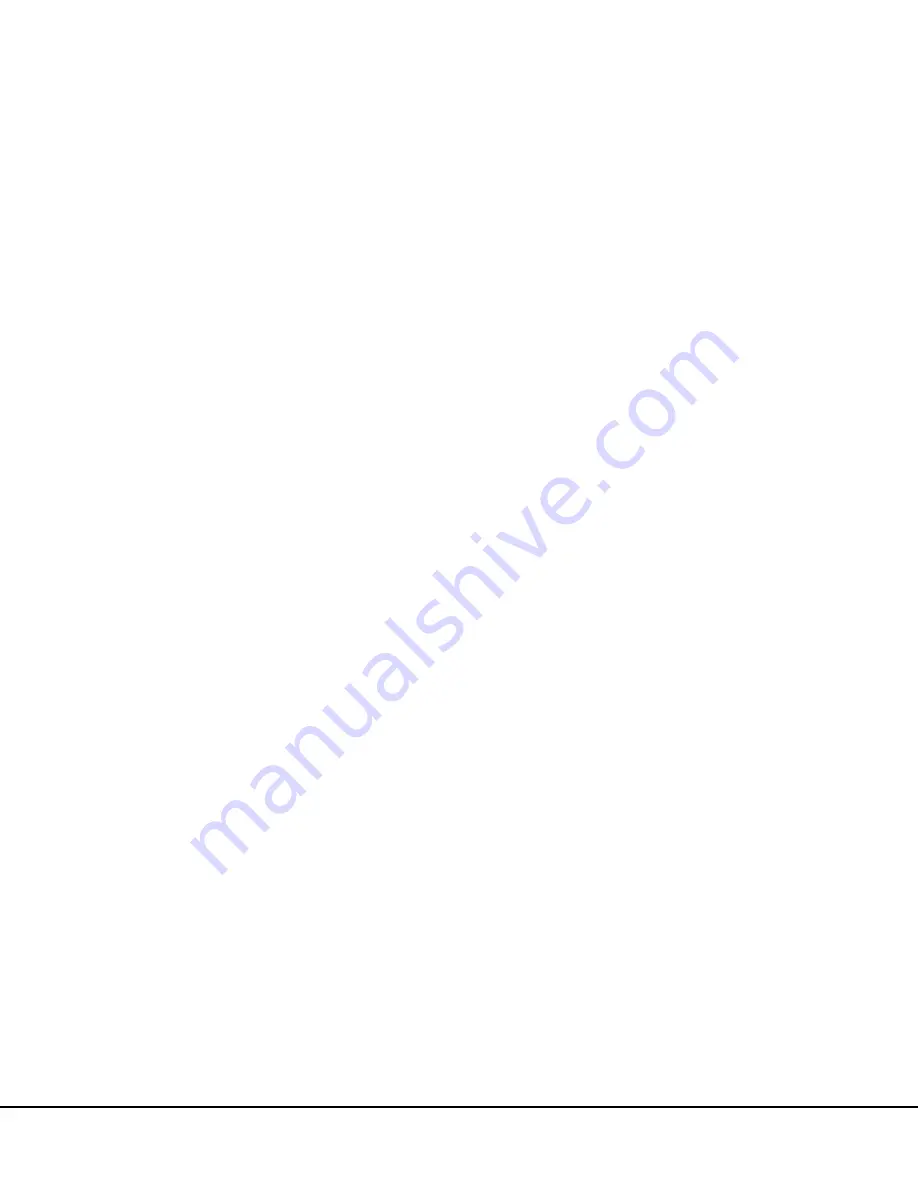
E02016 2/02
Electrical Propulsion Components
E2-61
PTU ABBREVIATIONS
Due to limited screen space, many abbreviations are
necessary for displaying information on the various
screens. A definition of each abbreviation and special
term can be accessed as follows:
1. From the
GE OHV STATEX III MENU
, select
“PTU TALK TO TRUCK” to access the
STATEX
III PTU MAIN MENU
.
2. Move the cursor to select “PTU ABBREVIA-
TIONS” and press [ENTER].
3. The
GE STATEX III PTU ABBREVIATIONS
screen will appear with instructions for viewing
the information.
4. When finished viewing, press the [SPACE] bar to
leave the screen.
OTHER MENU SELECTIONS
Software menu items not covered in this section of the
manual are normally used for truck checkout and trou-
bleshooting only.
