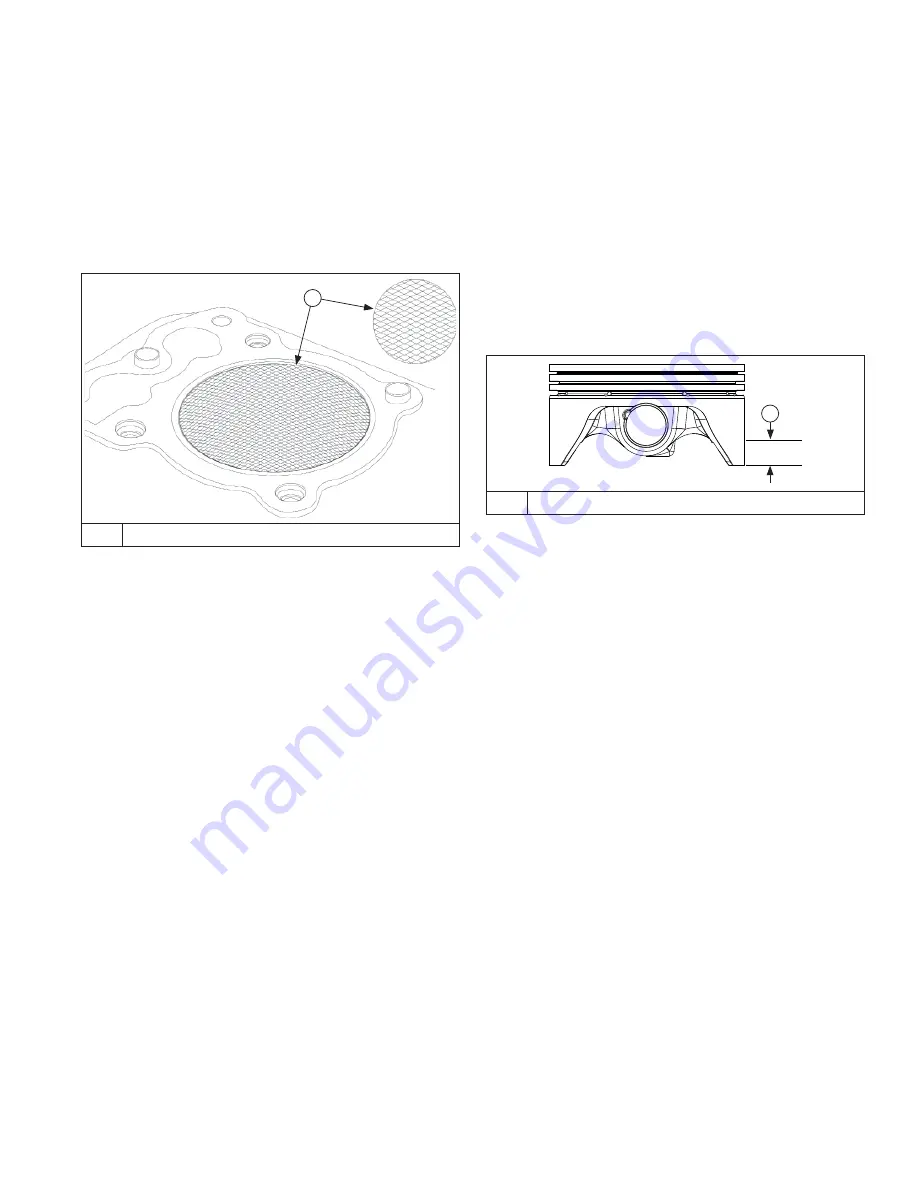
85
Disassembly/Inspection and Service
66 690 14 Rev. A
KohlerEngines.com
If cylinder bore is badly scored, excessively worn,
tapered, or out-of-round, resizing is necessary. Use
an inside micrometer to determine amount of wear,
then select nearest suitable oversize of either 0.08 mm
(0.003 in.), 0.25 mm (0.010 in.), or 0.50 mm (0.020 in.).
Resizing to one of these oversizes will allow usage of
available oversize piston and ring assemblies. Initially,
resize using a boring bar, then use following procedures
for honing cylinder.
Honing
Detail
A
A
23°-33° Crosshatch
While most commercially available cylinder hones can
be used with either portable drills or drill presses, use
of a low speed drill press is preferred as it facilitates
more accurate alignment of bore in relation to crankshaft
crossbore. Honing is best accomplished at a drill speed
of about 250 RPM and 60 strokes per minute. After
installing coarse stones in hone, proceed as follows:
1. Lower hone into bore and after centering, adjust so
that stones are in contact with cylinder wall. Use of a
commercial cutting-cooling agent is recommended.
2. With lower edge of each stone positioned even with
lowest edge of bore, start drill and honing process.
Move hone up and down while resizing to prevent
formation of cutting ridges. Check size frequently.
3. When bore is within 0.064 mm (0.0025 in.) of
desired size, remove coarse stones and replace with
burnishing stones. Continue with burnishing stones
until within 0.013 mm (0.0005 in.) of desired size and
then use
fi
nish stones (220-280 grit) and polish to
fi
nal size. A crosshatch should be observed if honing
is done correctly. Crosshatch should intersect at
approximately 23-33° o
ff
horizontal. Too
fl
at an angle
could cause rings to skip and wear excessively, too
steep an angle will result in high oil consumption.
4. After resizing, check bore for roundness, taper, and
size. Use an inside micrometer, telescoping gauge,
or bore gauge to take measurements. These
measurements should be taken at 3 locations in
cylinder-at top, middle, and bottom. There are 2
measurements that should be taken (perpendicular
to each other) at all 3 locations.
Clean Cylinder Bore After Honing
Proper cleaning of cylinder walls following boring and/
or honing is very critical to a successful overhaul.
Machining grit left in cylinder bore can destroy an engine
in less than 1 hour of operation after a rebuild.
Final cleaning operation should always be a thorough
scrubbing with a brush and hot, soapy water. Use a
strong detergent that is capable of breaking down
machining oil while maintaining a good level of suds. If
suds break down during cleaning, discard dirty water and
start again with more hot water and detergent. Following
scrubbing, rinse cylinder with very hot, clear water, dry
it completely, and apply a light coating of engine oil to
prevent rusting.
Measuring Piston-to-Bore Clearance
Piston Detail
A
A
6 mm (0.2362 in.)
NOTE: Do not use a feeler gauge to measure piston-to-
bore clearance–it will yield inaccurate
measurements. Always use a micrometer.
Before installing piston into cylinder bore, it is necessary
that clearance be accurately checked. This step is
often overlooked, and if clearances are not within
speci
fi
cations, engine failure will usually result.
Use following procedure to accurately measure piston-
to-bore clearance:
1. Use a micrometer and measure diameter of piston
above bottom of piston skirt and perpendicular to
piston pin.
2. Use an inside micrometer, telescoping gauge, or
bore gauge and measure cylinder bore. Take
measurement approximately 63.5 mm (2.5 in.) below
top of bore and perpendicular to piston pin.
3. Piston-to-bore clearance is di
ff
erence between bore
diameter and piston diameter (step 2 minus step 1).
Содержание Aegis ELH775
Страница 9: ...9 Specifications 66 690 14 Rev A KohlerEngines com Engine Dimensions Top A B A Oil Fill Cap B Radiator...
Страница 103: ...103 66 690 14 Rev A KohlerEngines com...
Страница 104: ...8 85612 60663 1 1P66 690 14 2021 by Kohler Co All rights reserved 104 KohlerEngines com 66 690 14 Rev A...