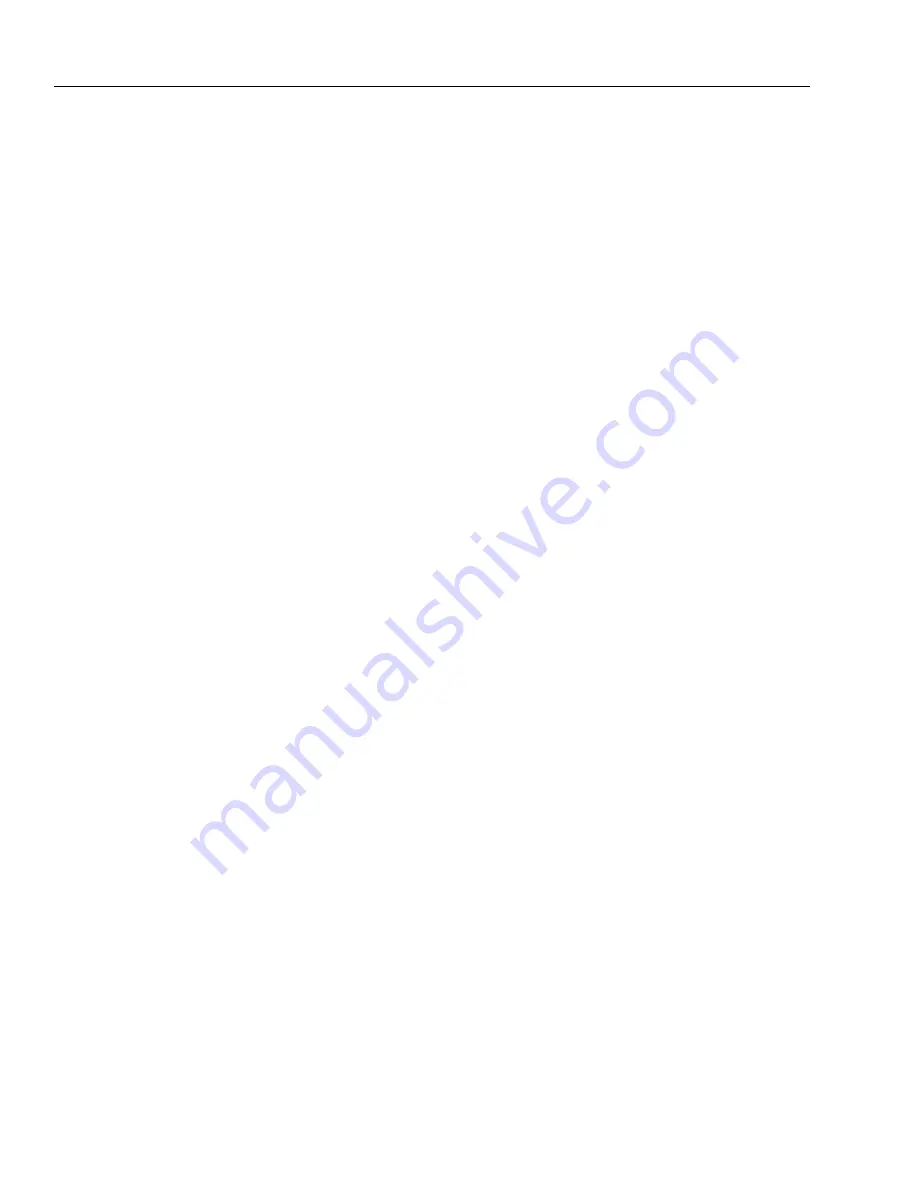
SECTION 3 - CHASSIS & TURNTABLE
3-156
– JLG Lift –
3121160
Minimum Pressure Valve/Check Valve
Assembly
This combined valve located in the filter support housing
has two functions.
The Minimum Pressure Valve - will maintain a pressure of
approximately 65
psig (4.5 bar) in the compressor unit to
ensure oil injection during load conditions and also to
maintain effective oil separation. Once this internal pres-
sure
is exceeded it will allow air to discharge downstream
to the service outlet.
