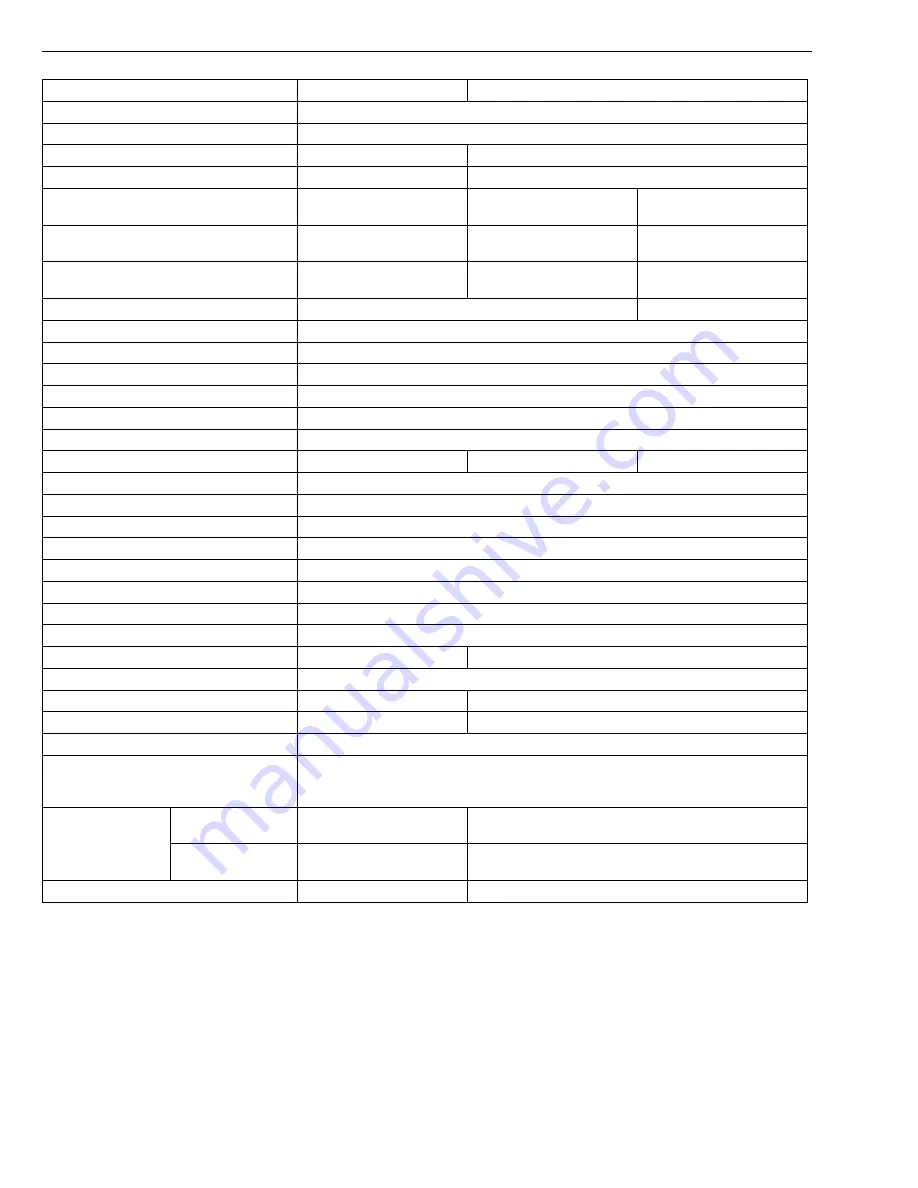
6
SM-E2B SERIES, WSM
SPECIFICATIONS
* The specification described above is of the standard engine of each model.
* Conversion Formula : HP = 0.746 kW, PS = 0.7355 kW
W10321290
Model
D782-E2B
D902-E2B
Number of Cylinders
3
Type
Vertical, Water-cooled, 4 cycle IDI diesel engine
Bore
×
Stroke mm (in.)