Refer to Section E3 for information regarding use of the
following selections from the
GE STATEX III PTU
MAIN MENU
selections:
“NORMAL OPERATION”
•
View Real Time Data
•
View Analog Inputs
•
Load Box Test
•
Accelerate Logic Help
•
Retard Logic Help
“SPECIAL OPERATION WITH ENGINE STOPPED”
•
Test - Digital Outputs
Содержание 830E
Страница 1: ...CEBM013200 Shop Manual DUMP TRUCK SERIAL NUMBERS A30708 A30732 ...
Страница 2: ......
Страница 4: ...NOTES ...
Страница 8: ...A 4 Introduction A00032 KOMATSU MODEL 830E TRUCK ...
Страница 9: ... ...
Страница 10: ... ...
Страница 12: ...A2 2 Major Component Description A02063 830E MAJOR COMPONENTS ...
Страница 32: ...A3 18 General Safety and Operating Instructions A03020 NOTES ...
Страница 34: ...A3 20 General Safety and Operating Instructions A03020 ...
Страница 46: ...A3 32 General Safety and Operating Instructions A03020 NOTES ...
Страница 61: ... 0 1 23 4 5 67 5 789574 0 ...
Страница 62: ... 7 4 4 0 5 0 8 3 7 4 4 2 1 5 4 4 4 A 4 4 4 8 8 4 0 4 5 67 5 789574 0 1 23 ...
Страница 63: ... 7 5 0 3 A B 594 5 4 5 4 7 2 C 4 7 D 7 D 1 5 4 4 4 5 5 8 D 0 A 4 4 4 3 8 2 0 1 23 4 5 67 5 789574 0 ...
Страница 64: ... 4 1 5 4 4 4 0 3 9 2 C C 0 4 5 67 5 789574 0 1 23 ...
Страница 65: ... 0 0 1 5 5 5 2 3 4 5 1 1 1 0 0 1 23 4 5 67 5 789574 0 ...
Страница 66: ... 4 5 6 8 4 4 E C 4 4 4 E C 4 4 7 D 5 6 7 5 9 4 4 8 5 4 4 4 5 0 D 9 0 4 5 67 5 789574 0 1 23 ...
Страница 67: ...3 5 5 4 5 2 8 5 5 D 4 4 1 1 1 6 1 1 7 8 5 5 0 1 23 4 5 67 5 789574 00 ...
Страница 68: ... 2 8 0 7 5 2 5 8 F 03 4 5 67 5 789574 0 1 23 ...
Страница 69: ...1 C 8 D 8 6 4 G 5 4 8 D 8 F 4 4 4 G 1 8 D 0 1 23 4 5 67 5 789574 02 ...
Страница 70: ... 6 8 7 0 H 8 9 9 8 A 5 A 3 4 2 4 5 0 3 2 8 9 8 4 8 0 4 0 C 5 7 4 4 7 5 5 7 4 4 7 4 0 4 5 67 5 789574 0 1 23 ...
Страница 72: ... 2 3 2 G 8 4 8 8 4 D 2 6 7 0 4 1 3 2 G 8 5 4 8 8 4 5 5 0 4 5 67 5 789574 0 1 23 ...
Страница 74: ... 6 7 8 5 8 5 5 5 5 4 8 8 4 8 8 4 0 4 8 8 4 3 2 4 8 8 4 5 5 4 7 8 8 4 0 4 5 67 5 789574 0 1 23 ...
Страница 75: ... 9 6 7 4 C F F F 0 0 8 0 0 F 0 88 1 6 7 G 6 G 8 G 8 4 6 7 4 4 0 2 0 1 23 4 5 67 5 789574 0 ...
Страница 77: ... G 5 5 5 5 5 5 G 6 5 6 G 5 5 5 5 4 D 0 5 D 6 7 4 3 G 5 8 2 C 5 D 0 1 23 4 5 67 5 789574 0 0 ...
Страница 78: ... 0 3 4 5 67 5 789574 0 1 23 ...
Страница 79: ... A 6 8 4 J 4 02 6 2 8 J 1 C E 2 3 4 1 5 8 5 0H 5 0H 8 5 0H 0 3 02 2 3 E C E 5 5 5 0 1 23 4 5 67 5 789574 0 2 ...
Страница 80: ...0 4 5 67 5 789574 0 1 23 ...
Страница 82: ...NOTES B1 2 Index B01018 ...
Страница 92: ...NOTES B3 6 Dump Body B03018 ...
Страница 94: ...C1 2 Index C01024 NOTES ...
Страница 116: ...NOTES C5 6 Air Filtration System C05012 4 98 ...
