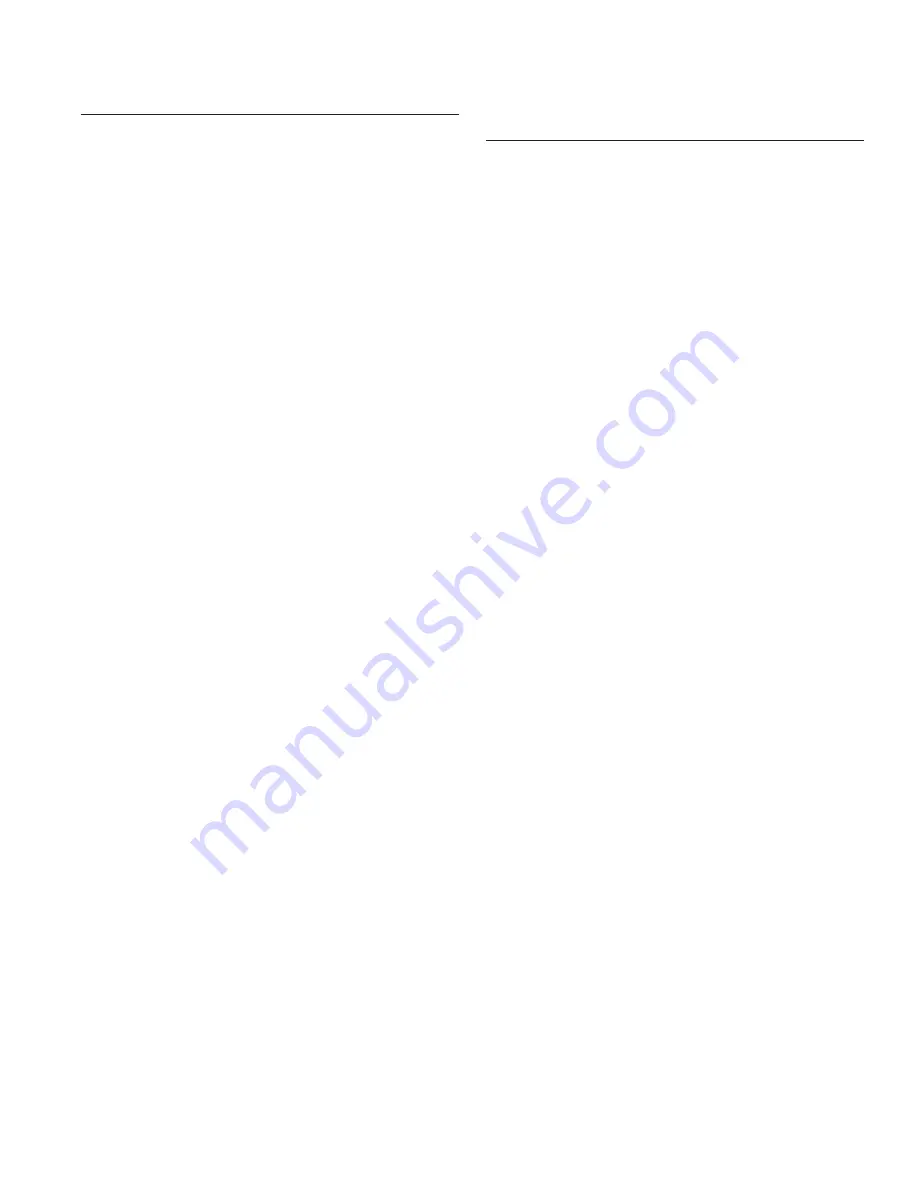
41
EFI System
66 690 14 Rev. A
KohlerEngines.com
Ignition Coil
If a coil is determined to be faulty, replacement is
necessary. Refer to Electrical System, Ignition System
Troubleshooting Guide Tests before performing coil tests
below. An ohmmeter may be used to test wiring and coil
windings.
NOTE: Do not ground primary coil leads with ignition
ON, as they may overheat or spark.
NOTE: Always disconnect spark plug lead from spark
plug before performing following tests.
NOTE:
If ignition coil(s) are disabled and an ignition
fault is registered, system will automatically
disable corresponding fuel injector drive
signal.
