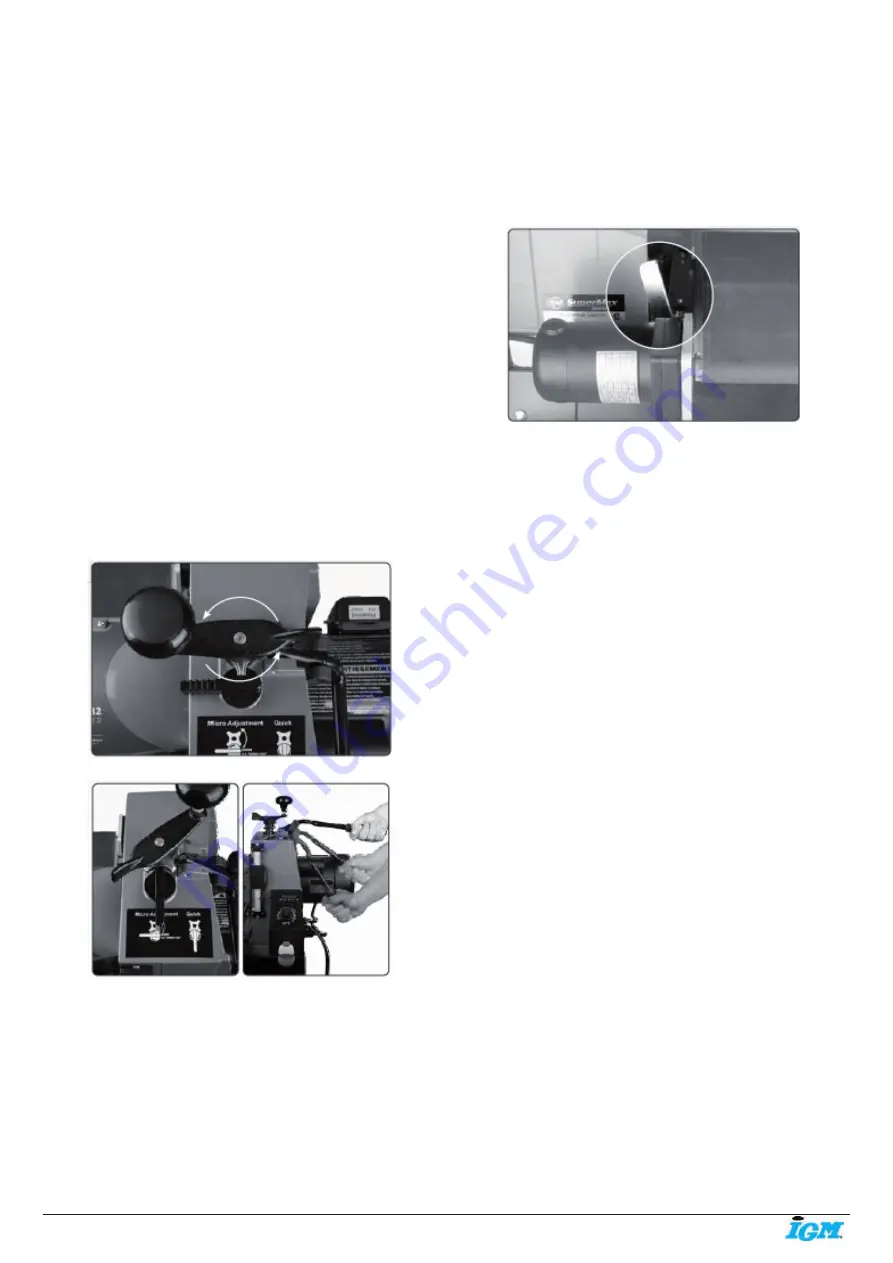
-10-
www.igmtools.com
the just sanded piece. Now the readout will show
the amount of stock removed per sanded pass in “INC” mode.
2. To change back to the original (Type 1) calibration press the “ABS/INC”
button to change back to “ABS” mode.
NOTE: When changing the abrasive wrap to a different grit the DRO must
be recalibrated for the change of drum
diameter with the new grit abrasive!
NOTE: When setting the depth of cut, never exceed the thickness of the
grit for stock removal.
Depth of Cut/Sanding
Determining the depth of cut is the most important operating procedure
decision. It may take some experimentation to determine the proper depth
of cut. We recommend practicing on a scrap of wood prior to sanding a
project.
TIP
: With the sander turned OFF, place the stock to be sanded under the
drum (wrapped with abrasive of choice)
and lower the drum until the drum contacts the workpiece and the drum
can be rotated with hand pressure.