The Discharge Check Valve - prevents air in service lines
or downstream receiver from venting down through the
compressor during unload (when the compressor auto-
matically will unload to approximately 40 psig [2.75 bar]
internally) and also during shutdown.
Hydraulic Drive System
Scope of supply may vary depending upon customer
specifications.
Hydraulic pump, oil reservoir, return line oil filter and
hoses to and from the completed packaged compressor
are not furnished with the compressor. This is customer
responsibility.
The packaged compressor unit will normally contain the
hydraulic motor, hydraulic pressure relief valve, and on/off
solenoid valve.
Input hydraulic oil pressure feed is connected to the bulk-
head provided on the compressor package. Within the
package the high pressure oil feeds to a manifold contain-
ing the pressure relief valve and directional solenoid valve.
If a malfunction in the hydraulic motor/compressor assem-
bly causes the hydraulic pressure to rise it will bypass to
the return line to safeguard damage or potential injury.
The directional solenoid valve is normally activated by the
on/off selector switch mounted in the instrument cluster
on the package, this valve is also connected through the
compressor safety circuits for over-temperature and over-
pressure, if either condition occurs it will shut the unit
down, by diverting oil back to tank. It is possible to add
remote on/off switch in parallel with the instrument cluster
to permit on/off operation from another location on the
vehicle.
Hydraulic oil from the manifold is hosed directly to the
hydraulic motor and the outlet from the motor passes to
the return line connection on the package. Customer to
provide both hydraulic feed and return lines.
The hydraulic motor powers the compressor through a
belt drive system.
Compressor Cooling System
The package contains a cooler assembly powered by a 12
volt D.C. electric fan. Oil from the compressor sump
passes through this cooler before being filtered for re-
injection into the compressor. A thermostatic fan tempera-
ture switch activates the fan to come on/off to maintain the
correct operating temperature for the compressor oil. This
switch will activate the fan to come on at approximately
185°F (85°C) and will switch off again at approximately
165°F (74°C). The purpose of maintaining an elevated
temperature during operation is to keep intake air mois-
ture in suspension as it passes through the compressor.
Thermal switch activation is affected by ambient condi-
tions, load/unload cycles (or low oil level).
Initial Startup
The following procedure should be used to make the
initial start-up of your compressor:
1.
Position the compressor on a level surface so that
the proper amounts of oil can be added if required.
2.
Unit should be bolted down, do not rely on hoses to
hold the module in position.
3.
Check all hose connections are tight and wiring con-
nections correct and tight.
4.
Check compressor oil level, top up if necessary.
5.
Switch instrument panel to OFF.
6.
Ensure hydraulic oil to pump inlet. (Prime if neces-
sary)
7.
Engage hydraulic system and allow hydraulic oil to
circulate back to tank. Check for leaks.
8.
Service valve on compressor closed.
9.
Switch the instrument panel switch to ON, this
should very quickly pass oil to the hydraulic motor
on the compressor and start producing air.
10.
Check pressure and temperature gauges. Pressure
switch may need adjustment to achieve desired
operating pressure.
11.
Partly open service valve to load compressor and
allow to warm up. Monitor temperature gauge, the
ideal operating temperature should be between
165°F and 190°F (74°C and 88°C) although it may be
higher in high ambient conditions.
12.
Cycle compressor on/off with service valve to ensure
operation is OK
13.
Close service valve then switch instrument switch to
OFF.
14.
Disengage hydraulic system.
Содержание 740A
Страница 1: ...Service and Maintenance Manual Models 740A 740AJ P N 3121160 January 8 2013 ...
Страница 2: ......
Страница 20: ...xviii JLG Lift 3121160 LIST OF TABLES TABLE NO TITLE PAGE NO This page left blank intentionally ...
Страница 35: ...SECTION 1 SPECIFICATIONS 3121160 JLG Lift 1 15 Figure 1 4 Torque Chart SAE Fasteners Sheet 1 of 3 ...
Страница 36: ...SECTION 1 SPECIFICATIONS 1 16 JLG Lift 3121160 Figure 1 5 Torque Chart SAE Fasteners Sheet 2 of 3 ...