Страница 135: ...D02023 24 VDC Electric Supply System D2 17 FIGURE 2 8 CRANKING MOTOR ASSEMBLY ...
Страница 181: ...E02016 2 02 Electrical Propulsion Components E2 25 ...
Страница 228: ...E2 72 Electrical Propulsion Components 2 02 E02016 NOTES ...
Страница 290: ...G2 8 Tires and Rims 04 03 G02004 NOTES ...
Страница 304: ...G3 14 Front Wheel Hub and Spindle 04 03 G03018 NOTES ...
Страница 312: ...H1 2 Index 5 03 H01015 NOTES ...
Страница 324: ...H3 4 Rear Suspensions 4 03 H03015 ...
Страница 328: ...2 6 27 6 7 6 7 6 7 67 B 67 6 7 C 6 27 6 7 2 6 27 67 2 67 6 7 5 0 5 0 0 67 0 6 7 5 4 0 D 6 7 E 4 4 ...
Страница 331: ... 0 0 6 76 6 7 5 5 M A 5 5 0 1 23 4 0 1 5 6 7 6 4 7 G 2 6 7 3 3 H I 5 5 3 HH ...
Страница 333: ...C B 654 7 H 6 27 0 L C N 6 2J 7 5 0 M 6 27 1 J 5 654 27 0 5 0 5 0 5 0 67 0 6 7 A ...
Страница 342: ...1 Actuator Base 2 Brake Valve 3 Orfice Set Screw FIGURE 2 3 BRAKE VALVE PARTIAL CUT AWAY J2 6 Brake Circuit J02032 ...
Страница 370: ...J4 10 Brake Circuit Check Out Procedure J04031 NOTES ...
Страница 380: ...J5 8 Rockwell Wheel Speed Front Disc Brakes J05019 NOTES ...
Страница 410: ...L2 4 Hydraulic System L02027 NOTES ...
Страница 426: ...L3 16 Hydraulic Component Repair 7 02 L03026 NOTES ...
Страница 429: ...L04037 Steering Circuit L4 3 FIGURE 4 2 FLOW AMPLIFIER ...
Страница 431: ...L04037 Steering Circuit L4 5 FIGURE 4 3 FLOW AMPLIFIER No Steer ...
Страница 433: ...L04037 Steering Circuit L4 7 FIGURE 4 4 FLOW AMPLIFIER Steering Left ...
Страница 435: ...L04037 Steering Circuit L4 9 FIGURE 4 5 FLOW AMPLIFIER Steering Right ...
Страница 437: ...L04037 Steering Circuit L4 11 FIGURE 4 6 FLOW AMPLIFIER No Steer External Shock Load ...
Страница 441: ...L04037 Steering Circuit L4 15 FIGURE 4 9 CUT AWAY VIEW OF STEERING PUMP ...
Страница 444: ...L4 18 Steering Circuit L04037 NOTES ...
Страница 453: ...L05026 Steering Component Repair L5 9 FIGURE 5 7 FLOW AMPLIFIER VALVE ...
Страница 476: ...L5 32 Steering Component Repair L05026 NOTES ...
Страница 483: ...L07027 Hoist Circuit L7 7 FIGURE 7 6 FLOAT POSITION ...
Страница 485: ...L07027 Hoist Circuit L7 9 FIGURE 7 7 POWER UP ...
Страница 487: ...L07027 Hoist Circuit L7 11 FIGURE 7 8 HOLD POSITION ...
Страница 489: ...L07027 Hoist Circuit L7 13 FIGURE 7 9 POWER DOWN ...
Страница 491: ...L07027 Hoist Circuit L7 15 FIGURE 7 10 FLOAT POSITION ...
Страница 492: ...L7 16 Hoist Circuit L07027 NOTES ...
Страница 504: ...L8 12 Hoist Circuit Component Repair L08031 FIGURE 8 18 HOIST CYLINDER ...
Страница 512: ...L8 20 Hoist Circuit Component Repair L08031 NOTES ...
Страница 523: ...L10016 05 03 Hydraulic Check out Procedure L10 11 FIGURE 10 5 FLOW AMPLIFIER VALVE ...
Страница 532: ...NOTES M1 2 Index M01047 ...
Страница 546: ...NOTES M5 4 Wiggins Quick Fill Fuel System M05002 10 96 ...
Страница 556: ...NOTES M8 6 Special Tools M08005 7 02 ...
Страница 592: ...M9 36 Air Conditioning System 05 02 M09010 for HFC 134a Refrigerant NOTES ...
Страница 596: ...M19 4 Radiator Shutters M19002 NOTES ...