Fault must be corrected to ignition coil
and ECU power (switch) must be turned OFF for
10 seconds for injector signal to return. This is a
safety measure to prevent bore washing and oil
dilution.
Testing
Main purpose of performing ignition coil resistance test
is to identify if primary (low voltage) and secondary (high
voltage) circuits are shorted to each other or ground.
Coil resistance readings will vary based on temperature.
If coil passes spark testing, and primary and secondary
circuits are not shorted, resistance variations outside
speci
fi
ed range may be normal due to temperature.
Using an ohmmeter set on Rx1 scale, check resistance
in circuits as follows:
1. To check cylinder coil 1 (starter side), disconnect
Black connector from ECU and test between Black
pins 1 and 15. To check cylinder coil 2 (oil
fi
lter side),
disconnect Grey connector from ECU and test
between Grey pins 10 and 17. Wiring and coil
primary circuits are OK if readings are 0.5-0.8
2. If reading(s) are not within speci
fi
ed range, check
and clean connections and retest.
3. If reading(s) are still not within speci
fi
ed range, test
coils separately from main harness as follows:
a. Remove screw retaining coil to radiator mounting
bracket and disconnect primary leads connector.
b. Connect an ohmmeter set on Rx1 scale to
primary terminals of coil. Primary resistance
should be 0.5-0.8
Ω
.
c. Connect an ohmmeter set on Rx10K scale
between spark plug boot terminal and B+ primary
terminal. Secondary resistance should be no
more than 6400-7800
Ω
.
d. If secondary resistance is not within speci
fi
ed
range, coil is faulty and needs to be replaced.
FUEL COMPONENTS
Fuel Pump
Fuel pumps are non-serviceable and must be replaced
if determined to be faulty. If a fuel delivery problem
is suspected, make certain pump is being activated
through relay, all electrical connections are properly
secured, fuses are good, and a minimum of 7.0 volts
is being supplied. If during cranking, voltage drops
below 7.0 volts, a reduction of fuel pressure may occur
resulting in a lean starting condition. If required, testing
of fuel pump and relay may be conducted.
1. Relieve pressure at fuel connector. Wrap a shop
towel completely around fuel connector. Press
release button and slowly pull connector away
allowing shop towel to absorb any residual fuel in
high pressure fuel line. Insert pressure test jumper
(from Kohler EFI Service Kit) between high pressure
fuel line and fuel supply.
2. Connect black hose of Pressure Tester. Route clear
hose into a portable gasoline container or equipment
fuel tank.
3. Turn on key switch to activate pump and check
system pressure on gauge. If system pressure of 39
psi ± 3 is observed, relay, fuel pump, and fuel
pressure regulator are working properly. Turn key
switch o
ff
and depress valve button on tester to
relieve system pressure.
a. If pressure is too high, and regulator is outside
tank (just down line from pump), check that return
line from regulator to tank is not kinked or
blocked. If return line is good, replace regulator
(see Fuel Pressure Regulator).
b. If pressure is too low, install in-line T between
pump and regulator and retest pressure at that
point. If it is too low there also, replace fuel pump.
4. If pump did not activate (step 3), disconnect plug
from fuel pump. Connect a DC voltmeter across
terminals in plug, turn on key switch and observe if a
minimum of 7 volts is present. If voltage is between
7 and 14, turn key switch o
ff
and connect an
ohmmeter between terminals on pump to check for
continuity.
a. If there was no continuity between pump
terminals, replace fuel pump.
b. If voltage was below 7, test wiring harness and
relay as covered in Electrical Relay section.
5. If voltage at plug was good, and there was continuity
across pump terminals, reconnect plug to pump,
making sure you have a good connection. Turn on
key switch and listen for pump to activate.
a. If pump starts, repeat steps 2 and 3 to verify
correct pressure.
b. If pump still does not operate, replace it.
Содержание Aegis ELH775
Страница 9: ...9 Specifications 66 690 14 Rev A KohlerEngines com Engine Dimensions Top A B A Oil Fill Cap B Radiator...
Страница 103: ...103 66 690 14 Rev A KohlerEngines com...
Страница 104: ...8 85612 60663 1 1P66 690 14 2021 by Kohler Co All rights reserved 104 KohlerEngines com 66 690 14 Rev A...