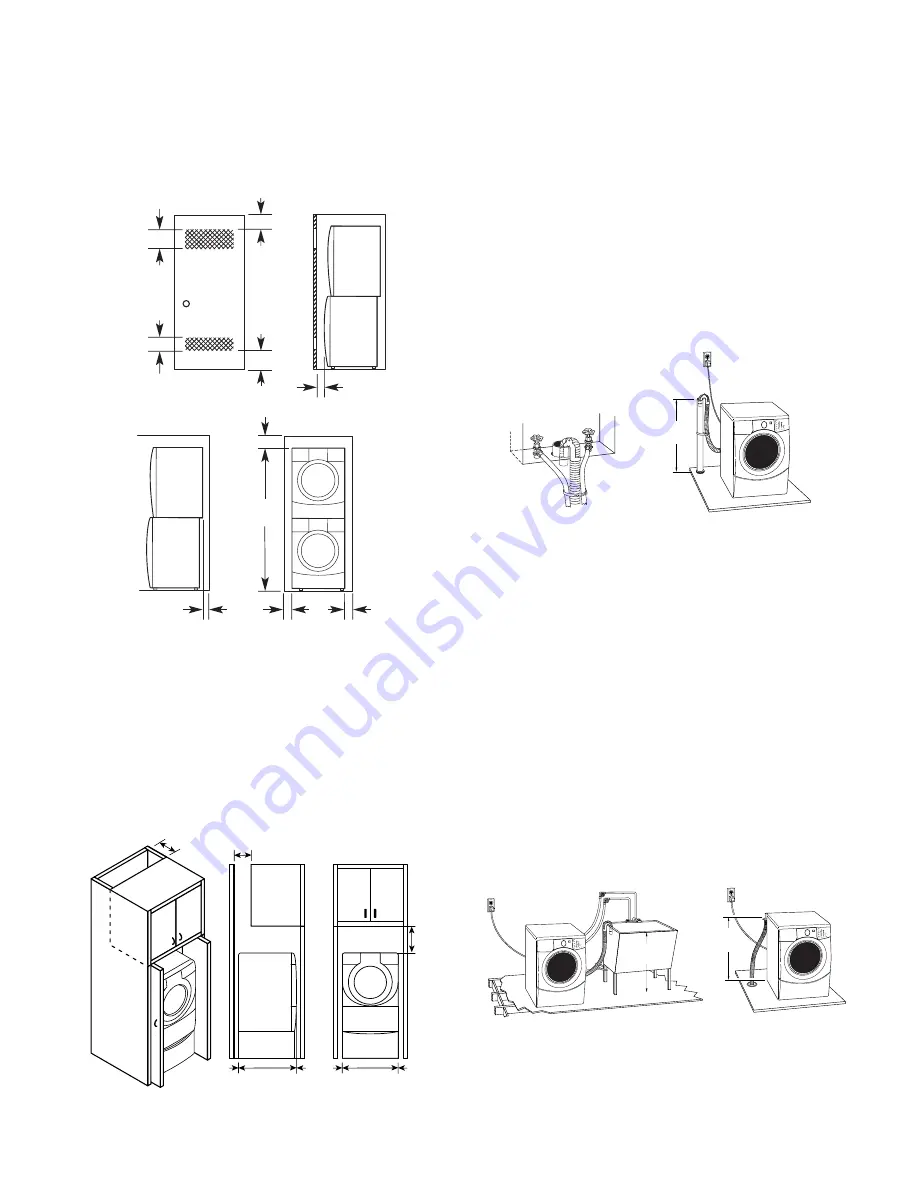
2-3
Recessed Or Closet Installation—
With Stacked Washer & Dryer
The dimensions shown are for the recom-
mended spacing.
* Min. top and bottom air openings for closet door.
** External exhaust elbow requires additional space.
*** Wall, door and floor molding may require
additional spacing.
48 in.
2
*
(310 cm
2
)
3" (7.6 cm)
6" (15.2 cm)
76"
(193 cm)
27"
(68.6 cm)
3" (7.6 cm)
1" (2.5 cm)
5-1/2"**
(14 cm)
1"***
(2.5 cm)
1"***
(2.5 cm)
24 in.
2
*
(155 cm
2
)
Cabinet Installation
The dimensions shown are for the recom-
mended spacing. For cabinet installation with
a door, the minimum ventilation openings in
the top are required.
7" (17.8 cm)
9"
(22.9 cm)
7" (17.8 cm)
4"
(10.2 cm)
31-1/2"
(80.0 cm)
27"
(68.6 cm)
1"
(2.5 cm)
1"
(2.5 cm)
1"
(2.5 cm)
30" min.
(76.2 cm)
1
2
30" min.
(76.2 cm)
28" min.
(71 cm)
1
2
DRAIN SYSTEM
The washer can be installed using the standpipe
drain system (floor or wall), the laundry tub
drain system, or the floor drain system. Select
the drain hose installation method you need
(see “Alternate Parts”).
Standpipe Drain System—
Wall Or Floor (View 1 & 2)
The standpipe drain requires a minimum diam-
eter standpipe of 2
″
(5 cm). The minimum
carry-away capacity can be no less than 17 gal
(64 L) per minute.
The top of the standpipe must be at least 30
″
(76.2 cm) high and no higher than 96
″
(2.4 m)
from the bottom of the washer.
Laundry Tub Drain System (View 1)
The laundry tub needs a minimum 20 gal.
(76 L) capacity. The top of the laundry tub must
be at least 30
″
(76.2 cm) above the floor.
Floor Drain System (View 2)
The floor drain system requires a siphon break
that may be purchased separately (see “Alter-
nate Parts ”).
The siphon break must be a minimum of 28
″
(71 cm) from the bottom of the washer. Addi-
tional hoses might be needed.
Содержание KHWS01PMT / WH
Страница 1: ...TECHNICAL EDUCATION JOB AID 4317352 KAL 4 FRONT LOADING AUTOMATIC WASHER MODEL KHWS01PMT WH ...
Страница 18: ...2 10 NOTES ...
Страница 30: ...3 12 NOTES ...
Страница 60: ...4 30 NOTES ...
Страница 80: ...6 14 NOTES ...
Страница 81: ...7 1 WIRING DIAGRAM ...
Страница 82: ...7 2 NOTES ...
Страница 84: ...8 2 NOTES ...
Страница 86: ......