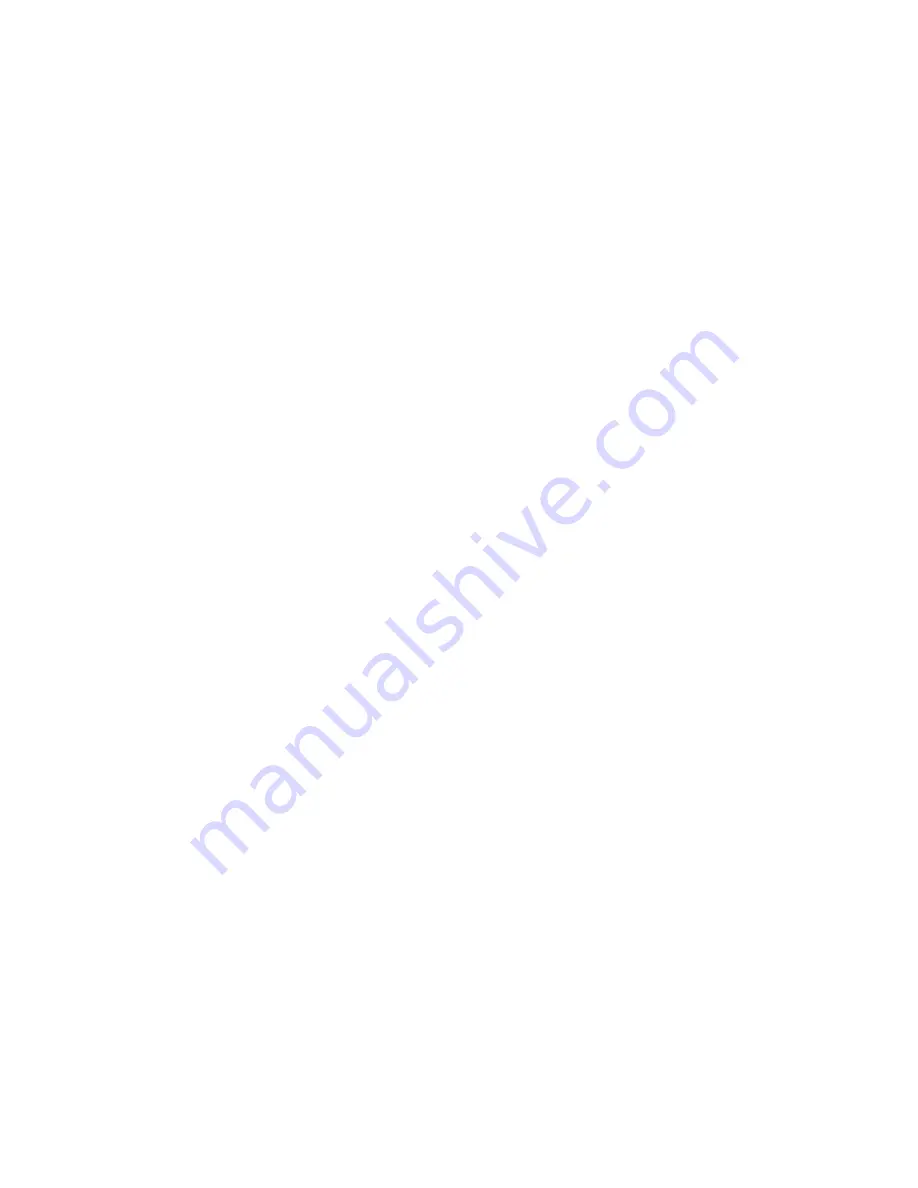
40
1.
Hold
the
dancer
arm
in
the
retracted
position.
2.
Make
sure
that
the
strap
is
correctly
wound.
See
figure
13
3.
Use
a
5/32
inch
hex
head
wrench
to
loosen
the
strap
collar
set
screw.
4.
Adjust
the
position
of
the
collar
so
that
the
strap
is
snug
when
the
dancer
arm
is
completely
retracted.
Tighten
the
screw.
5.
Use
a
1/8
inch
hex
head
wrench
to
loosen
the
set
screw
that
holds
the
spring
retainer
onto
the
dancer
arm
shaft.
6.
Position
the
spring
retainer
so
that
the
strap
is
held
snug
on
the
dancer
arm
shaft,
but
the
tension
releases
when
the
dancer
arm
is
pulled
by
the
advancing
label
stock.
If
the
tension
is
too
loose,
the
unwind
will
not
brake
properly
and
a
loop
of
loose
label
stock
will
form.
If
the.
Tension
is
too
tight,
the
printer's
stepper
motor
will
be
forced
to
pull
against
the
unwind
brake;
this
will
put
undue
stress
on
the
printer's
stepper
motor
and
may
cause
web
stalls,
or
registration
errors.
7.
Check
the
adjustment
of
the
unwind
brake
at
the
beginning
and
at
the
end
of
a
roll
of
labels,
and
adjust
if
necessary.
Содержание Write-up 3138NV-DAT
Страница 1: ...08 Write up 3138NV DAT Manual with Write Up P N 7408815 150 ...
Страница 16: ...16 Figure 6 Product Detector 1 Side Application ...
Страница 43: ...43 Figure 14 Tamp Flow Control ...