Страница 597: ... 0 1 0 2 3 3 1 1 3 4 5 1 4 6 6 1 6 6 1 6 6 1 7 18 1 9 1 1 1 0 1 1 1 4 4 3 3 4 7 7 4 3 8 8 3 ...
Страница 598: ... 3 3 4 1 1 6 6 6 6 6 0 0 2 2 0 1 0 0 3 3 7 3 6 6 7 7 8 1 1 4 2 4 1 1 51 1 3 1 1 1 1 ...
Страница 599: ... 5 4 1 6 1 1 1 4 1 1 4 1 1 1 4 1 3 1 4 6 1 4 4 2 54 0 3 1 3 3 3 6 1 2 0 1 0 0 3 1 1 3 A ...
Страница 601: ... 1 B 0 C 8 D B 3 0 C 8 8 8 I 8 6 J 8 D I 8 8 D 0 8 8 K 8 8 8 8 3 6 B 0 C B C J 0 1 8 J L 0L 0 D D 1 ...
Страница 604: ... 1 0 8 D 1 4 J D 7 1 L 8 6 0 8 0 8 3 1 3 N 8 3 1 0 N 3 1 ...
Страница 609: ... 1 8 0 8 8 7 8 8 8 8 0 3N 0 0 0 8 4 1 8 D 8 0 8 0 1 8 1 4 D 3 1 4 D 8 D 8 T D 63 8 8 ...
Страница 614: ... 1 1 0 0 D 0 8 8 0 0 H 0 D D D D 8 D D 0 8 8 0 0 8 8 D E D 8 0 8 ...
Страница 615: ...6 D 0 P Q D 0 8 D 0 8 8 D D E D D 2 D E 8 O E E 8 O F 0 0 F 0 0 F 8 F 8 F 8 8 8 D 8 8 F 8 8 8 F 1 7 8 0 ...
Страница 616: ... 8 8 D 1 G J 4 D 0 F 6 0 1 1 0 0 4 D 8 8 D 1 8 8 D 8 D 0 6 E 0 8 8 8 E 0 8 8 8 ...
Страница 617: ... 0 D 0 8 L 0 B 0 C B C 8 0 D 8 3 0 0 8 0 0 D 0 8 0 0 0 8 0 0 1 0 0 D 0 8 0 2 2 2 0 D 8 0 8 2 2 0 D 8 ...
Страница 618: ... 0 8 0 0 0 8 0 D D 0 0 8 D 0 8 0 0 8 D 1 0 D 0 0 8 8 0 0 8 D 1 0 D 4 0 0 0 D P Q 0 8 0 0 D 4 0 0 0 D P Q 8 8 ...
Страница 619: ... 7 0 D D D D 0 0 9 0 D D 0 8 0J D 0 0 0 0 0 0 0 4 D 0 0 D 0 0 3 D 3 0 H 0 2 0 0 8 0 D 6 0 ...
Страница 621: ... 8 8 P Q D 0 8 D 0 3 T D E E 9 2 2 1 2 7 2 17 2 5 7 5 A 7 5 7 5 B 7 5 7 9 2 21 1 21 2 2 9 ...
Страница 622: ... E H D D D D D D D D ...
Страница 623: ...3 1 0 H H T 0 D P Q D 0 3 T D E E 9 P Q 1 7 8 7 8 8 8 P Q H 8 7 H F P 7Q F PK Q 8 7 7 0 1 8 D 7 ...
Страница 625: ...6 8 4 2 D A K 0 8 0 0 D P Q 0 H D H D P Q D H 8 0 ...
Страница 626: ... D 0 P Q 8 8 D P Q D PH Q 8 0 ...
Страница 627: ... 0 0 1 2 0 3 3 0 3 3 4 5 2 0 1 3 3 3 3 2 3 3 6 6 1 3 3 3 3 7 2 8 9 4 4 4 4 4 2 3 3 4 2 3 3 ...
Страница 628: ... 2 2 0 4 5 1 1 4 4 1 1 3 3 3 3 7 4 3 1 3 2 2 3 23 0 8 9 4 A 8 9 4 4 4 4 4 0 2 4 4 B 4 4 4 ...
Страница 629: ... 4 4 4 ...
Страница 630: ...7 0 1 C 2 70 70D 4 0 4 C 2 4 8 9 ...
Страница 631: ...0 4 4 8 5 E 9 ...
Страница 632: ... 0 1 3 3 F 4 G H 4 F 4 C 2 4 8 119 5 4 8 9 ...
Страница 633: ...A 2 4 8 4 4 3 5 F 4 0 4 C 2 4 ...
