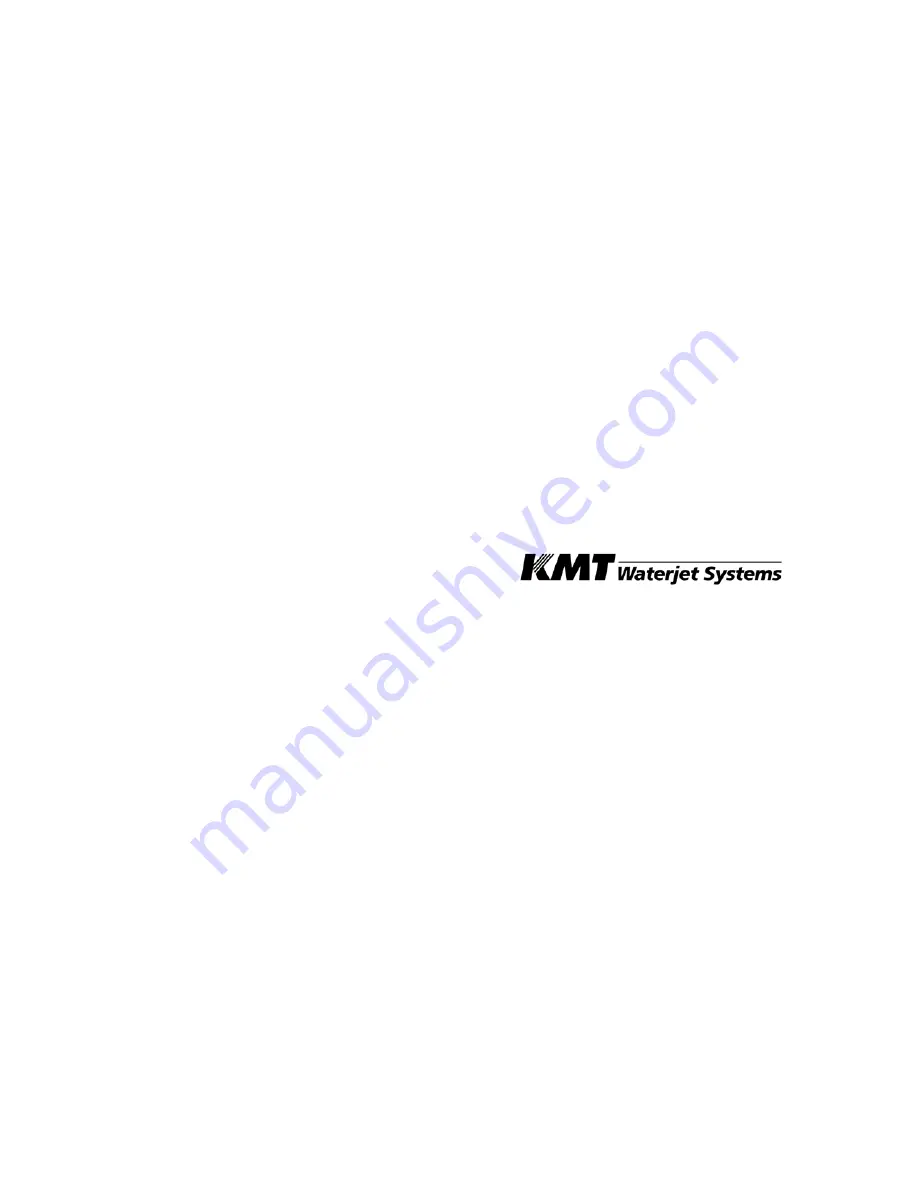
NOTICE
This document contains subject matter in which KMT
Waterjet Systems has proprietary rights. Recipients of
this document shall not duplicate, use, or disclose
information contained herein, in whole or in part, for other
than the purpose for which this manual was provided.
KMT Waterjet Systems believes the information described
in this manual to be accurate and reliable. Much care has
been taken in its preparation; however, the Company
cannot accept any responsibility, financial or otherwise,
for any consequences arising out of the use of this
material. The information contained herein is subject to
change, and revisions may be issued to advise of such
changes and/or additions
KMT Waterjet Systems
635 West 12
th
Street
PO Box 231
Baxter Springs, Kansas 66713
Tel. (800) 826-9274
FAX (620) 856-5050
49838857.doc
Содержание STREAMLINE SL-IV PLUS
Страница 44: ...SECTION 6 LOW PRESSURE WATER May 2003 6 4 05148390 Figure 6 2 LP Cutting Water Supply Circuit ...
Страница 78: ...SECTION 7 HIGH PRESSURE WATER May 2003 p 7 30 49831951 ...
Страница 82: ...SECTION 8 ELECTRICAL SYSTEM Aug 2002 p 8 4 49836323 ...
Страница 111: ...SECTION 12 PARTS LISTS July 2003 page 12 5 49836349 ...
Страница 113: ...SECTION 12 PARTS LISTS July 2003 page 12 7 49836349 ...
Страница 115: ...SECTION 12 PARTS LISTS July 2003 page 12 9 49836349 ...
Страница 117: ...SECTION 12 PARTS LISTS July 2003 page 12 11 49836349 ...
Страница 119: ...SECTION 12 PARTS LISTS July 2003 page 12 13 49836349 ...
Страница 121: ...SECTION 12 PARTS LISTS July 2003 page 12 15 49836349 ...
Страница 123: ...SECTION 12 PARTS LISTS July 2003 page 12 17 49836349 ...
Страница 125: ...SECTION 12 PARTS LISTS July 2003 page 12 19 49836349 ...
Страница 127: ...SECTION 12 PARTS LISTS July 2003 page 12 21 49836349 ...
Страница 129: ...SECTION 12 PARTS LISTS July 2003 page 12 23 49836349 ...
Страница 131: ...SECTION 12 PARTS LISTS July 2003 page 12 25 49836349 ...
Страница 133: ...SECTION 12 PARTS LISTS July 2003 page 12 27 49836349 ...
Страница 135: ...SECTION 12 PARTS LISTS July 2003 page 12 29 49836349 ...
Страница 137: ...SECTION 12 PARTS LISTS July 2003 page 12 31 49836349 ...
Страница 139: ...SECTION 12 PARTS LISTS July 2003 page 12 33 49836349 ...
Страница 141: ...SECTION 12 PARTS LISTS July 2003 page 12 35 49836349 ...
Страница 143: ...SECTION 12 PARTS LISTS July 2003 page 12 37 49836349 ...
Страница 145: ...SECTION 12 PARTS LISTS July 2003 page 12 39 49836349 ...
Страница 146: ......
Страница 147: ......