This is a good test for maximum stock removal as you are becoming
familiar with setting the sander for proper stock removal.
Drum Head Height Adjustments
The drum height can be adjusted using one of two methods determined by
the position of the height adjustment selector.
In the micro adjustment position turning the main height adjustment
handle controls the height of the drum. Clockwise for Up and counter
clockwise for Down.
Note: One full turn raises or lowers the head approximately 1,6 mm
(1/16”).
With the selector in the quick lever position the main handle is
disengaged. Quick large-scale adjustments of up to 76,2 mm (3”) can then
be made by pulling up or down on the Quick Lever.
Note: After completing height adjustments in quick lever mode always
return the selector back to micro adjustment mode.
Conveyor and Speed Rate
After the depth of cut has been determined, selecting the proper feed rate
is essential. For finish sanding the best finish is usually achieved with a
slow to moderate feed rate. Faster feed rates can be used as long as the
machine is not over-stressed.
When finish sanding with grits finer than 80, the best finish can usually be
obtained if INTELLISAND does not engage. If INTELLISAND does slow
the conveyor when finish sanding, it is best to make another sanding pass
without changing the thickness setting and sand again
Note:
INTELLISAND will automatically adjust the conveyor feed rate if
an excess load is detected. This prevents excessive gouging, reduces
the risk of burning and protects the machine from overload or stalling.
The red light by the adjustment knob will come on when INTELLISAND is
operating. When the load is decreased, INTELLISAND will automatically
increase the feed rate to the pre-selected speed.
Stock Feeding Operation
Rest and hold the stock to be sanded on the conveyor table. Allow the
conveyor to carry the stock into the drum. Once the stock is halfway
through, reposition yourself to the outfeed side of the machine to control
the stock as it exits the unit.
Stock Feeding Maximum Performance
The versatility of this drum sander allows it to be used for a wide range of
tasks. Learning to use the multiple controls to make adjustments will allow
you to fine tune the machine for maximum results.
• Sanding stock wider than the drum
When sanding stock wider than the drum the fast lever will be very useful
(see picture). Wide stock requires extra space between the drum and the
conveyor on the outboard (left) edge. The extra space prevents ridge lines
from developing along the part that extends beyond the drum. Adjust the
fast lever 45 degrees from the vertical position to slightly shift the drum
position. Before sanding always test on a scrap piece. If a line or ridge is
still visible, make adjustments to the drum alignment. Always return the
lever to the upright position when wide stock sanding is completed.
Note: The fast lever raises the inboard side of the table .003. Upon first
use, the conveyor table bolts may be set too tight at the factory for secure
shipping. In this case, loosen the bolts slightly. Never tighten the table
bolts all the way. Tighten the bolts enough to still allow the fast lever to be
moved.
• Sanding multiple pieces simultaneously
When sanding multiple pieces at once, make sure to stagger the pieces
across the width of the conveyor belt. This position provides better contact
with the tension rollers. It is best to only process pieces that are all of a
similar thickness. If there is a thickness difference, the thinner pieces may
not come in contact with the tension rollers and may slip on the conveyor
belt.
• Sanding Imperfect or Tall Stock
To avoid bodily injury, take special care when sanding stock that is
twisted, bowed or otherwise varied in thickness from end to end. If
possible, support such stock as it is being sanded to keep it from slipping
or tipping. Use extra roller stand, assistance from another person, or
hand pressure on the stock to minimize potentially hazardous situations.
Special attention is needed as the stock exits the machine. Special
attention is needed as the stock exits the machine.
• Stock Feeding Position and Angle
Positioning the stock at an angle will allow the most effective stock
removal and least loading on the abrasives. Feeding stock straight
through yields the widest sanding capacity and least noticeable scratch
pattern. Some pieces because of their dimensions will need to be fed into
the sander at a 90-degree angle (perpendicular to the drum). However,
even a slight offset angle of the stock can provide for more effective
sanding. Final pass sanding should be done while following the grain
pattern.
Tension Roller Pressure
The tension roller pressure is factory set and should be adequate.
However, the pressure of each roller can be adjusted as needed. To
increase the tension, turn the tension adjusting screw clockwise 1/4
revolution at a time. To decrease tension, turn the adjusting screw counter
clockwise 1/4 revolution at a time.
Note: Too little pressure can result in slippage of stock on conveyor belt or
kick-back Too much tension can cause snipe when drum sanding.
Содержание 1632
Страница 14: ...14 www igmtools com 16 32 HEAD ASSEMBLY...