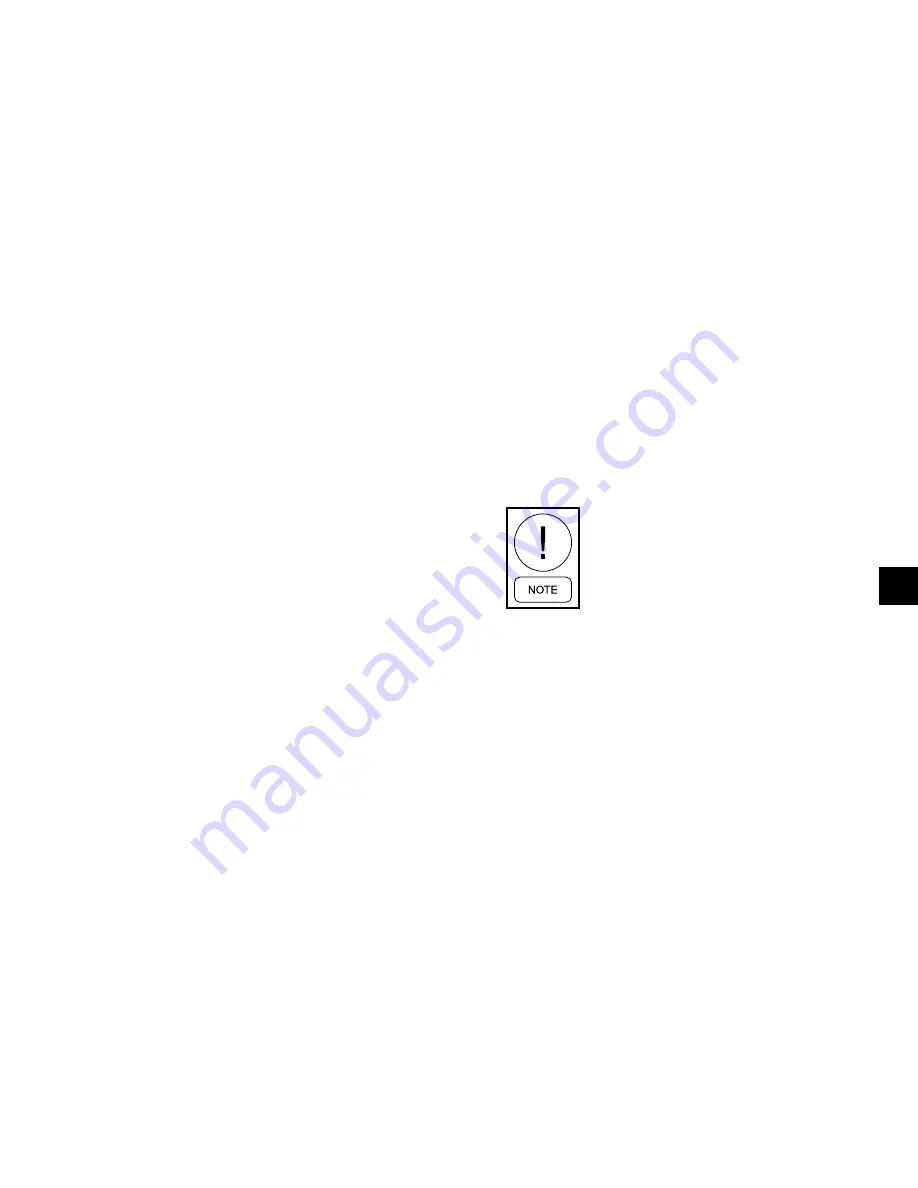
JOHNSON CONTROLS
35
FORM 155.17-N1
ISSUE DATE: 4/1/2013
10
SECTION 10 – STEAM CONDENSATE RETURN SYSTEM
Steam condensate return systems should be designed
in accordance with good engineering practice for the
gen er al purpose of removing condensate from the ab-
sorp tion unit’s generator and returning it to the boiler.
Al ways pitch the condensate piping to prevent liquid
ham mer ing.
The typical condensate leaving temperature when the
absorption unit is running at full load is 180°F (82.2°C)
at ap prox i mate ly 15.0 PSIG (204.77 kPa) as measured
immediately downstream of the drain solenoid valve.
Refer to the Typical Piping Schematic (
) for a brief de scrip tion of each component,
starting at the unit’s condensate drain cooler.
STEAM CONDENSATE DRAIN COOLER
The condensate drain cooler(s) are installed on the unit
by the factory. It ef fec tive ly elim i nates the need for an
additional condensate cooler or a steam trap.
CONDENSATE FLOW SETTING VALVE
This is a needle valve that is supplied, installed, and
set by the factory. It is set to allow the correct amount
of steam condensate flow through the valve at full load
conditions. Only a skilled and certified JOHNSON
CONTROLS Service Technician should adjust this
valve during unit start-up.
STEAM CONDENSATE DRAIN SOLENOID
VALVE
This NC valve is also supplied and installed by the
factory. It is used to insure zero steam flow through
the generator shell when the unit is shut down. This
valve works in con junc tion with the Automatic Shut-
Off Valve at the steam inlet.
FLANGE ADAPTER (SPOOL PIECE)
This customer-supplied adapt er must be installed at
the outlet condensate flange of the unit. A flow me-
ter will be temporarily installed at this lo ca tion dur ing
start-up to fine-tune the condensate flow setting valve.
CONDENSATE OUTLET PRESSURE
INDICATOR
(Customer supplied) The pres sure immediately before
the Con den sate Back-Pressure Valve must be read at
this lo ca tion.
