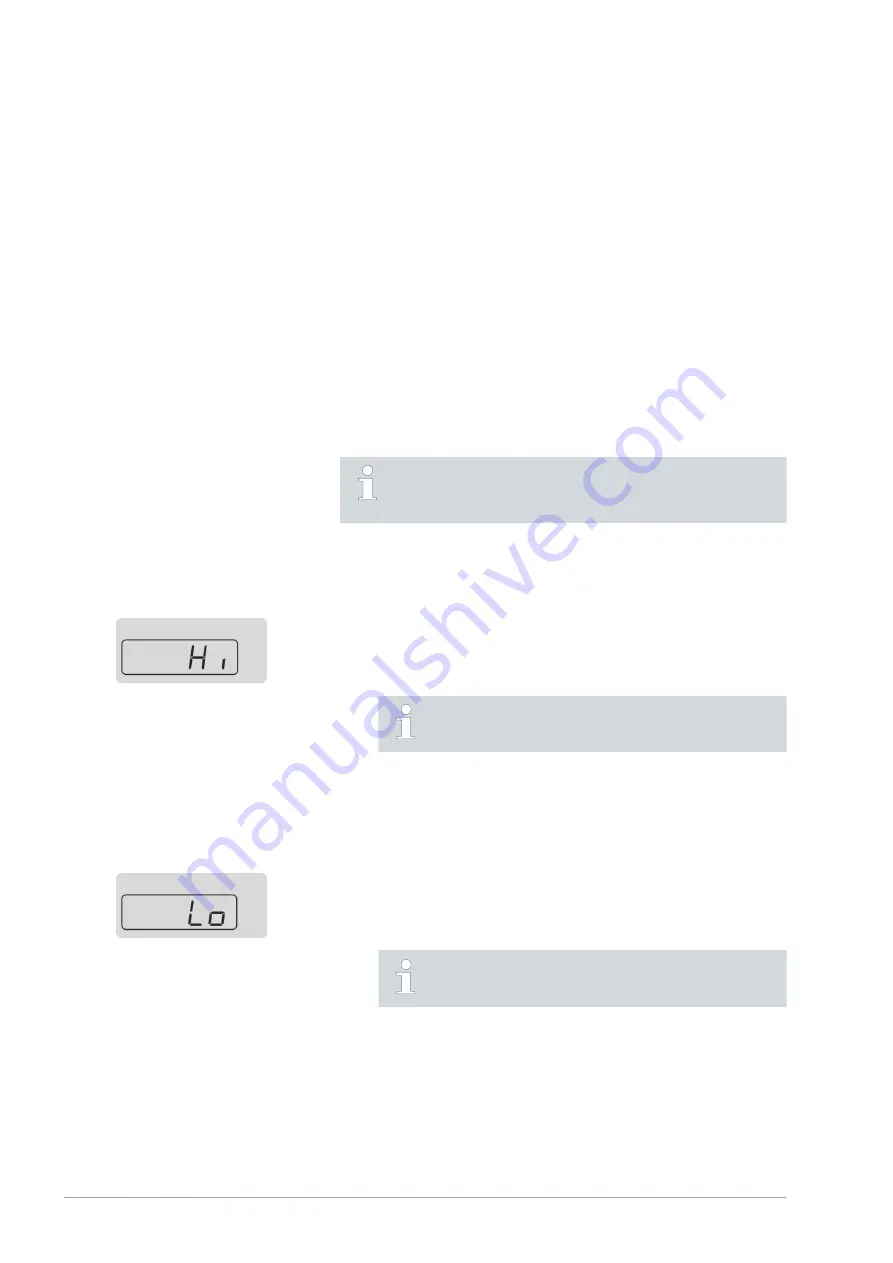
3.
Press the input button to confirm.
6.5 Restricting the temperature limits
You must limit the temperature limit value range for safety reasons. These
two values depend on the heat transfer liquid used. The default settings
45.0 °C and 5.0 °C are stored in the device and cannot be changed.
Appropriate temperature limit values are:
Aqua 90
- Set the range to the values 42 °C and 3 °C.
Kryo 30 (water/
glycol)
- Set the range to the values 42 °C and -12 °C.
Adjusting the temperature limit values automatically limits the
adjustable set point range to 2 °C below the upper temperature
limit and 2 °C above the lower temperature limit.
Personnel:
n
Operating personnel
1.
Select the menu item for the upper temperature limit value.
2.
Press the input button to confirm.
3.
Specify the upper limit.
The maximum value for the upper limit is 45 °C.
4.
Press the input button to confirm.
Personnel:
n
Operating personnel
1.
Select the menu item for the lower temperature limit value.
2.
Press the input button to confirm.
3.
Specify the lower limit.
The minimum value for the lower limit is 5 °C when using
Aqua 90 and -15 °C when using Kryo 30.
4.
Press the input button to confirm.
6.6 Configuring the clock timer
The integrated clock timer can be used to switch the device on and off
automatically. The clock timer can be viewed and configured during normal
operation of the device.
Upper temperature limit value
Fig. 14: Upper limit
Lower temperature limit value
Fig. 15: Lo. limit
V07
Microcool
34 / 57