67
×
73.6 (2.64
×
2.90)
72
×
73.6 (2.83
×
2.90)
Total Displacement cm
3
(cu.in.)
778 (47.48)
898 (54.80)
ISO Net Continuous
kW/min
-1
(rpm) (HP/min
-1
(rpm))
11.7 / 3200 (15.7 / 3200)
13.4 / 3200 (18.0 / 3200)
15.2 / 3600 (20.4 / 3600)
ISO / SAE Net Intermittent
kW/min
-1
(rpm) (HP/min
-1
(rpm))
13.5 / 3200 (18.1 / 3200)
15.4 / 3200 (20.6 / 3200)
17.5 / 3600 (23.5 / 3600)
SAE Gross Intermittent
kW/min
-1
(rpm) (HP/min
-1
(rpm))
14.1 / 3200 (18.9 / 3200)
16.1 / 3200 (21.6 / 3200)
18.5 / 3600 (24.8 / 3600)
Maximum Bare Speed (min
-1
(rpm))
3450
3800
Minimum Bare Idling Speed (min
-1
(rpm))
900 to 1000
Combustion Chamber
Spherical type (E-TVCS)
Fuel Injection Pump
Bosch MD type mini pump
Governor
All speed mechanical governor
Direction of Rotation
Counter-clockwise (viewed from flywheel side)
Injection Nozzle
Bosch “Throttle” type
Injection Timing
0.30 rad (17
°
) before T.D.C.
0.31 rad (18
°
) before T.D.C.
0.35 rad (20
°
) before T.D.C.
Firing Order
1-2-3
Injection Pressure
13.73 MPa (140 kgf/cm
2
, 1991 psi)
Compression Ratio
24 : 1
Lubricating System
Forced lubrication by trochoid pump
Oil Pressure Indicating
Electrical type switch
Lubricating Filter
Full flow paper filter (Cartridge type)
Cooling System
Pressurized radiator, forced circulation with water pump (not included in the basic engine)
Starting System
Electric Starting with Starter
Starting Motor
12 V, 1.0 kW
12 V, 1.2 kW
Starting Support Device
By glow plug in combustion chamber
Battery
12 V, 36 AH equivalent
12 V, 52 AH equivalent
Charging Alternator
12 V, 150 W
12 V, 480 W
Fuel
Diesel Fuel No.2-D (ASTM D975)
Lubricating Oil
Class CF lubricating oil as per API classification is recommended.
If this class of lubricating oil is not available, preferably use Class CD or CE lubricating oil.
For details on recommended lubricating oils, see page G-5, 8.
Lubricating Oil
Capacity
Oil Pan Depth
101 mm (3.98 in.)
–
3.7 L (0.98 U.S.gals)
Oil Pan Depth
121 mm (4.76 in.)
3.6 L (0.95 U.S.gals)
–
Weight (Dry) kg (lbs)
63.5 (139.7)
72.0 (158.7)
KiSC issued 06, 2006 A
Содержание D662-E2B
Страница 1: ...SM E2B SERIES WORKSHOP MANUAL DIESEL ENGINE KiSC issued 06 2006 A...
Страница 17: ...15 SM E2B SERIES WSM DIMENSIONS DIMENSIONS Z482 E2B KiSC issued 06 2006 A...
Страница 18: ...16 SM E2B SERIES WSM DIMENSIONS Z602 E2B KiSC issued 06 2006 A...
Страница 19: ...17 SM E2B SERIES WSM DIMENSIONS D662 E2B D722 E2B KiSC issued 06 2006 A...
Страница 20: ...18 SM E2B SERIES WSM DIMENSIONS D782 E2B KiSC issued 06 2006 A...
Страница 21: ...19 SM E2B SERIES WSM DIMENSIONS D902 E2B KiSC issued 06 2006 A...
Страница 97: ...SM E2B SERIES WSM DIESEL ENGINE S 32b rev 001 5 01 07 THIS PAGE INTENTIONALLY LEFT BLANK...