Страница 37: ...SECTION 1 SPECIFICATIONS 3121160 JLG Lift 1 17 Figure 1 6 Torque Chart SAE Fasteners Sheet 3 of 3 ...
Страница 38: ...SECTION 1 SPECIFICATIONS 1 18 JLG Lift 3121160 Figure 1 7 Torque Chart METRIC Fasteners Sheet 1 of 3 ...
Страница 39: ...SECTION 1 SPECIFICATIONS 3121160 JLG Lift 1 19 Figure 1 8 Torque Chart METRIC Fasteners Sheet 2 of 3 ...
Страница 40: ...SECTION 1 SPECIFICATIONS 1 20 JLG Lift 3121160 Figure 1 9 Torque Chart METRIC Fasteners Sheet 3 of 3 ...
Страница 50: ...SECTION 2 GENERAL 2 10 JLG Lift 3121160 Figure 2 2 Engine Operating Temperature Specifications Ford 4150548 E ...
Страница 51: ...SECTION 2 GENERAL 3121160 JLG Lift 2 11 Figure 2 3 Engine Operating Temperature Specifications GM 4150548 E ...
Страница 52: ...SECTION 2 GENERAL 2 12 JLG Lift 3121160 NOTES ...
Страница 109: ...SECTION 3 CHASSIS TURNTABLE 3121160 JLG Lift 3 57 Figure 3 39 Swing Hub ...
Страница 111: ...SECTION 3 CHASSIS TURNTABLE 3121160 JLG Lift 3 59 Figure 3 40 Swing Brake Assembly Ausco Prior to S N 0300068040 ...
Страница 123: ...SECTION 3 CHASSIS TURNTABLE 3121160 JLG Lift 3 71 Figure 3 43 Swing Drive Hub Fairfield S N 0300068040 to Present ...
Страница 135: ...SECTION 3 CHASSIS TURNTABLE 3121160 JLG Lift 3 83 Figure 3 48 Rotary Coupling Port Location ...
Страница 138: ...SECTION 3 CHASSIS TURNTABLE 3 86 JLG Lift 3121160 A B D D B C Figure 3 51 Auxiliary Pump Sheet 1 of 2 ...
Страница 153: ...SECTION 3 CHASSIS TURNTABLE 3121160 JLG Lift 3 101 Figure 3 54 EFI Component Location ...
Страница 156: ...SECTION 3 CHASSIS TURNTABLE 3 104 JLG Lift 3121160 Figure 3 55 ECM EPM Identification ECM EPM ...
Страница 167: ...SECTION 3 CHASSIS TURNTABLE 3121160 JLG Lift 3 115 Figure 3 59 Deutz EMR 2 Troubleshooting Flow Chart ...
Страница 168: ...SECTION 3 CHASSIS TURNTABLE 3 116 JLG Lift 3121160 Figure 3 60 Deutz EMR 2 Vehicle Side Connection Diagram ...
Страница 169: ...SECTION 3 CHASSIS TURNTABLE 3121160 JLG Lift 3 117 Figure 3 61 Deutz EMR 2 Engine Side Connection Diagram Sheet 1 of 2 ...
Страница 170: ...SECTION 3 CHASSIS TURNTABLE 3 118 JLG Lift 3121160 Figure 3 62 Deutz EMR 2 Engine Side Connection Diagram Sheet 2 of 2 ...
Страница 171: ...SECTION 3 CHASSIS TURNTABLE 3121160 JLG Lift 3 119 Figure 3 63 EMR 2 Engine Plug Pin Identification ...
Страница 172: ...SECTION 3 CHASSIS TURNTABLE 3 120 JLG Lift 3121160 Figure 3 64 EMR 2 Vehicle Plug Pin Identification ...
Страница 173: ...SECTION 3 CHASSIS TURNTABLE 3121160 JLG Lift 3 121 Figure 3 65 EMR2 Fault Codes Sheet 1 of 5 ...
Страница 174: ...SECTION 3 CHASSIS TURNTABLE 3 122 JLG Lift 3121160 Figure 3 66 EMR2 Fault Codes Sheet 2 of 5 ...
