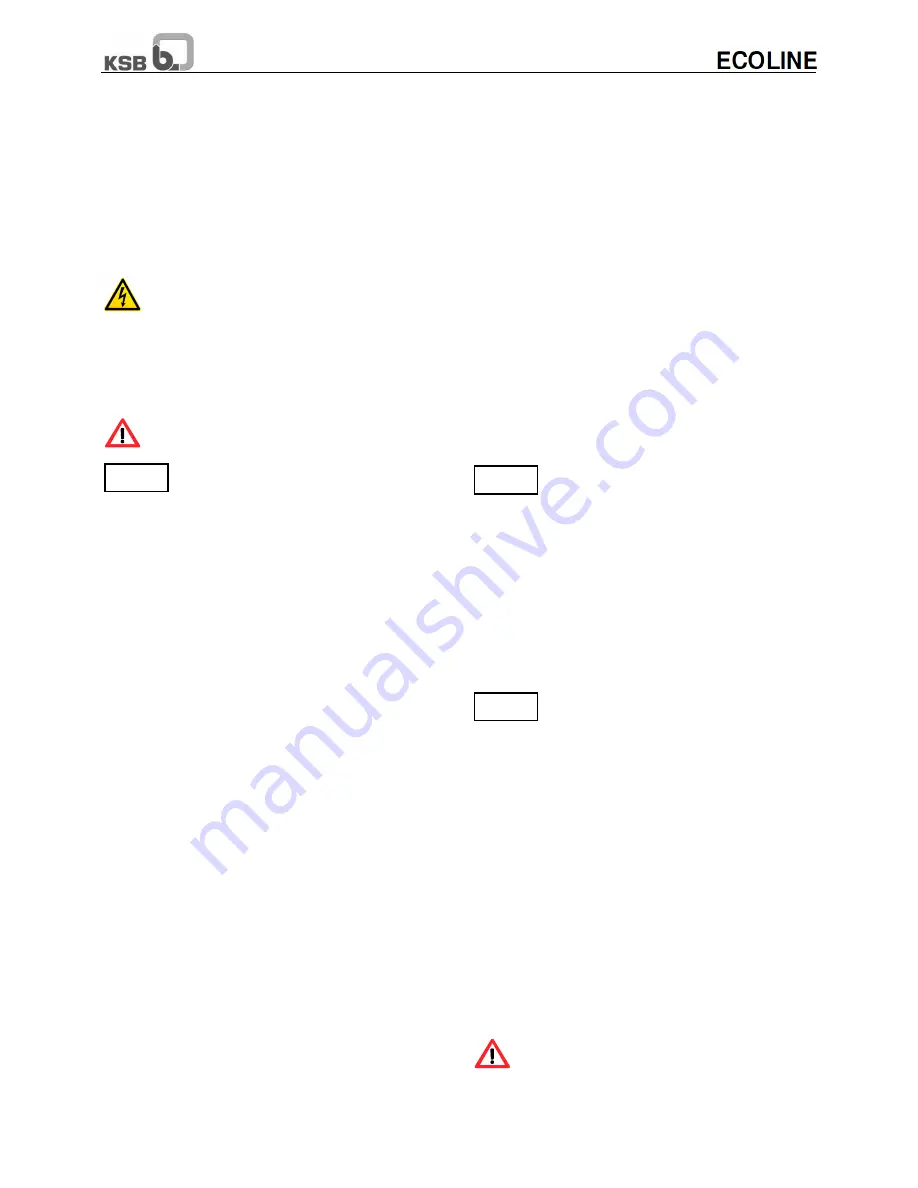
Depending on the installation position, any liquid remaining
in the valve may have to be removed.
Prior to possible transport, the valves must be flushed and
drained carefully.
If you have any questions, please contact your KSB Sales
Office.
8.1.2 Removing Actuators
If actuators powered by an external source of
energy (electric, pneumatic, hydraulic) need to be
removed from the valves or dismantled, the energy supply
must be shut down prior to starting any repair work and the
instructions in the sections 3, 8.1.1 and the operating
instructions of the actuator must be observed.
Valve actuators with integrated spring-loading
feature cannot be removed.
Springs under tension!
If you have any questions, please contact your KSB Sales
Office.
8.2
Maintenance
Our valves are largely maintenance free, materials of sliding
parts were selected to keep wear to a minimum. To ensure
reliable operation and to reduce repair costs, all valves -
especially those which are seldom operated or where access
is difficult -should be checked periodically.
The user is responsible for defining appropriate intervals for
checks and maintenance, depending on the application of
the valve.
The service life of non-maintenance-free valves can be
extended by:
- lubricating movable parts such as stem (200) and gland
bolts (not for oxygen valves) and provided in the case of gate
valve using suitable lubricants to DIN 51825 / equivalent
- timely changing of the packing rings
- timely replacing of the cover gasket (411)
The safety instructions in sections 3, 8.1 and the notes in
section 9 must be observed.
8.3
Valve Reassembly
Valve reassembly shall be effected in reverse order to
dismantling.
To maintain functional reliability, new gaskets and gland
packing shall be used whenever the valve is reassembled.
After reassembly and prior to commissioning / start-up, the
valves shall be subjected to a leak test in accordance with
DIN 3230, Part 3l, or API 598 and ASME B16.34 Section 8.
9
Troubleshooting
9.1
General
All repair and service work must be carried out by qualified
personnel using suitable tools and genuine spare parts.
The safety instructions in sections 3 and 8 must be observed.
9.2
Faults & Remedies
Fault - Leakage at the seat
Remedy - Remachine the seat on wedge/disc
and body using suitable regrinding equipment
after dismantling the valve. Regrinding
of body and cone seats should be continued until the seats
show a smooth and even ring.
Fault - Leakage at the cover/bonnet gasket
Remedy - Retighten the cover/bonnet flange connection
Remedy - Replace the gasket (411) after removing the
cover/bonnet bolts (901). Clean the surfaces carefully before
inserting a new gasket.
On asbestos-free gaskets, no additional
sealing agents may be used. When using anti
adhesive coatings, use sealing agents explicitly
recommended by the manufacturer of the sealing material.
If you have any further questions please contact nearest
KSB Sales office.
Fault - Leakage of the Stuffing Box
Remedy - Retighten the stuffing box with the nuts (920) at
the gland flange (452). Make sure that the friction forces at
the stem do not increase too much.
Remedy - Replace the packing rings of the stuffing box;
Unscrew the nuts (920) and lift the gland flange (452). Clean
the stuffing box chamber thoroughly before inserting new
packing rings. Split packing rings should be inserted in such
a way that the slots are offset by 120° to 180°.
Do not replace packing while the valve is
pressurized. The back seat bushing is not intended
to maintain a seal during replacement.
Caution
Caution
Caution