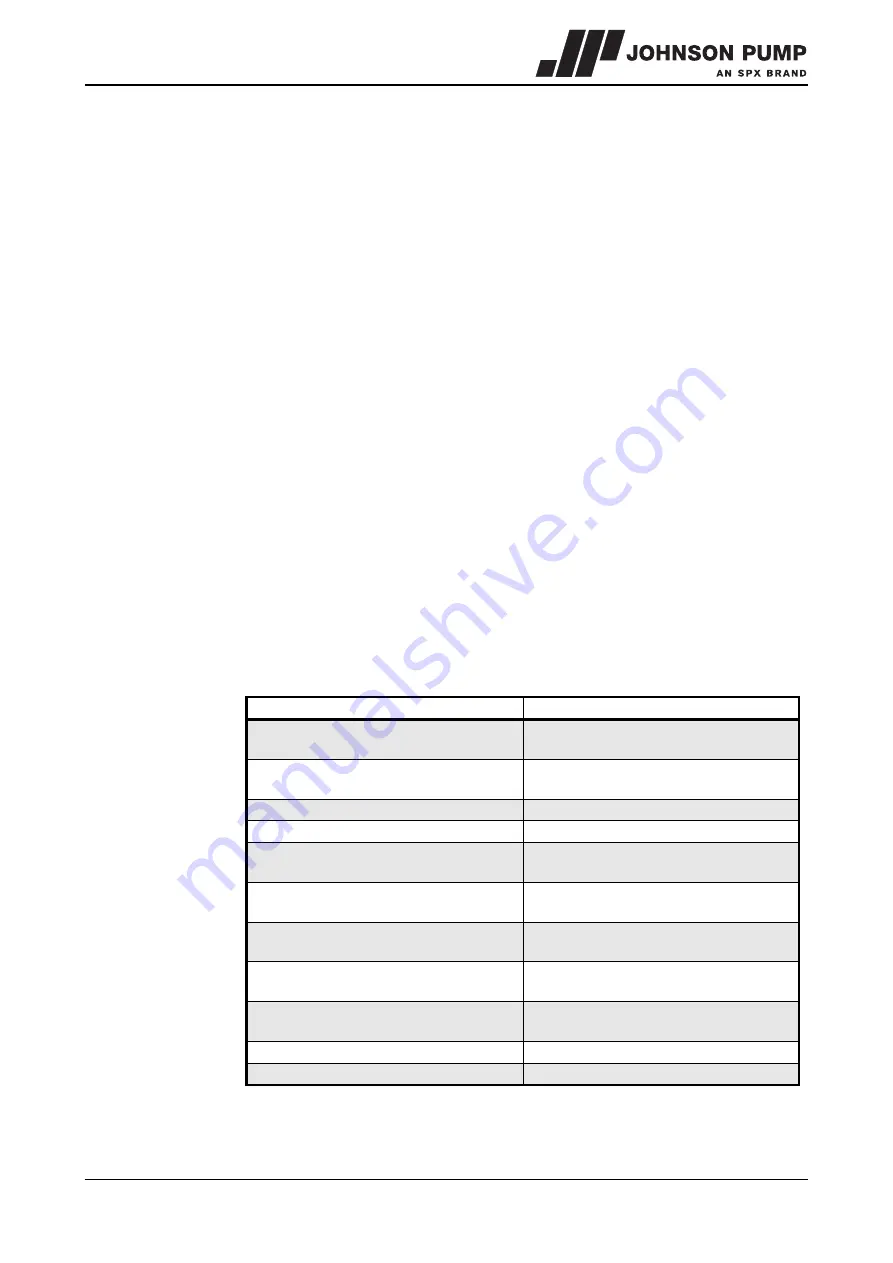
MCHZ/EN (0912) 4.2
Problem solving
25
MCHZ
6 Problem solving
Faults in a pump installation can have various causes. The fault may not be in the pump, it
may also be caused by the pipe system or the operating conditions. Firstly, always check
that installation has been executed in accordance with the instructions in this manual and
that the operating conditions still correspond with the specifications for which the pump
was purchased.
In general, breakdowns in a pump installation are attributable to the following causes:
• Faults with the pump.
• Breakdowns or faults in the pipe system.
• Faults due to incorrect installation or commissioning.
• Faults due to incorrect choice of pump.
A number of the most frequently occurring failures as well as their possible causes are
shown in the table below.
Table 2: Most frequently occurring failures.
Most common faults
Possible causes, see Table 3.
Pump delivers no liquid
1 2 3 4 5 8 9 10 11 13 14 17 19 20 21
29
Pump has insufficient volume flow
1 2 3 4 5 8 9 10 11 13 14 15 17 19 20
21 28 29
Pump has insufficient head
2 4 5 13 14 17 19 28 29
Pump stops after start up
1 2 3 4 5 8 9 10 11
Pump has higher power consumption than
normal
12 15 16 17 18 22 23 24 25 26 27 32
34 38 39
Pump has lower power consumption than
normal
13 14 15 16 17 18 20 21 28 29
The stuffing box packing is leaking
excessively
23 25 26 30 31 32 33 43
Packing rings or mechanical seal have to
be replaced to often
23 25 26 30 32 33 34 41
Pump vibrates or is noisy
1 9 10 11 15 18 19 20 22 23 24 25 26
27 29 37 38 39 40
Bearings wear too much or become hot
23 24 25 26 27 37 38 39 40 42
Pump running rough hot or seizes
23 24 25 26 27 34 37 38 39 40 42
Содержание MCHC
Страница 5: ...4 MCHZ EN 0912 4 2 ...
Страница 48: ...MCHZ EN 0912 4 2 Dimensions 47 MCHZ 8 Dimensions ...
Страница 59: ...58 Dimensions MCHZ EN 0912 4 2 ...
Страница 61: ...60 Parts MCHZ EN 0808 4 1 9 3 MCHZ 12 5 14a b 16 Figure 27 MCHZ 12 5 14a b 16 ...
Страница 63: ...62 Parts MCHZ EN 0808 4 1 9 4 MCHZS 12 5 14a b 16 Figure 28 MCHZS 12 5 14a b 16 ...
Страница 70: ...MCHZ EN 0808 4 1 Parts 69 MCHZ 9 7 MCHZ 20a b Figure 31 MCHZ 20 a b ...
Страница 72: ...MCHZ EN 0808 4 1 Parts 71 MCHZ 9 8 MCHZS 20a b Figure 32 MCHZS 20 a b ...
Страница 81: ...80 Technical data MCHZ EN 0912 4 2 ...
Страница 85: ...84 ORDFORM 0804 3 1 EN ...