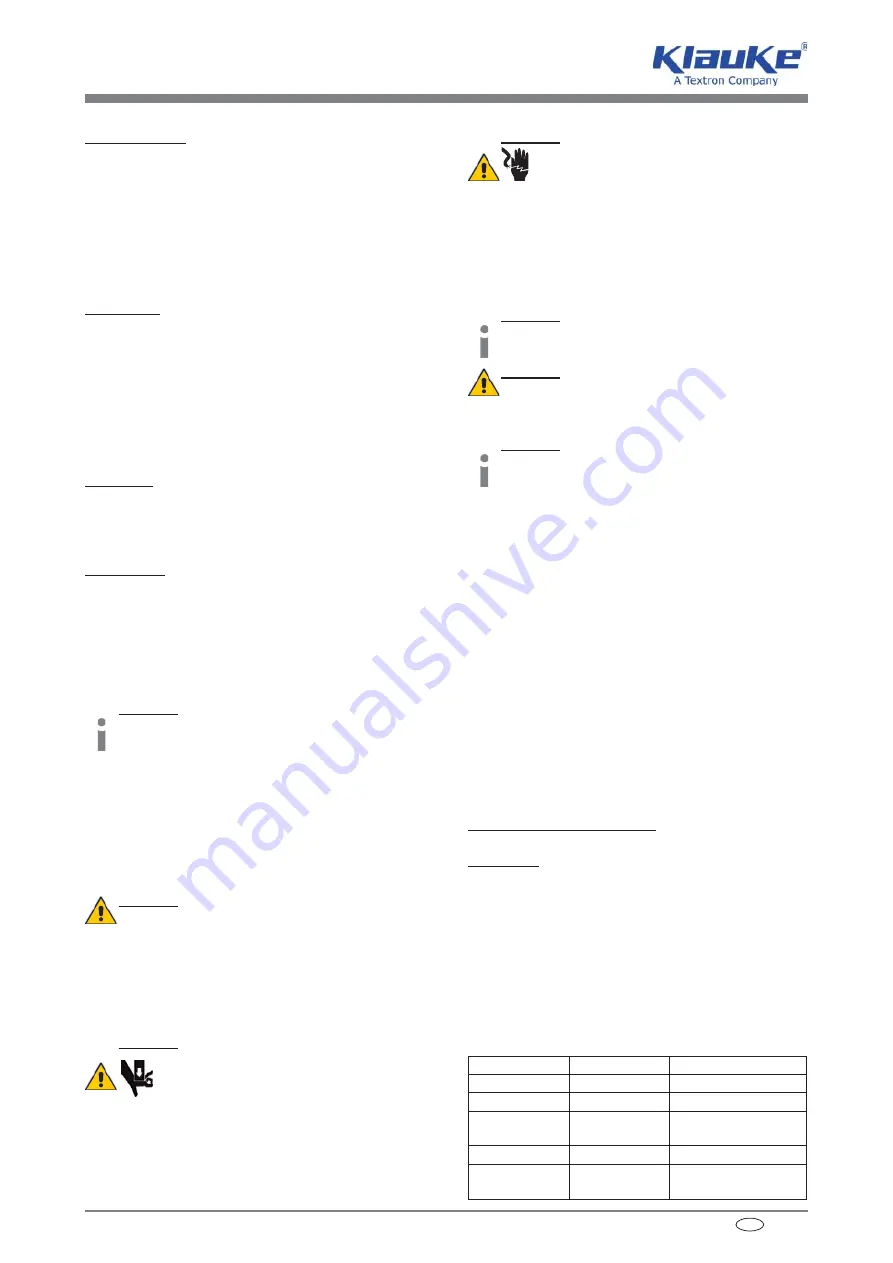
EHP4230
3
Instruction Manual
GB
HE.12929_E © 05/2011
8.2 Hole making
As indicated prior the knockout sizes are adjusted by the
speed adjustment button. The punch must be turned onto
the draw stud until there is a
fi
rm contact with the sheet
metal. The knockout cycle is started by actuating the sa-
fety foot switch. Just before or shortly after completing the
knockout the pump switches into the creep speed. The
user gains a signi
fi
cant amount of time to release the foot
switch, respectively end the knockout cycle in order to
avoid a fatal contact between punch and die.