Страница 634: ... 3 0 5 3 6 3 ...
Страница 635: ...I 4 F 4 4 4 ...
Страница 636: ...7 0 7 7 7 C 2 I1 2 7 C 2 7 1 7 I ...
Страница 637: ...7 4 0 7 7 7 C 2 I1 2 7 C 2 7 J 7 ...
Страница 638: ...7 5 6 0 7 7 7 C 2 I1 2 7 C 2 7 J 7 ...
Страница 639: ...7 7 8 0 7 7 7 C 2 I1 2 7 C 2 7 J 7 ...
Страница 640: ...77 9 0 I1 0 0 C 2 7 ...
Страница 641: ...70 5 4 0 K 4 ...
Страница 642: ...7 5 0 6 4 1 1 4 8 119 5 8 119 5 8 9 ...
Страница 643: ...7A 30 6 7 4 8 119 5 4 8 9 2 ...
Страница 644: ...7 ...
Страница 645: ...7I ...
Страница 646: ...0 ...
Страница 647: ... 0 1 2 3 4 5 62 4 62 6 4 5 62 4 62 6 4 7 5 6 4 6 6 2 4 7 5 6 4 4 6 6 0 8 5 9 62 6 62 2 0 8 5 62 0 62 7 0 1 ...
Страница 648: ... 0 7 0 7 0 7 0 7 2 1 3 A 1 2 3 0 7 2 1 3 A 1 2 3 2 0 7 2 1 3 A 1 2 3 0 7 2 1 3 A 1 2 3 0 7 A B C 8 0 7 0 0 7 D D ...
Страница 649: ... D D 0 4 D 4D 0 E F G G H G 9 0 G G 2 G G D D E 2 3 G G D D I 4 4 4 5 3 4 6 5 G G D D I ...
Страница 652: ... 2 67 D D 5 4 M6 5 N 2 M6 5 N DI D 5 2 6 OI M6 P 4 I ...
Страница 653: ... A 0 A E 0 7 0 7 7 7 9 4 7 6 0 6 E E 7 0 ...
Страница 654: ...0 1 0 9 2 4 7 7 7 E 7 0 4 9 4J0 4 4 E7 9 J 47 4 E 4 E7 E 7 0 7 09 49 6E E 2 2 ...
Страница 678: ...N2 16 Truck Cab 04 03 N02014 NOTES ...
Страница 682: ...N3 4 Cab Components N03018 NOTES ...
Страница 688: ...N4 6 Operator Comfort N04023 NOTES ...
Страница 710: ...N5 22 Operator Controls N05056 NOTES ...
Страница 712: ...P1 2 Index P01028 NOTES ...
Страница 715: ...P02039 Lubrication and Service P2 3 ...
Страница 726: ...P2 14 Lubrication and Service P02039 NOTES ...
Страница 744: ...P3 18 Automatic Lubrication System P03022 NOTES ...
Страница 745: ... 0 0 1 2 0 0 3 3 0 0 1 2 0 4 5 6 7 6 4 ...
Страница 746: ...8 9 9 8 9 9 9 9 2 8 3 1 1 3 3 9 9 9 0 3 4 6 7 6 4 5 ...
Страница 747: ... 8 9 9 8 9 5 9 9 5 2 9 9 8 3 8 9 9 8 9 9 9 5 2 9 9 8 3 3 9 A4 0 9 9 9 9 9 3 9 9 9 9 9 4 5 6 7 6 4 ...
Страница 748: ... 1 9 B 9 3 9 B 3 0 0 0 B 2 1 A 9 B 3 46 2 46 B 3 3 6 5 B 3 46 3 6 B 4 6 7 6 4 5 ...
Страница 754: ...R1 2 System Schematics R01060 NOTES ...
Страница 755: ......
Страница 756: ...Electrical Schematic HH354 Jun 03 Hydrauiic Schematic Brake System 830E Effective with A30650 UP ...
Страница 758: ......
Страница 759: ......
Страница 760: ......
Страница 761: ......
Страница 762: ......
Страница 763: ......
Страница 764: ......
Страница 765: ......
Страница 766: ......
Страница 767: ......
Страница 768: ......
Страница 769: ......
Страница 770: ......
Страница 771: ......
Страница 772: ......
Страница 773: ......
Страница 774: ......
Страница 775: ......
Страница 776: ......
Страница 777: ......
Страница 778: ......
Страница 779: ......
Страница 780: ......
Страница 781: ......
Страница 782: ......
Страница 783: ......