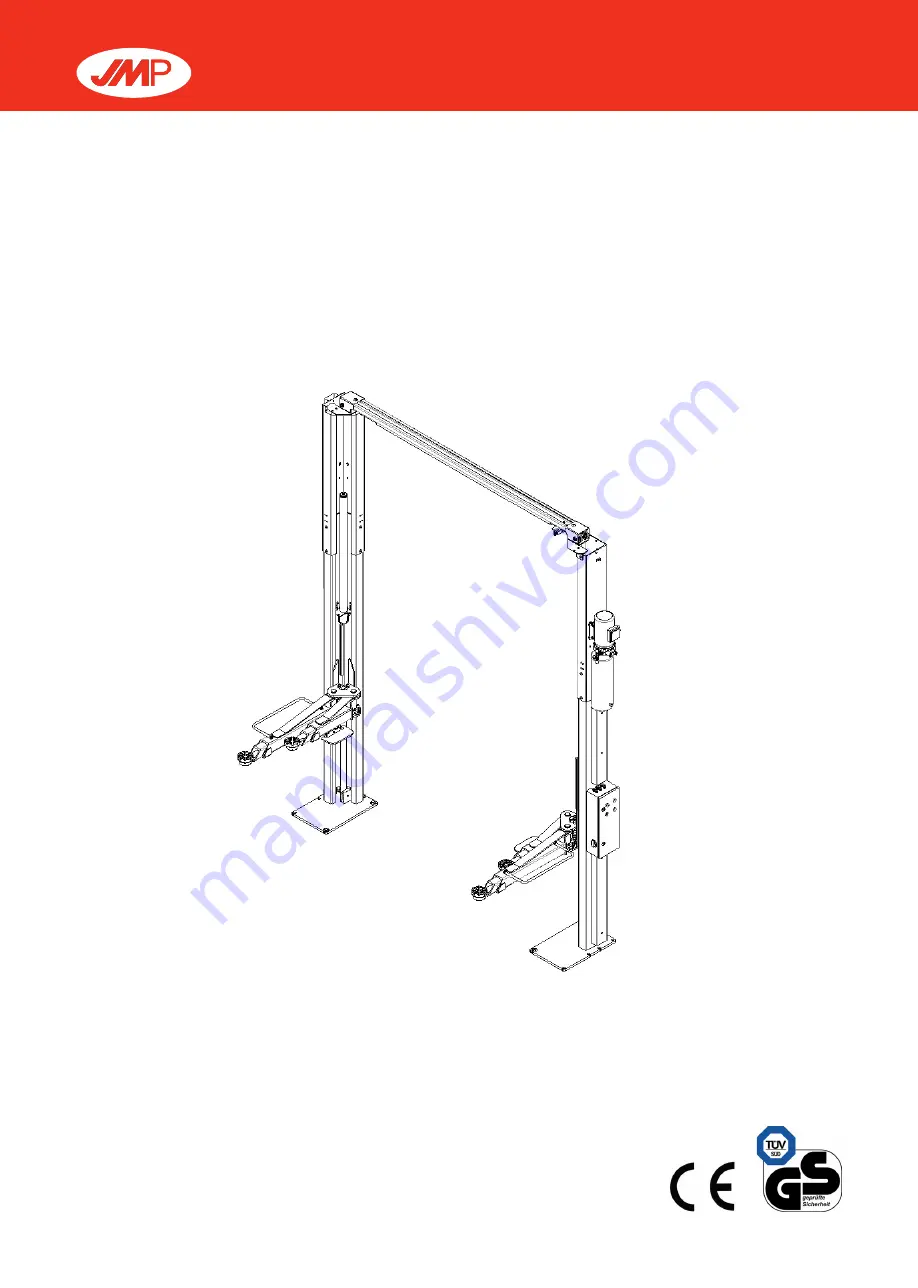
Vehicle Lift „JMP FOX 4000 H“
From cars to vans with medium wheelbase up to 4 tonnes total weight.
Lift status: 21.04.2016, as of serial number 2017-06-1495
Status of operating instructions: 27.02.2018
Revision number: 4
JM-No. 674 00 71
Operation instructions and inspection logbook
Serial number:__________________
Johannes J. Matthies GmbH & Co. KG
Hammerbrookstr. 97
20097 Hamburg
Web: www.matthies.de
Email: [email protected]
Содержание FOX 4000 H
Страница 11: ...9 6 3 Data sheets a Standard version with 4090 mm ...
Страница 12: ...10 b Lift column extension version with 4690 mm ...
Страница 13: ...11 6 4 Load distribution ...
Страница 14: ...12 6 5 Foundation plan ...
Страница 15: ...13 6 6 Electrical diagram and parts list ...
Страница 16: ...14 6 7 Hydraulic diagram and hydraulic parts list ...
Страница 32: ...30 12 7 Installation of covers pipe clips and hydraulic line ...
Страница 33: ...31 ...
Страница 34: ...32 Ensure that hydraulic hoses F G and I are firmly connected and no leaks are evident ...
Страница 37: ...35 12 10 Installation of limit switch ...
Страница 41: ...39 B Safety catch A Cable from control cabinet B Safety catch cable ...
Страница 42: ...40 C Shut off bar C Cable from control cabinet D Safety catch cable ...
Страница 43: ...41 D Limit switch A Cable contact for shut off bar B Crossbar C Connector D Cable gland Clamp 102 Clamp 104 ...
Страница 44: ...42 E Pump unit A Limit switch cable B Column extension cable bushing ...
Страница 45: ...43 A Limit switch cable C Cable sleeve Clamp 102 Clamp 111 ...
Страница 46: ...44 12 13 Filling and venting of hydraulic system Grounding Connection 400 V U1 U2 U3 Clamp 200 Clamp 201 ...
Страница 49: ...47 12 16 Dowel data sheet ...
Страница 62: ...60 16 CE Confirmation ...