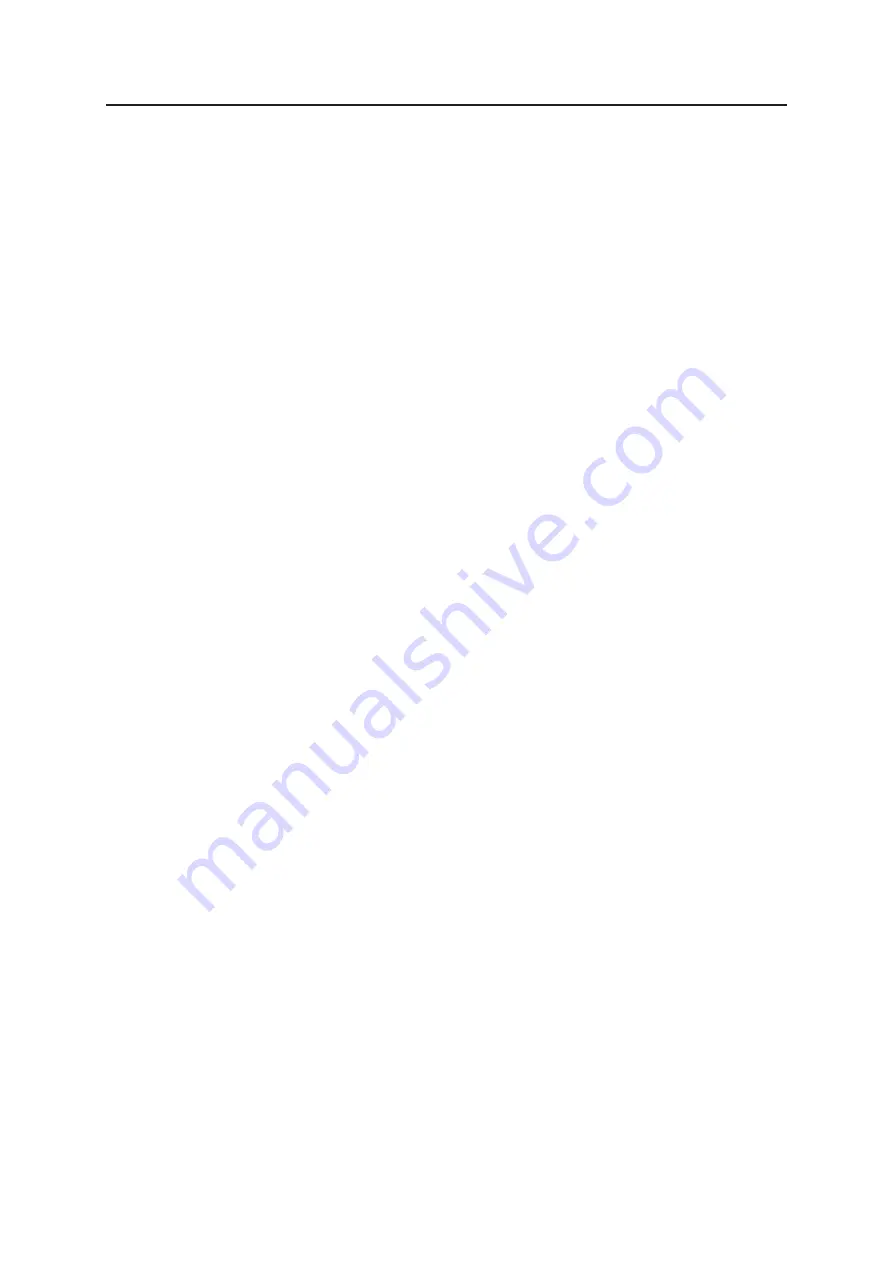
Index
SensoGate WA 132
A
Accessories 41
42
Adapter for free hose
connection 40
Air supply 40
Ambient temperature 5
Assembly, calibration chamber 31
Assembly, drive unit 26
Assembly, sensors 15
ATEX directive 42
ATEX marking 36
Attaching the media
connection 12
B
Basic SensoGate tool kit 40
Bayonet contour (U) 27
Bayonet coupling 29
Bellows 41
Blocking the retractable fitting 11
C
Cable jack (G) 22
Cable loop length 20
Calibration chamber, assembly 31
Calibration chamber,
dissassembly 30
Calibration chamber (K) 30
CE marking 5
Clamp (E) 23
Coding pin (O) 26
Compressed-air
connection (AL) 23
Compressed-air supply (Ex) 36
Conductivity, electrostatics 4
Connection (AC) to media hose 12
Connections, overview 36
Control air, connection
possibilities 8
Coupling nut (AH) 25
Coupling nut, large (S) 23
Coupling nut, small (R) 23
D
Declaration of Contamination 43
Dimension drawings (installation
Drinking water pipes 6
Drive unit, assembly 26
Drive unit, disassembly 25
Drive unit, servicing 38
Drive units, variants 10
E
Electrostatic charging 4
Equipotential bonding cable 23
EU Declaration of Conformity 42
Extension (V), sensor
installation 19
F
Filling hole (W) 23
Fixing bracket (H) for media
connection 12
Flange bushing (N) 30
Form-fit screw heads 29
Function description 8
G
Gasket material 39
Glass breakage 15
Guiding edges of calibration
H
Hazardous locations,
electrostatics 4
Hazardous locations,
specifications 36
Hose bracket (M), media
connection 12
Hose coupling (AE), media
connection 12
Hose, extension for air supply 40
Housing material 36
I
Icons 5
Immersion tube, assembly 29
Immersion tube, disassembly 28
Immersion tubes 10
Immersion tube, servicing 37
Immersion tube (T), design 27
Immersion tube, total length 27
Ingress protection 5
Installation dimensions 32
Installing a liquid-electrolyte
sensor 23
Installing a sensor,
preparations 15
Installing a solid-electrolyte
sensor, long 19
Installing a solid-electrolyte
sensor, short immersion 16
Installing the calibration
chamber 31
Installing the drive unit 26
Installing the immersion tube 29
Installing the media
connection 12
Intended Use 6
K
KEMA 36
L
Leakage hole 9
Length of immersion tube 27
Lift piston, SensoLock 11
Liquids, conductivity 4
Lock position 11
Loose flange 9
Lubricants 38
M
Maintenance intervals 37
Markings 5
Media connection 9
Media connection, installation 12
Modular design, retractable
fitting 10
Mounting angle 8
Mounting wrench 40
Moving to PROCESS position
blocked 11
Multiplug (AB) 12
O
Opening (AJ) in drive unit 26
Operating the retractable fitting 5
Order code 7
O-ring (D) on sensor 22
O-ring sets 39
Outlet hose (AF) 12
Outlet symbol 5
Overview of retractable fitting 9
P
Package contents 6
Permissible pressure for probe
control 36
Pressure chamber of sensor 40
Pressure ratings for electro-
pneumatic controller 36
Pressurized sensors 36
Process adaptation, modular
design 10
Process adaptation (P),
disassembly 30
Process adaptations,
specifications 36
4
3