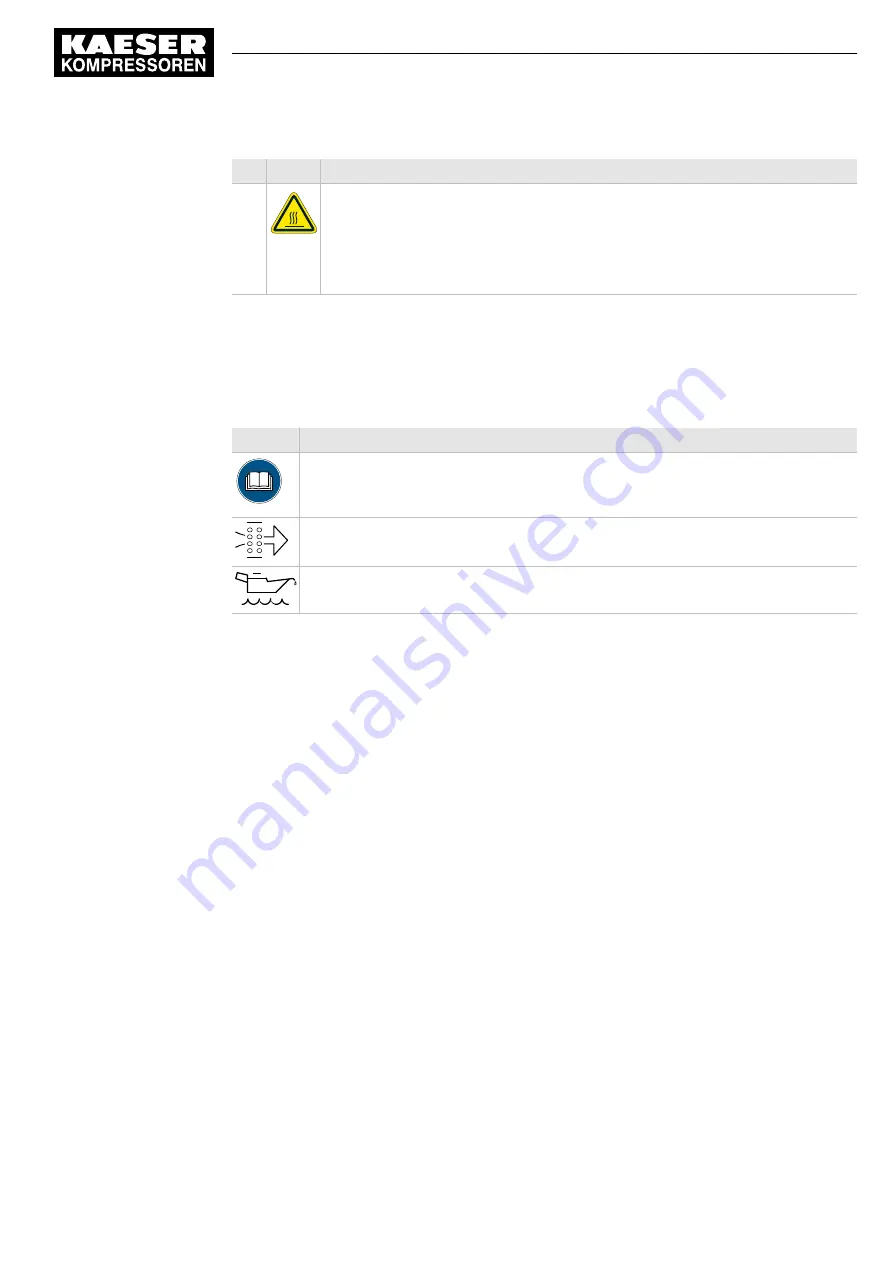
Item Sign
Meaning
2
Hot surface!
Risk of burns caused by contact with hot components
➤ Do not touch the surface.
➤ Wear long-sleeved garments (not synthetics such as polyester) and protective
gloves.
Tab. 28 Safety Signs
3.9 Information signs
The table lists the various information signs used and their meanings.
Sign
Meaning
Personal injury or damage to the machine by incorrect operation!
➤ Read and understand the service manual and all safety signs before switching on
this machine.
Maintain the air filter regularly.
Check the oil level regularly and change the oil at the correct intervals.
Tab. 29 Information signs
3.10 In emergency
3.10.1 Correct fire fighting
Suitable measures
Calm and prudent action can safe lives in the event of a fire.
➤ Keep calm.
➤ Give the alarm.
➤ Shut off supply lines if possible.
Power supply disconnecting device (all phases)
Cooling water (if present)
➤ Warn and move endangered personnel to safety.
➤ Help incapacitated persons.
➤ Close the doors.
➤ When trained accordingly: Attempt to extinguish the fire.
3
Safety and Responsibility
3.9
Information signs
No.: 9_5753 24 E
Assembly and operating manual 2-stage piston compressor
EPC-2-G
23
Содержание EPC 150-2-G
Страница 2: ...KKW PEPC 2 04 en SBA KOLBEN AGGREGAT 2 STUFIG 20170303 120300...
Страница 6: ...Contents iv Assembly and operating manual 2 stage piston compressor EPC 2 G No 9_5753 24 E...
Страница 10: ...List of Tables viii Assembly and operating manual 2 stage piston compressor EPC 2 G No 9_5753 24 E...
Страница 100: ...13 Annex 13 2 Dimensional Drawing 90 Assembly and operating manual 2 stage piston compressor EPC 2 G No 9_5753 24 E...