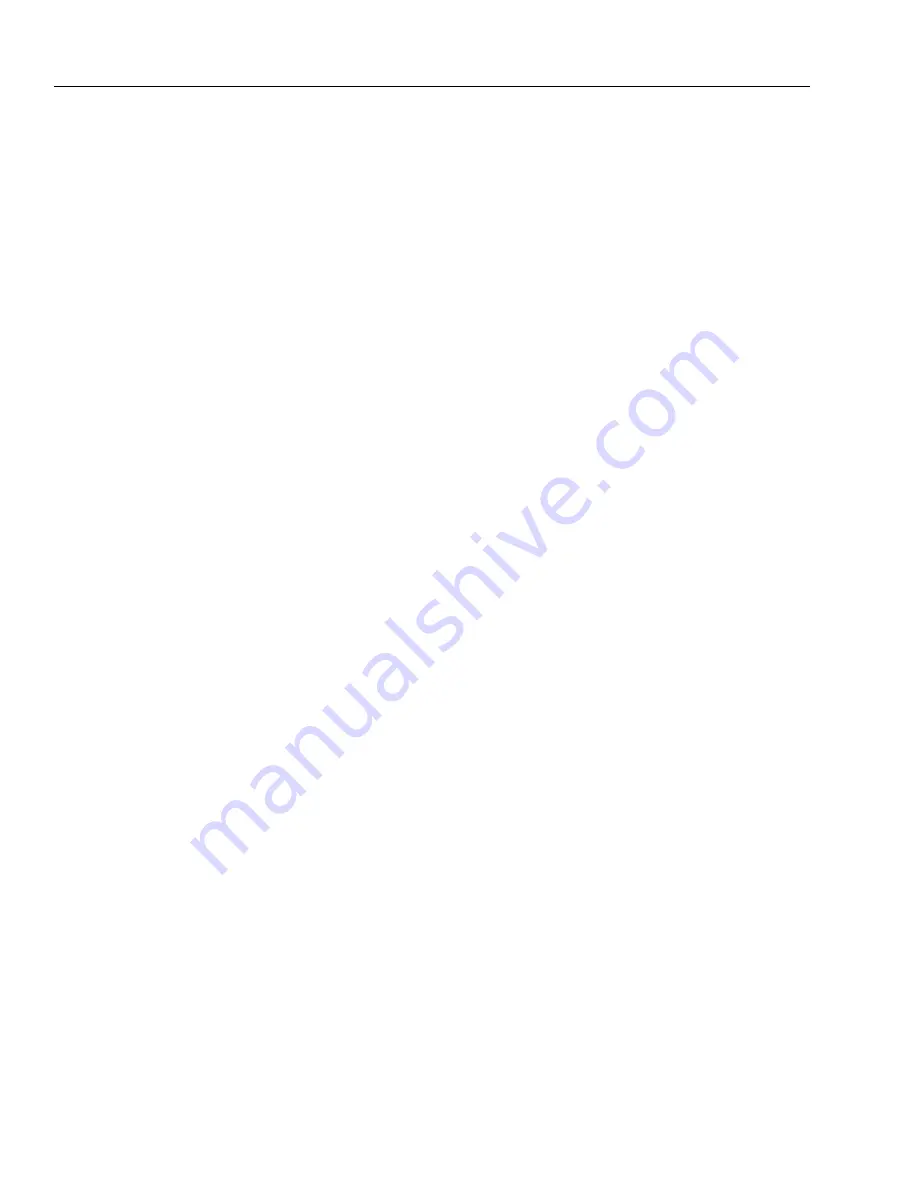
SECTION 2 - GENERAL
2-6
31215079
2. Unless specific torque requirements are given within
the text, standard torque values should be used on
heat-treated bolts, studs, and steel nuts, in accor-
dance with recommended shop practices (See
Torque Chart Section 1).
Hydraulic Lines and Electrical Wiring
Clearly mark or tag hydraulic lines and electrical wiring,
as well as their receptacles, when disconnecting or
removing them from the unit. This will assure that they
are correctly reinstalled.
Hydraulic System
1. Keep the system clean. If evidence of metal or rubber
particles are found in the hydraulic system, drain and
flush the entire system.
2. Disassemble and reassemble parts on a clean work
surface. Clean all metal parts with non-flammable
cleaning solvent. Lubricate components, as required,
to aid assembly.
Lubrication
Service applicable components with the amount, type,
and grade of lubricant recommended in this manual, at
the specified intervals. When recommended lubricants
are not available, consult your local supplier for an
equivalent that meets or exceeds the specifications
listed.
Battery
Clean battery, using a non-metallic brush and a solution
of baking soda and water. Rinse with clean water. After
cleaning, thoroughly dry battery and coat terminals
with an anti corrosion compound.
Lubrication and Servicing
Components and assemblies requiring lubrication and
servicing are shown in the Lubrication Chart in
Section 1.
2.4
LUBRICATION AND INFORMATION
Hydraulic System
1. The primary enemy of a hydraulic system is contami-
nation. Contaminants enter the system by various
means, e.g., using inadequate hydraulic oil, allowing
moisture, grease, filings, sealing components, sand,
etc., to enter when performing maintenance, or by
permitting the pump to cavitate due to insufficient
system warm-up or leaks in the pump supply (suc-
tion) lines.
2. The design and manufacturing tolerances of the
component working parts are very close, therefore,
even the smallest amount of dirt or foreign matter
entering a system can cause wear or damage to the
components and generally results in faulty opera-
tion. Every precaution must be taken to keep hydrau-
lic oil clean, including reserve oil in storage. Hydraulic
system filters should be checked, cleaned, and/or
replaced as necessary, at the specified intervals
required in the Lubrication Chart in Section 1. Always
examine filters for evidence of metal particles.
3. Cloudy oils indicate a high moisture content which
permits organic growth, resulting in oxidation or cor-
rosion. If this condition occurs, the system must be
drained, flushed, and refilled with clean oil.
4. It is not advisable to mix oils of different brands or
types, as they may not contain the same required
additives or be of comparable viscosities. Good
grade mineral oils, with viscosities suited to the
ambient temperatures in which the machine is oper-
ating, are recommended for use.
NOTE:
Metal particles may appear in the oil or filters of new
machines due to the wear-in of meshing compo-
nents.
Hydraulic Oil
1. Refer to Section 1 for recommendations for viscosity
ranges.
2. JLG recommends Standard UTTO Fluid, which has an
SAE viscosity of 10W-30 and a viscosity index of 152.
NOTE:
Start-up of hydraulic system with oil temperatures
below -15°F (-26°C) is not recommended. If it is nec-
essary to start the system in a sub-zero environment,
it will be necessary to heat the oil with a low density,
100VAC heater to a minimum temperature of -15°F
(-26°C).
Go
to
Discount-Equipment.com
to
order
your
parts