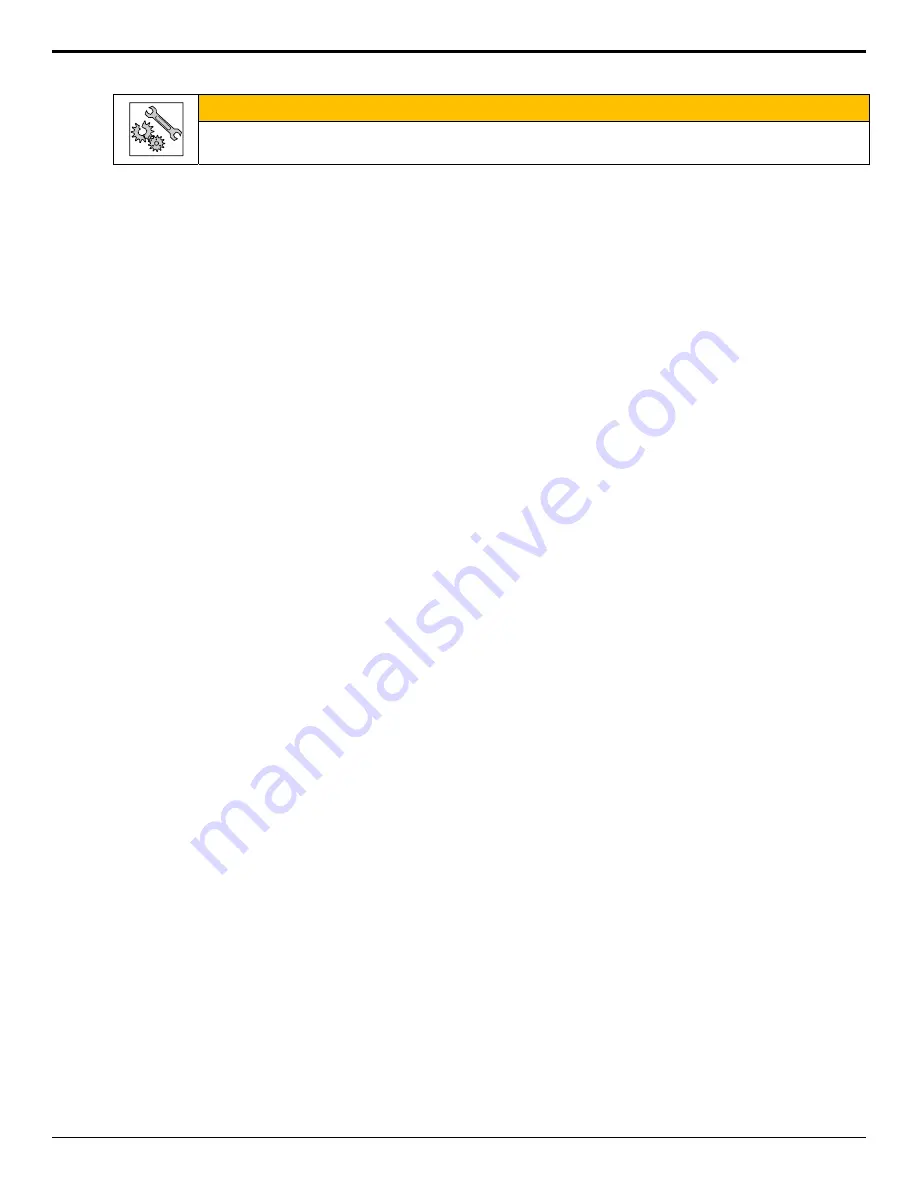
MDX [en-US]
50
11.2
Spare Parts Stock
CAUTION
After installation of spare parts it is important that the steps outlined in Section 6.1 "Commissioning / Return to
Service" are followed prior to start-up.
Due to the erosive action of the slurry, many of the wet end components of the pump may require replacement during normal
maintenance. Inspection or overhaul of the mechanical components may also require the replacement of certain parts.
The following are recommended lists of parts (whenever applicable) to have on hand for normal maintenance and inspection.
The quantities of parts kept in store will depend upon the severity of the slurry duty and the number of units operating.
Maintenance practices may also favor keeping fully built sub-assemblies or complete pumps on hand in some cases. Previous
experience in similar duties often provides the best experience. If in doubt, contact your GIW / KSB representative for specific
recommendations.
Commissioning Spares
Gaskets for all equipment
Wet End fasteners
Shaft Sleeve w/ gaskets & o-rings
Impeller Release Ring assembly
Impeller Release Ring hardware
Mechanical Seal w/ adapter & fasteners
Operational Spares include Commissioning Spares and
Additional set of gaskets for all equipment
Pump Casing
Impeller
Side Liners
Bearing Assembly
Bearings
Bearing Assembly Gasket Kit
Bearing Lubricant
Shaft Seal
Shaft Sleeve
Shaft Seal Water Ring
Stuffing Box Packing
Additional mechanical Seal
Seal Plate or Optional Throttle Seal
Содержание GIW MDX
Страница 53: ...MDX en US 53 14 Notes...