Страница 175: ...SECTION 3 CHASSIS TURNTABLE 3121160 JLG Lift 3 123 Figure 3 67 EMR2 Fault Codes Sheet 3 of 5 ...
Страница 176: ...SECTION 3 CHASSIS TURNTABLE 3 124 JLG Lift 3121160 Figure 3 68 EMR2 Fault Codes Sheet 4 of 5 ...
Страница 177: ...SECTION 3 CHASSIS TURNTABLE 3121160 JLG Lift 3 125 Figure 3 69 EMR2 Fault Codes Sheet 5 of 5 ...
Страница 236: ...SECTION 4 BOOM PLATFORM 4 20 JLG Lift 3121160 Figure 4 7 Boom Valve and Limit Switches Location 0271989 A ...
Страница 237: ...SECTION 4 BOOM PLATFORM 3121160 JLG Lift 4 21 Figure 4 8 Transportation Switch Installation CE Only 0258384 A ...
Страница 238: ...SECTION 4 BOOM PLATFORM 4 22 JLG Lift 3121160 Figure 4 9 Tower Power Track Installation Sheet 1 of 2 ...
Страница 239: ...SECTION 4 BOOM PLATFORM 3121160 JLG Lift 4 23 Figure 4 10 Tower Power Track Installation Sheet 2 of 2 ...
Страница 244: ...SECTION 4 BOOM PLATFORM 4 28 JLG Lift 3121160 Figure 4 14 Rotator Assembly HELAC ...
Страница 276: ...SECTION 4 BOOM PLATFORM 4 60 JLG Lift 3121160 THIS SENSOR ON NON ADE MACHINES ONLY Figure 4 21 UMS Sensor Location ...
Страница 277: ...SECTION 4 BOOM PLATFORM 3121160 JLG Lift 4 61 ADE MACHINES NON ADE MACHINES Figure 4 22 UMS Module Location ...
Страница 286: ...SECTION 4 BOOM PLATFORM 4 70 JLG Lift 3121160 NOTES ...
Страница 307: ...SECTION 5 HYDRAULICS 3121160 JLG Lift 5 21 Figure 5 17 Variable Displacement Pump Rexroth ...
Страница 316: ...SECTION 5 HYDRAULICS 5 30 JLG Lift 3121160 NOTES ...
Страница 319: ...SECTION 6 JLG CONTROL SYSTEM 3121160 JLG Lift 6 3 Figure 6 2 ADE Block Diagram ...
Страница 325: ...SECTION 6 JLG CONTROL SYSTEM 3121160 JLG Lift 6 9 Figure 6 8 Analyzer Flow Chart Version 5 X Software Sheet 2 of 4 ...
Страница 328: ...SECTION 6 JLG CONTROL SYSTEM 6 12 JLG Lift 3121160 Figure 6 11 Control Module Location ...
Страница 374: ...SECTION 6 JLG CONTROL SYSTEM 6 58 JLG Lift 3121160 NOTES ...
Страница 381: ...SECTION 7 BASIC ELECTRICAL INFORMATION SCHEMATICS 3121160 JLG Lift 7 7 Figure 7 11 Connector Installation ...
Страница 400: ...SECTION 7 BASIC ELECTRICAL INFORMATION SCHEMATICS 7 26 JLG Lift 3121160 Figure 7 34 Hydraulic Schematic Sheet 1 of 6 ...
Страница 402: ...SECTION 7 BASIC ELECTRICAL INFORMATION SCHEMATICS 7 28 JLG Lift 3121160 Figure 7 36 Hydraulic Schematic Sheet 3 of 6 ...
Страница 404: ...SECTION 7 BASIC ELECTRICAL INFORMATION SCHEMATICS 7 30 JLG Lift 3121160 Figure 7 38 Hydraulic Schematic Sheet 5 of 6 ...
Страница 406: ...SECTION 7 BASIC ELECTRICAL INFORMATION SCHEMATICS 7 32 JLG Lift 3121160 NOTES ...
Страница 407: ......