8.3 Bending
Operating the pump with the Bus Bar Tool Center (BBTC)
the approach switch with the hand trigger must be con-
nected to the pump via the socket (pic. 1.2) as well as
the hydraulic hose. The user can now decide with which
speed he prefers to operate the piston of the Bus Bar Tool
Center (BBTC). The speed can be adjusted via the speed
adjustment button (pic. 1.3). The retraction stop mode
allows the operator to slowly approach the required ben-
ding radius.
8.4 Cutting
A cutting cycle is usually performed in the normal mode,
which means that the cutting cycle is terminated automa-
tically after the max. operating pressure is reached or ter-
minated manually when the cable is cut.
8.5 Crimping
When crimping cable lugs and connectors the retraction
mode allows a better positioning or clamping function
which assists in producing perfect crimps. Actuating the
safety foot switch respectively the two hand safety con-
trol starts the crimping cycle. In the retraction mode when
releasing the safety foot switch or two hand control the
piston remains in its position and does not retract.
Attention
In case of an handling error the piston can be re-
tracted by a very brief actuation or by stepping
down the actuator of the safety foot switch also
in the retraction mode.
The crimping cycle continues when actuating the safety
foot switch again from the very position in which it was
interrupted. The crimping cycle runs automatically and
does not switch off before the max. operating pressure
is reached. In the retraction mode the retraction of the
piston can be stopped by actuating the foot switch.
Attention
The working process can be interrupted at any
moment by releasing or stepping down the ac-
tuator of the safety foot switch.
Once the three step safety foot switch has been stepped
down, it can only be reactivated by pushing the reset but-
ton of the foot switch. This reset button (pic. 1.10) is loca-
ted on the top of the foot switch.
Attention
Before changing the dies, respectively
blades of the tools attached to the pump
unit switch off the power to avoid uninten-
ded operation.
4.2 Explanation of the application range
The electro-hydraulic pump unit type EHP4 can be con-
nected to all punching, crimping and cutting heads, res-
pectively with all remote heads, of our product range.
Attention
Do not punch, crimp on or cut or operate
this unit on live lines.
Before starting to work on electric lines the user must
make sure that none of the parts in the working area of
the operator is live.
The units are not designed for continued operation. After
approximately 100 crimps respectively 80-50 cuts conse-
cutively a short break of at least 15 minutes is necessary
to let the unit cool down.
Attention
Too intensive use can cause heat damages to
the tool
Attention
During the operation of electric engines sparks
can occur which might ignite highly infl ammab-
le or explosive liquids and materials
Attention
Electro-hydraulic crimping/cutting tools should
not be operated in pouring rain or under water.
The unit can be operated in a temperature range from
-20°C to +40°C indoors and outdoors.
Before connecting the device to the public mains network
supply, the local power distribution supplier need to be
informed.
4.3 Service and maintenance instruction
The electro-hydraulic unit must be cleaned and dried after
each use. The pump is basically maintenance free, only
the oil level must be checked regularly and the pump has
to be inspected for possible damages and wear.
The EHP4 is equipped with an oil level control glass (pic.
1.5) which enables the operator the check the oil level of
the pump.
The oil level should be 10 mm below the top of the control
glass. If the oil level is too low please
fi
ll up the oil ac-
cordingly.
The following hydraulic oils are suitable for a temperature
range -20°C to +40°C:
Hydraulic oils based on Ester:
Rivolta S.B.H. 11, Shell
Naturell HF-E 15
Mineral oils:
Shell Tellus T 15, AVIA HVI 15, Mobil DTE 11,
NUTO H 15, Rando HD - Z15, Agip OSO 15, BP Energol
HLP 15.
Other equivalent hydraulic oils can also be used.The hy-
draulic hose (pic. 1.9) and the armature must be checked
for damage and leakage.
4.4 Oil changing and maintenance cycles
It is advisable to have the pump serviced by a specialist
during regular intervals to safeguard a technically proper
state before use.
Table 2 - Service schedule
What
When
Who
Cleaning
after each use Service personnel
Check oil level weekly
Service personnel
Check high
pressure hose
weekly
Specialist
Proper state
quarterly
Electric specialist
Change
hydraulic oil
annually
Manufacturer/
Specialist