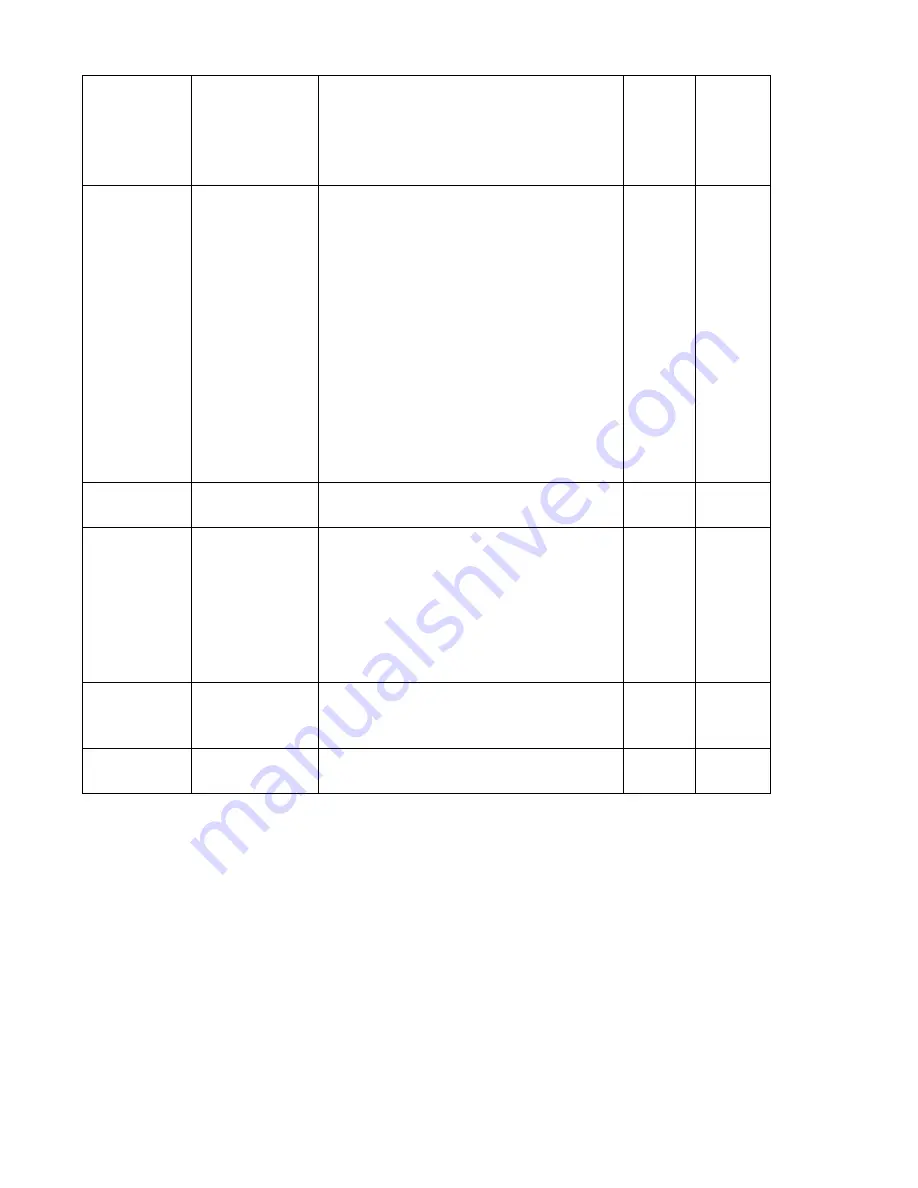
91
11. All input signals are ignored during
auto tuning. The variable is automatically
changed to 0 after auto tuning is completed.
Sets the variable to other values to end auto
tuning.
d0.04
Vc_Loop_BW
Sets the bandwidth of the velocity loop in
Hz. The variable can only be set after auto
tuning is performed properly; otherwise the
actual bandwidth goes wrong, which causes
abnormal working of the driver. If the auto
tuning result is abnormal, setting this
parameter may also cause abnormal
working of the driver.
Note: This parameter cannot be applied
when auto tuning is unavailable.
0
0~600
d2.17
K_Load
Indicates loading parameters
/
20~1500
0
d2.21
Sine_Amplitude
Proper increase in this data will reduce the
tuning error, but machine vibration will
become severer. This data can be adjusted
properly according to actual conditions of
machines. If the data is too small, the auto
tuning error becomes greater, or even
causes a mistake
64
0~1000
d2.22
Tuning_Scale
It is helpful to reduce the auto tuning time by
reducing the data, but the result may be
unstable.
128
0~16384
d2.23
Tuning_Filter
Indicates
filter
parameters
during
auto-tuning
64
1~1000
Auto tuning is a process where the suitable and stable K_Load value is automatically calculated. In the auto
tuning mode, the data of numeric display is automatically switched to the real-time display mode of K_Load
data. When K_Load data gradually becomes stable, the driver automatically adjusts Kvp and Kvi data of a
velocity loop, so that the actual bandwidth of the velocity loop is 50Hz. When K_Load data becomes stable,
the driver automatically stops auto tuning operation; then you need to customize Vc_Loop_BW, representing
the desired bandwidth of the velocity ring. Finally, run the test system in the actual environment, and save the
parameters.
Precautions:
1. Auto tuning applies when both forward rotation and reverse rotation of a motor are allowable, and the
loadings do not change much during the operation. When forward rotation or reverse rotation of the
motor is not allowable on a device, it is recommended to adjust the parameters manually.
2. During auto tuning operation, pulse signals, digital input signals, and analog signals of the external
controller are temporarily unavailable, so safety must be ensured.
3. Before auto tuning operation, it is recommended to properly adjust the Kvp, Kvi and Speed_Fb_N (a
Содержание CD420
Страница 8: ...8 1 3 3 Power Brake and Encoder cable of Motors...
Страница 16: ...16 3 4 Power Interfaces CD420 X2 CD430 CD620 X2 and X5 of CD Driver Fig 3 4 Power interfaces of a CD driver...
Страница 22: ...22 Fig 4 3 Separate regulation of bits...
Страница 78: ...78...
Страница 99: ...99 Chapter 11 Specification 11 1 Servo Drivers and Motors Selection Table...
Страница 100: ...100 11 2 Servo Driver 11 2 1 Technical Specification Table for Servo Driver...
Страница 101: ...101 11 2 2 Mechanical Dimension Diagram for Servo Driver...
Страница 102: ...102 11 3 Dimensions Torque Curve Technical Specifications of Servo Motors 11 3 1 SMH60 Servo Motor...
Страница 103: ...103 11 3 2 SMH80 Servo Motor...
Страница 104: ...104 11 3 3 SMH110 Servo Motor 1 Technical Specification Table...
Страница 105: ...105 2 Dimension Torque Curve...
Страница 106: ...106 11 4 Wiring Diagram for Servo Motor Cable 11 4 1 Wiring Diagram for the Power Cable...
Страница 107: ...107 11 4 2 Wiring Diagram for the Encoder Cable...