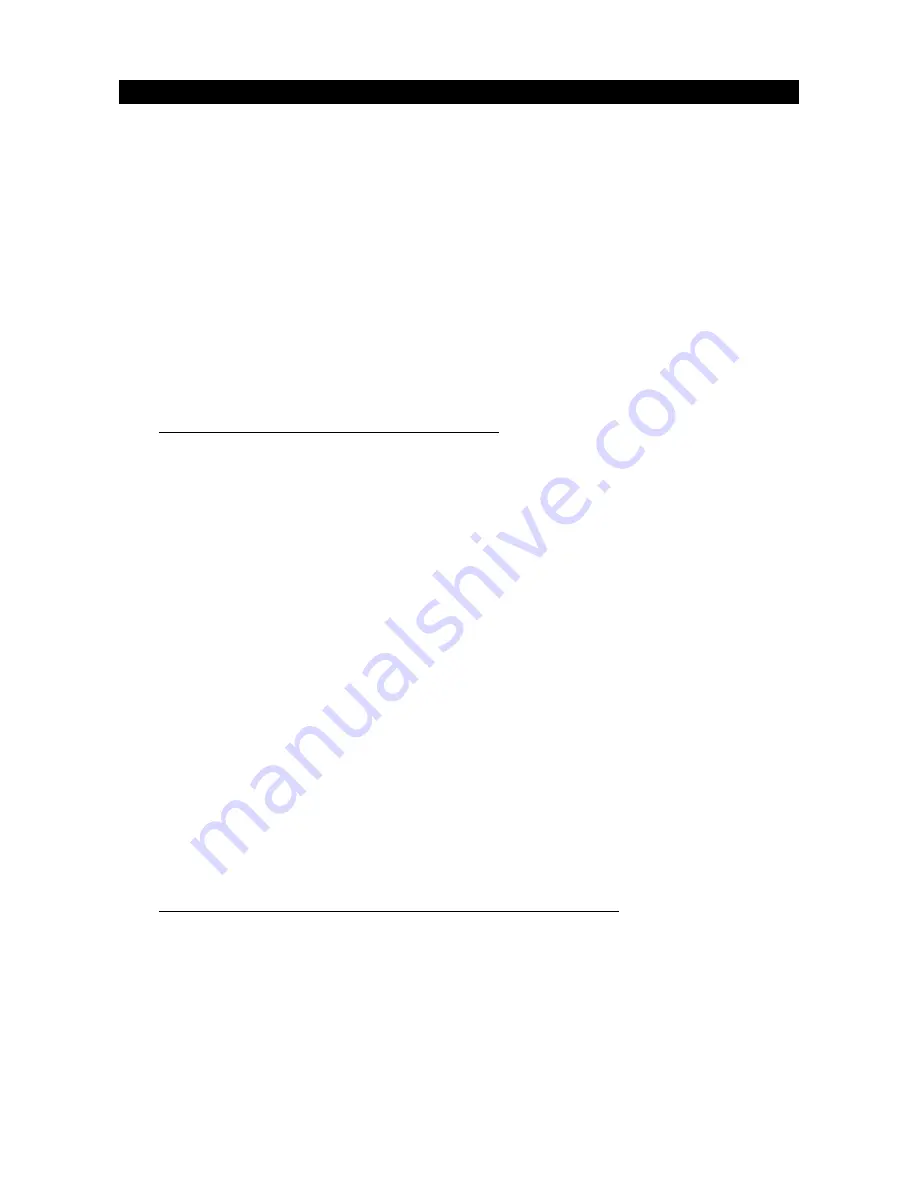
43
GENERAL CONDITIONS OF WARRANTY
KUHN-AUDUREAU S.A., B.P. 19, 85260 LA COPECHAGNIERE, FRANCE (hereinafter referred to as
the Company) hereby certifies in accordance with the provisions stated below to each original purchaser
of new equipment manufactured by Kuhn-Audureau that said equipment is, at the time of delivery to
the user, guaranteed against all construction faults and manufacturing defects, provided that the
equipment in question is used and maintained in accordance with the instructions contained in the
accompanying manual.
This warranty covers our equipment for a period of one year from the date of delivery or for 500 hours
of operation, whichever is the shorter.
The date of the invoice to the final purchaser and the return of the warranty card by the dealer to the
Company, with the signature of the dealer and the purchaser, will indicate delivery of the equipment.
The warranty is limited to a money-back guarantee or to the repair at our factory and by our Enginee-
ring Departments of parts which are recognised to be faulty in terms of material or craftsmanship.
F
The following exceptions shall apply however:
- Parts included in the composition of machines but which are not manufactured by Kuhn-Audureau, such as
tyres, transmission assemblies, overload clutches, hydraulic rams, hydraulic distributors, etc., are not covered
by the Kuhn-Audureau warranty but by the respective manufacturer’s warranty.
- Claims relating to such parts will be handled in the same way as if they were Kuhn-Audureau parts. However
compensation will depend on the warranty agreement of the manufacturer concerned, insofar as the latter
acknowledges the validity of the claim. Obviously the warranty does not apply if the faults are due to normal wear
and tear, deterioration or accidents resulting from negligence or inadequate supervision, misuse, lack of
maintenance and/or if the machine has been damaged in an accident, lent or used for a purpose other than the
one intended by the Company.
- Obviously the warranty does not apply if the faults are due to normal wear and tear, deterioration resulting from
negligence or inadequate supervision, misuse, lack of maintenance and/or if repairs have not been carried out by
an approved dealer.
- The warranty is void if alterations have been made to the machine without the express agreement of the Company
or if anything other than OEM parts have been fitted to machine sold by the Company and/or if repairs have not
been carried out by an approved dealer or distributor.
- The Company cannot be held responsible for damage suffered by the machine or its accessories during transport
and handling by any carrier, even outside the legal warranty period. Machines, machine parts or accessories are
carried at the risk of the addressee.
- The Company will not be responsible in the case of a claim or injury involving the owner or a third party, or for the
resulting liability.
-
Similarly, the Company cannot be held to pay any compensation whatsoever for the loss of a harvest or any
damages whatsoever due to a flaw, latent defect or breakdown of the machine.
F
The User is responsible for and shall bear all costs relating to:
- routine servicing of the equipment, including lubrication, supervision and maintenance of oil levels, minor
adjustments, etc.;
- the labour required to remove and replace a faulty part or parts and, if necessary, adjustments of the corresponding
new part or parts;
- the dealer’s call-out charge;
- the transport of machines, machine parts or accessories to the place of repair and the return of the elements in
question to the place of use;
- wear parts, such as belts, tyres, bed chains, knives, teeth, overload clutches, etc., which are not covered by the
warranty.
Содержание ALTOR 11050
Страница 13: ...13 ...
Страница 15: ...15 ...
Страница 17: ...17 ...
Страница 21: ...21 NOTES ...
Страница 23: ...23 Figure 1 Figure 2 Figure 3 6 HEIGHT ADJUSTEMENTS 2 POSITIONS 3 HEIGHTS 180 ROTATION ...
Страница 39: ...39 ...
Страница 42: ...42 NOTES ...