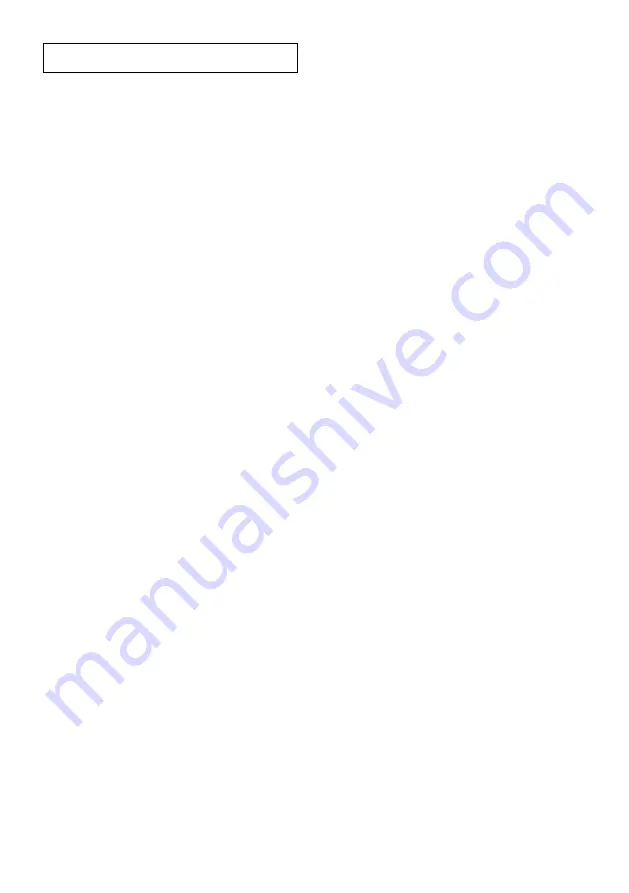
8
1057616-W2-J
INSTALLATION
General
Installation must be carried out in accordance
with these instructions, and must be conducted by
designated, qualified and competent personnel.
1.
Before commencing, make sure that the
installation conditions comply with the
information given in section:
'Specifications'
.
For Type 3 valves. See also installation
conditions in the
'TMV3 Requirements
Manual'
.
2.
The mixing valve should be positioned for
easy access during use and maintenance.
All routine maintenance procedures can
be conducted with the mixing valve body
in place (except for strainer and non return
valve access on dk and oem models). For all
models, allow a minimum of 80 mm clearance
in front of the temperature control to enable
removal of the Thermostatic Cartridge during
maintenance.
3.
Conveniently situated ‘full bore’ isolating
valves must be provided for maintenance
purposes.
4.
The use of supply-line or zone strainers
will reduce the need to remove debris at
each mixing valve point. The recommended
maximum mesh aperture dimension for such
strainers is 0.3 mm.
5.
Inlet pressure tappings which allow
measurement of the inlet pressures to the
mixing valve under operating conditions are
particularly recommended for healthcare
applications with Type 3 valves.
6.
Pipework must be rigidly supported.
7.
Certain types of system can result in the
thermostatic mixing valve having excessive
‘dead-legs’ of pipework, or auxiliary cold
water supply added to the mixed water from
the thermostatic mixing valve. Such systems
can disguise the onset of thermostatic mixing
valve malfunction and should not be used.
8.
Supply pipework layout should be arranged to
minimise the effect of other outlet usage upon
the pressures at the mixing valve inlets.
9.
Inlet and outlet threaded joint connections
should be made with PTFE tape or liquid
sealant. Do not use oil-based, non-setting
jointing compounds.
10.
To eliminate pipe debris it is essential that
supply pipes are thoroughly flushed through
before connection to the mixing valve.
Outlet Position / Reversed Inlet
Supplies
Rada 215-t3 oem, 215 dk, 215-t3 dk, 222 dk and
222-t3 dk models only:
These models are readily adaptable for rising or
falling pipework; flat-faced union connectors (not
supplied on all models) allow the valve body to
accept a variety of pipework configurations, and
to be reversed or inverted as appropriate.
215-t3 c and 215-t3 zc models only:
These models are supplied with inlet connections
configured hot - left, cold - right, and top outlet
as standard. It is essential that the inlet supplies
correspond with the markings on the thermostatic
cartridge. Should the existing hot and cold
pipework make this configuration inconvenient,
or a bottom outlet position be required, the valve
inlets or outlet can be reversed, as detailed
below. If both the outlet and inlet positions
require reversing, it is easier to simply rotate the
complete mixing valve 180°, and then reposition
the temperature knob or cap.
Outlet Reversal
should be done
prior
to
installation of the mixing valve body. Rotate the
body 180° so that the outlet is in the opposite
direction, then follow the procedure for reversing
the cartridge .
Reversed connections
can be altered before or
after mixing valve installation.
Reversing the Cartridge
1.
If the mixing valve has already been installed,
isolate the supplies and open an outlet fitting
to release pressure and to assist the draining
of residual water.
2.
Remove the temperature knob or locking cap,
using a 3 mm hexagonal key.
Note!
Do not remove the temperature hub.
3.
With the removal clip in place, unscrew the
head nut using a 35 mm wrench, this will begin
to draw the thermostatic cartridge out of the
body and release the indicator trim (adjustable
models).
Содержание Rada 215 Series
Страница 30: ...30 1057616 W2 J NOTES...
Страница 31: ...31 1057616 W2 J...