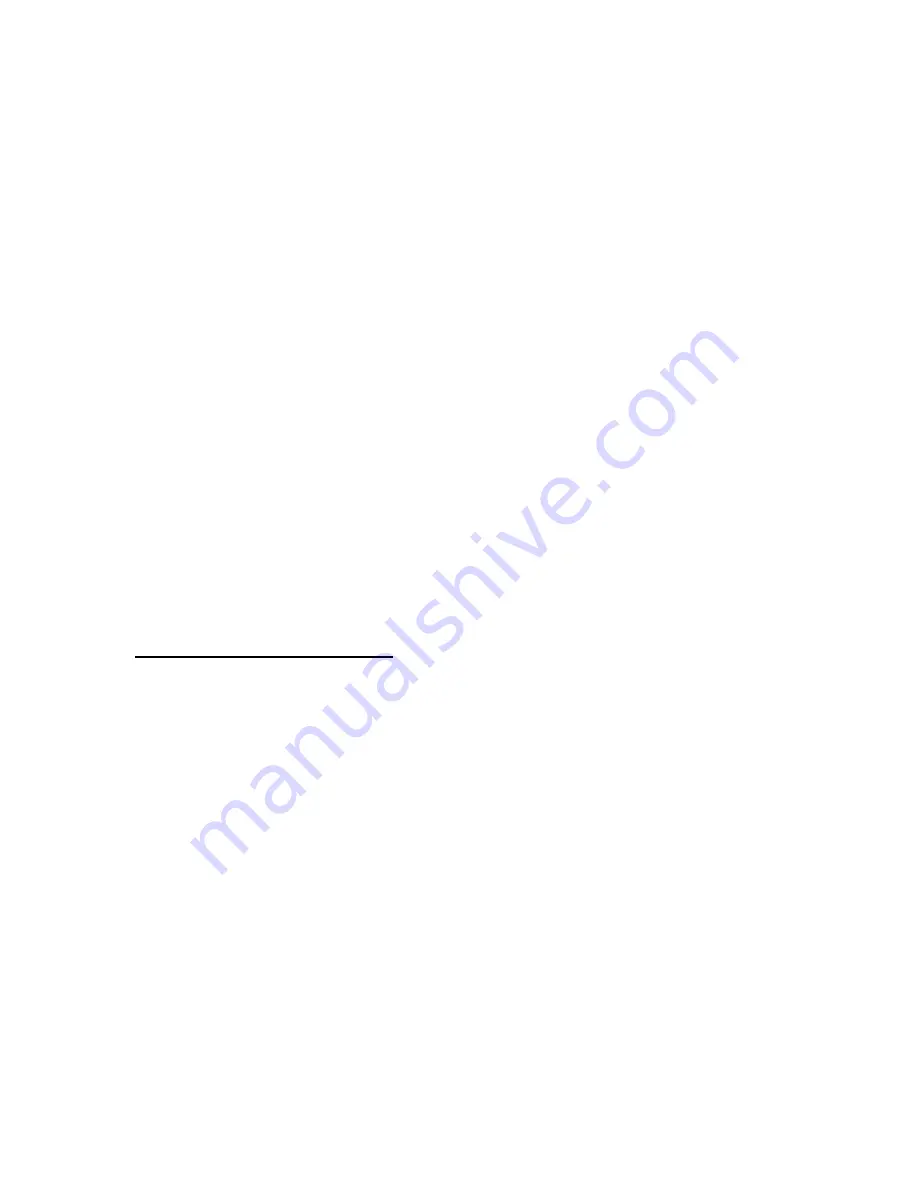
SLD/DLD/PLD AIR COOLED CONDENSING UNITS
6
cause liquid to return to the compressor.
Too high suction superheat may cause
excessive discharge temperatures. For
maximum system capacity the minimum
superheat must be 20 F and the maximum
superheat must be 30 F to 40 F at the
compressor for medium and low
temperature, respectively.
7) After several hours of operation, check
the compressor oil level. The oil level
should be 1/2 the way up on the glass with
the compressor off. Care must be taken to
be sure the proper lubricant is used.
8) On freezer system after the coil is frosted,
manually advance the defrost timer to
initiate a defrost. Observe the defrost cycle
to see if all controls are functioning properly
and that the coil is clear of all frost before
the system returns to refrigeration. Reset the
defrost timer to the correct time of day.
9) After the room has reached temperature
and the liquid line solenoid has closed,
check the compressor to be sure it has
pumped down and shut off. If the
compressor continues to run, check the low
pressure control setting as outlined in step
#2.
VII. FEATURES AND CONTROLS
1) REFRIGERANT OIL
The oil level should be 1/2 the way up on
the glass in the compressor with the
compressor off. Oil level should be checked
frequently during startup and during the first
48 hours of operating time. Since no
dependable rule of thumb can be used, the
only safe method is to carefully check the oil
level and add as little oil as needed. If oil is
required to be added, an oil pump is
recommended to pump the oil directly into
the compressor against suction pressure.
Refrigerant oil should be purchased in
sealed containers and should not be left open
to atmosphere. Exposure to air and moisture
for extended periods will result in
contamination of the oil and cause harmful
reactions in the compressor. Do not transfer
oil from one container to another.
2) HIGH AND LOW PRESSURE
CONTROLS
SLD/DLD/PLDs are furnished with
individual manual reset high-pressure and
low-pressure controls.
These are safety controls for the system.
(See Table 3).
3) OIL FAILURE SWITCH
Each compressor on the Model
SLD/PLD/DLD unit has its own electronic
oil pressure control. Should oil pump
differential pressure, measured between the
pump inlet and outlet, fall below 9 psig for a
period of two minutes, the control will open
and stop the compressor.
A trip of the oil pressure safety control is a
warning that the compressor has been
running without proper lubrication.
Repeated trips of the control are a clear
indication that something in the system
requires immediate attention and corrective
action.
If system is plagued with oil failure safety
switch tripouts, it is almost always traceable
to one of the following sources.
a) Shortage of oil in the compressor
b)
Oil trapping in the system
c)
Liquid slugback to the compressor for
some reason.
d)
Compressor short cycling
e)
Refrigerant in the oil on startup
f)
Malfunctioning oil pump
g)
Clogged on the oil suction screen
h)
Excessively low suction pressure
i)
Possibly a defective control, but not
probable
j)
Low refrigerant charge in low ambient
conditions
4) CRANKCASE HEATERS
Crankcase heaters are provided to reduce the
possibility of refrigerant condensing in the
crankcase oil.