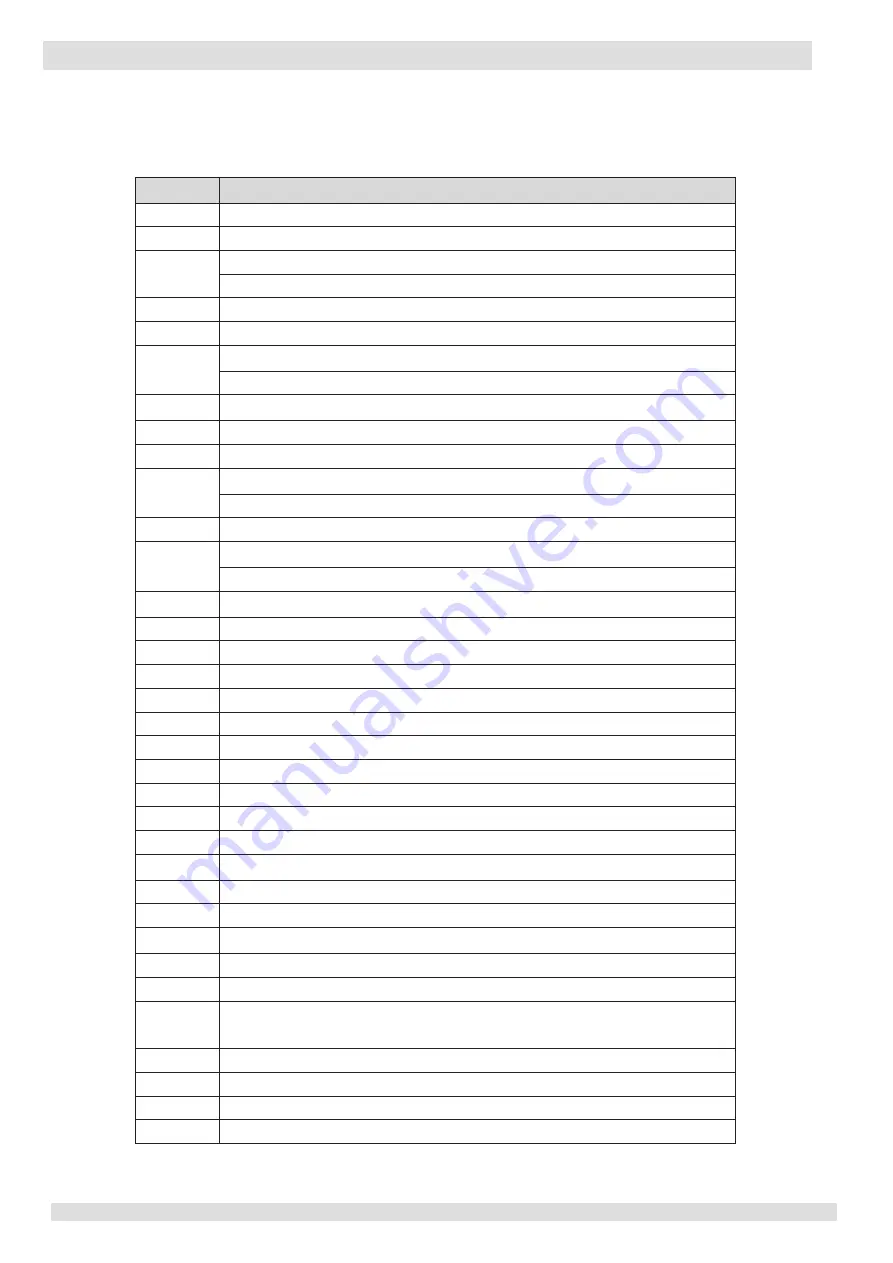
DC Inverter Chiller
70
8
Appendix
8.1
Error Code Table
Table 3-8.1: Error code table of KEM-30 DRS4, KEM-30 DRS4 KH, KEM-60 DRS4 and KEM-60 DRS4 KH
Error cod
e
Content
E0
Main control parameter memory EEPROM failure
E1
Phase sequence failure of main control board check
E2
Communication failure between master and the HMI
Communication failure between master and the slave
E3
Total water outlet temperature sensor (Tw) failure (displayed on master unit only)
E4
Unit water outlet temperature sensor (Two) failure
E5
1E5 condenser tube temperature sensor T3A failur
e
2E5 condenser tube temperature sensor T3B failure
E7
Ambient temperature sensor (T4) failur
e
E8
Power supply phase sequence protector output error
E9
Water flow detection failure
Eb
1Eb --> Taf1 cooling evaporator low-temperature anti-freeze protection sensor failu
re
2Eb --> Taf2 cooling evaporator low-temperature anti-freeze protection sensor failure
EC
Slave unit module reduction
Ed
1Ed --> A system discharge temperature sensor failur
e
2Ed --> B system discharge temperature sensor failure
EF
Unit water return temperature sensor (Twi) failur
e
EH
System self-check failure alarm
EP
Discharge temperature sensor failure alarm
EU
Tz/7 Coil final outlet temperature sensor error
P0
System high-pressure protection or discharge temperature protection
P1
System low pressure protection
P2
Tz/7 Coil final outlet temperature too high
P3
T4 ambient temperature too high in cooling mode
P4
System A current protection
P5
System B current protection
P6
Inverter module failure
P
7
High temperature protection of system condenser
P9
Water inlet and outlet temperature difference protection
Pb
Antifreeze protection in winter
P
C
Evaporator pressure too low in cooling
PE
Cooling evaporator low temperature antifreeze protection
PH
T4 ambient temperature too high in heatling mode
PL
Inverter module temperature Tfin too high
temperature protection
xPU
DC fan module protection
H5
Voltage too high or too low
xH9
Compressor inverter module is not matched
xHE
Not insert electronic expansion valve error
Table continued on next page …