ADJUSTABLE CONDENSATE BACK-
PRESSURE VALVE
This must be a cus tom er-supplied globe or similar type
valve. It is installed downstream of the pressure indi-
cator and used to adjust the condensate back-pressure
during start-up. YORK designs all the steam-fired ab-
sorption units around a 15 PSIG (204.77 kPa) back-
pressure rating for conformity. Therefore, when the
unit is run ning full load, the con den sate back-pres-
sure must be set at 15 PSIG (204.77 kPa) to insure the
steam flow through the first stage gen er a tor is cor rect
to design con di tions.
Dimension H
2
on the Steam Piping
Sche mat ic (
) is a
max i mum of 33 feet (10 meters). This is
the max i mum height of piping to pre vent
ex ces sive back-pressure to the con den sate
drain cooler.
When designing and installing the steam con den sate
pip ing, the condensate system pressure drop down-
stream of the con den sate back-pressure valve must be
equal to or lower than 15 PSIG (204.77 kPa). If not,
this required setting will not be achievable and not
enough steam will flow through the high-temperature
generator for unit full load capacity.
The following formula must be used when designing
the steam condensate piping:
∆ P H2 + ∆ P Piping + ∆ P Valve = 15.0 PSIG
Where:
∆
P
H2 = Pressure drop due to height, H2.
∆
P
Piping = Pressure drop due to condensate piping,
elbows, bends, etc...
∆
P
Valve = Pressure drop due to condensate system
backpressure valve.
Содержание YORK YPC Series
Страница 10: ...JOHNSON CONTROLS 10 FORM 155 17 N1 ISSUE DATE 4 1 2013 THIS PAGE INTENTIONALLY LEFT BLANK ...
Страница 18: ...JOHNSON CONTROLS 18 FORM 155 17 N1 ISSUE DATE 4 1 2013 THIS PAGE INTENTIONALLY LEFT BLANK ...
Страница 20: ...JOHNSON CONTROLS 20 FORM 155 17 N1 ISSUE DATE 4 1 2013 THIS PAGE INTENTIONALLY LEFT BLANK ...
Страница 28: ...JOHNSON CONTROLS 28 FORM 155 17 N1 ISSUE DATE 4 1 2013 THIS PAGE INTENTIONALLY LEFT BLANK ...
Страница 30: ...JOHNSON CONTROLS 30 FORM 155 17 N1 ISSUE DATE 4 1 2013 THIS PAGE INTENTIONALLY LEFT BLANK ...
Страница 34: ...JOHNSON CONTROLS 34 FORM 155 17 N1 ISSUE DATE 4 1 2013 THIS PAGE INTENTIONALLY LEFT BLANK ...
Страница 36: ...JOHNSON CONTROLS 36 FORM 155 17 N1 ISSUE DATE 4 1 2013 THIS PAGE INTENTIONALLY LEFT BLANK ...
Страница 38: ...JOHNSON CONTROLS 38 FORM 155 17 N1 ISSUE DATE 4 1 2013 THIS PAGE INTENTIONALLY LEFT BLANK ...
Страница 46: ...JOHNSON CONTROLS 46 FORM 155 17 N1 ISSUE DATE 4 1 2013 THIS PAGE INTENTIONALLY LEFT BLANK ...
Страница 50: ...JOHNSON CONTROLS 50 FORM 155 17 N1 ISSUE DATE 4 1 2013 THIS PAGE INTENTIONALLY LEFT BLANK ...
Страница 52: ...JOHNSON CONTROLS 52 FORM 155 17 N1 ISSUE DATE 4 1 2013 THIS PAGE INTENTIONALLY LEFT BLANK ...
Страница 54: ...JOHNSON CONTROLS 54 FORM 155 17 N1 ISSUE DATE 4 1 2013 THIS PAGE INTENTIONALLY LEFT BLANK ...
Страница 58: ...JOHNSON CONTROLS 58 FORM 155 17 N1 ISSUE DATE 4 1 2013 THIS PAGE INTENTIONALLY LEFT BLANK ...
Страница 62: ...JOHNSON CONTROLS 62 FORM 155 17 N1 ISSUE DATE 4 1 2013 THIS PAGE INTENTIONALLY LEFT BLANK ...
Страница 64: ...JOHNSON CONTROLS 64 FORM 155 17 N1 ISSUE DATE 4 1 2013 THIS PAGE INTENTIONALLY LEFT BLANK ...
Страница 70: ...JOHNSON CONTROLS 70 FORM 155 17 N1 ISSUE DATE 4 1 2013 THIS PAGE INTENTIONALLY LEFT BLANK ...
Страница 78: ...JOHNSON CONTROLS 78 FORM 155 17 N1 ISSUE DATE 4 1 2013 THIS PAGE INTENTIONALLY LEFT BLANK ...
Страница 80: ...JOHNSON CONTROLS 80 FORM 155 17 N1 ISSUE DATE 4 1 2013 THIS PAGE INTENTIONALLY LEFT BLANK ...
Страница 84: ...JOHNSON CONTROLS 84 FORM 155 17 N1 ISSUE DATE 4 1 2013 THIS PAGE INTENTIONALLY LEFT BLANK ...
Страница 93: ...JOHNSON CONTROLS 93 Appendix A Tables A FORM 155 17 N1 ISSUE DATE 4 1 2013 ...
Страница 94: ...JOHNSON CONTROLS 94 FORM 155 17 N1 ISSUE DATE 4 1 2013 THIS PAGE INTENTIONALLY LEFT BLANK ...
Страница 98: ...JOHNSON CONTROLS 98 FORM 155 17 N1 ISSUE DATE 4 1 2013 THIS PAGE INTENTIONALLY LEFT BLANK ...
Страница 113: ...JOHNSON CONTROLS 113 Appendix C Insulation Illustrations C FORM 155 17 N1 ISSUE DATE 4 1 2013 NOTES ...