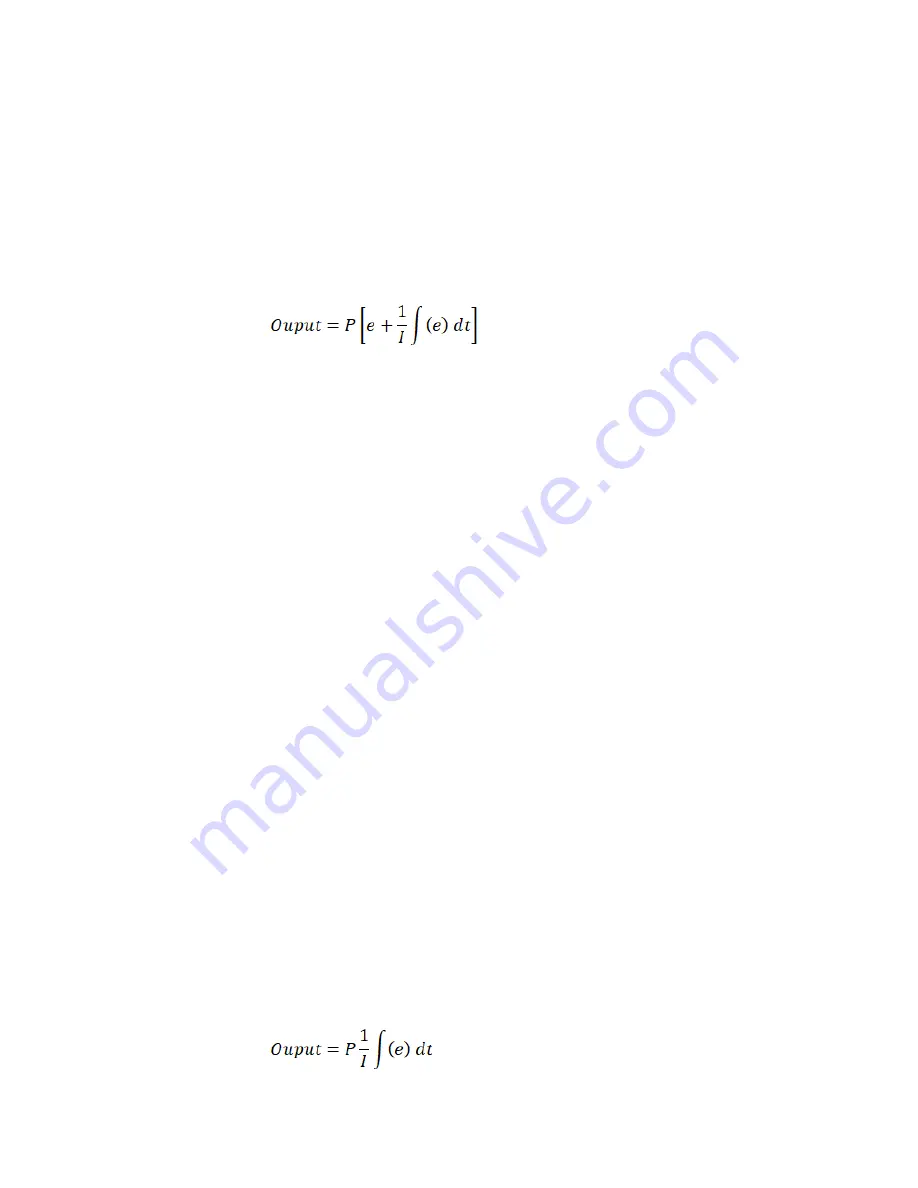
24
c
HAPTER
3:
Operation
F71/F41 Teslameter
3.5.2.3 Closed Loop Mode
Closed Loop mode, sometimes called feedback control, is the control mode most often
associated with field controllers. In this mode, the controller attempts to keep the
measured magnetic field at exactly the user entered setpoint. To do this, feedback
from the probe is used to calculate and actively adjust the field control option card
analog voltage output. The teslameter uses a PI control algorithm to tune the control-
ler for each unique system.
The PI control equation has two variable terms: proportional (P) and integral (I), see
below. See
FIGURE 3-17. Changing these variables for best control of a system is
called tuning. The PI equation is:
where the error (
e
) is defined as:
e
= Setpoint - Feedback Reading
3.5.2.3.1 Proportional (P)
The value of the proportional term is multiplied by the error (
e
) to produce the output
value. The error is defined as the difference between the setpoint and feedback field
measurement.
If proportional is acting alone, with no integral, there must always be an error or the
output will go to zero. A great deal must be known about the magnet, power supply,
and probe to compute the ideal P value. Most often the proportional setting is deter-
mined by trial and error. The proportional setting is part of the overall control loop
gain, and so are the magnet, magnet gap, and power supply characteristics. The pro-
portional setting will need to change if the hardware changes.
3.5.2.3.2 Tuning Proportional
The proportional setting is tied to the overall gain of the system. The gain of the power
supply should be fairly constant over its entire range of operation, but the gain of the
magnet changes with field. As the magnet approaches saturation, the amount of cur-
rent needed to change the field a given amount increases substantially. No single
value of P will be sufficient to maintain acceptable control over the entire range of
magnet operation.
To find the correct proportional setting for a system, turn off the I setting and start
with a low value for P, approximately 5 or 10. And set the control setpoint to some
low, non-zero field (100 mT for example). If the field is oscillating, then P is too high
and needs to be reduced. If the field is not oscillating, increase P by a factor of two
until the system begins to oscillate. See FIGURE 3-17(a). Do not set the proportional
setting so high that it causes violent oscillations. The appropriate value for P is one
half of the value required for sustained oscillation. An even lower setting of one quar-
ter may be desired for minimal overshoot. See FIGURE 3-17(b).
3.5.2.3.3 Integral
The integral term, also called reset, looks at error over time to build the integral con-
tribution to the output.