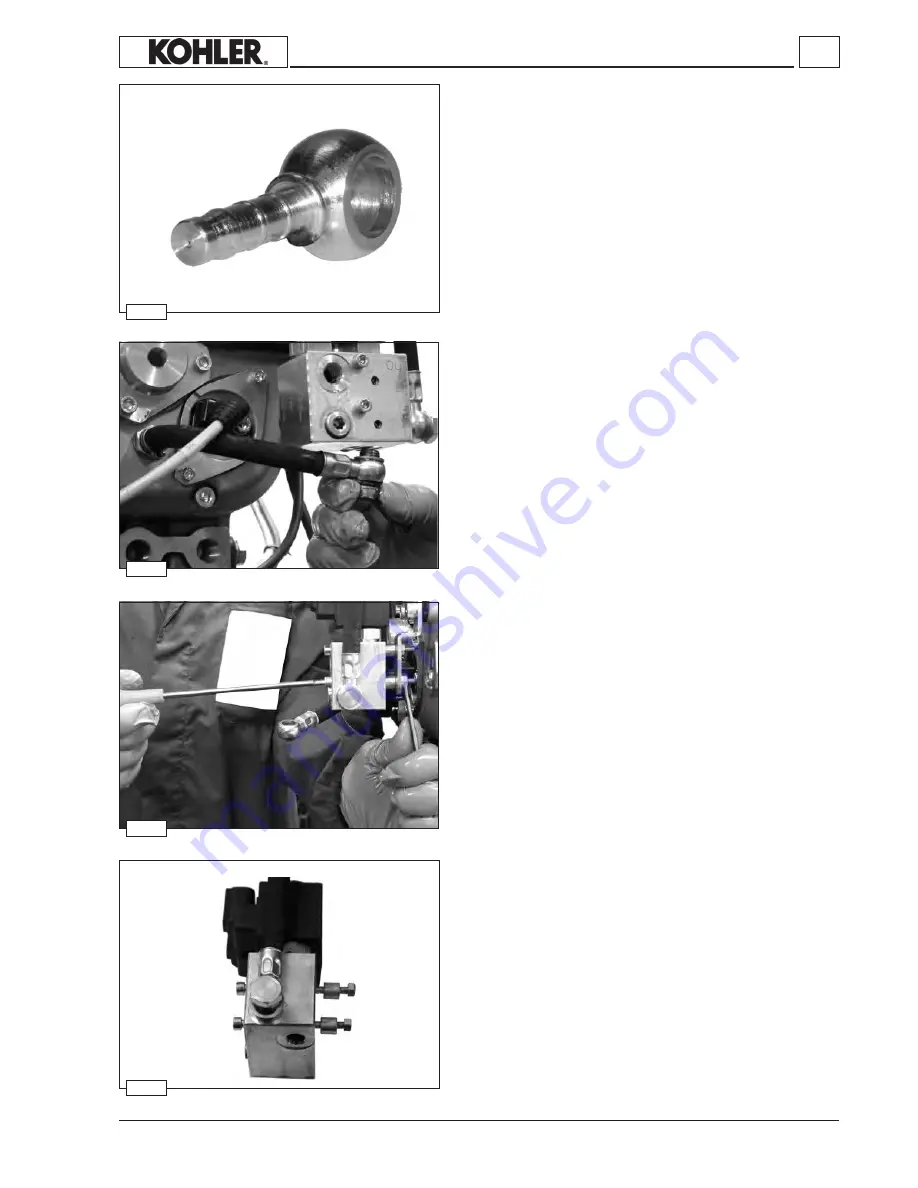
- 77 -
II
A_12
A_13
A_14
A_15
Variator lubrication jet complete with banjo union.
Disassembly / Reassembly
View of the unassembled solenoid valve block with two spacers
between the block and the bracket.
To remove the solenoid valve block from the support bracket, unscrew
the two screws M 5.
Unscrew the union of variator oil discharge pipe
20
.
KD Workshop Manual_cod. ED0053029350_
1° ed
_ rev.
00
Содержание KD 626/3
Страница 1: ...KD 625 3 626 3 WORKSHOP MANUAL...
Страница 21: ...21 3 KD Workshop Manual_cod ED0053029350_1 ed_ rev 00...
Страница 69: ...69 NOTES KD Workshop Manual_cod ED0053029350_1 ed_ rev 00...
Страница 70: ...70 NOTES KD Workshop Manual_cod ED0053029350_1 ed_ rev 00...
Страница 99: ...99 NOTES KD Workshop Manual_cod ED0053029350_1 ed_ rev 00...