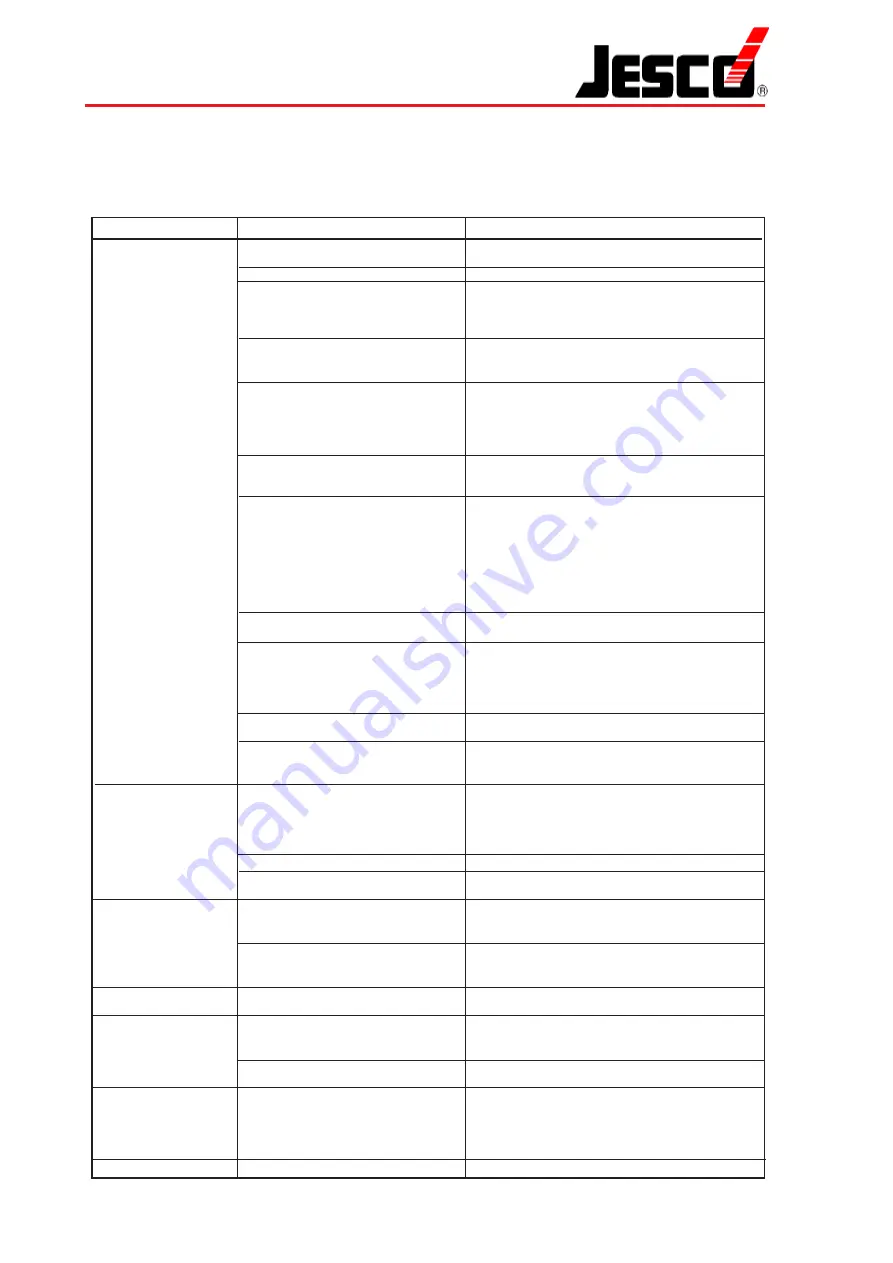
Chlorinator C 2700
BW 2 03 01 / 7
Operating and Maintenance Instructions
Type of fault
Possible cause
Remedy
No display or
Chlorine barrel empty, indicated by
Connect new barrel.
insufficient display
low chlorine gas pressure.
on flow meter
Connecting valve closed.
Open valve.
Chlorine gas line bent or blocked.
Close chlorine barrel,
drain off line and device,
stop motive water supply, dismantle chlorine
gas line and clean or replace it.
Blocked filter before inlet valve,
Clean or replace filter.
indicated by low chlorine volume
despite high vacuum.
Motive water pressure too low.
Compare ejector characteristics sheet with
acutal pressure values, install booster pump,
if necessary.
Open reducing valve.
Back pressure too high.
Excessive pressure drop in dirt trap
Remove dirt trap from reducing valve
of motive water.
and clean filter.
Also flush water lines.
Ejector blocked, contaminated or
Remove ejector, clean PVC inlet nozzle and outlet
encrusted by deposits (possibly caused
borehole using hypochloric acid and rinse well in
by decarbonization in the diffusor).
water. If possible, apply higher concentration of
chlorine (1...2g/m
3
) in the solution to obtain more
HCL. Set motive pressure before ejector as low as
possible but make sure that the maximum chlorine
still be metered.
Block solution injection fitting.
Remove and clean solution injection fitting and
check if the valve is fully open.
Excessive back pressure caused by bent
Lay line with sufficiently large bends: PVC
or blocked solution line. Excessive
lines may have restricted cross-sections due to
pressure losses due to friction in pipes
wrong gluing.
or fittings.
Check joints.
Float stuck in flow meter glass.
Clean flow meter as described under
Maintenance.
Components under vacuum prime
Check the joints of the suction line, the ejector
external air.
non-return valve and the flow meter glass holder.
Metered volume
Inlet valve blocked.
Remove inlet valve as described under
does not increase
Maintenance.
when adjusting screw
is opened.
Vacuum primed by the ejector is too low.
See above.
Float stuck in the flow meter glass.
Clean the flow meter glass as described under
Maintenance.
Chlorine odor in the
Gas lines leak.
Close barrel connecting valve immediately and drain
room.
off lines using the ejector. Leakage test as described
under Startup.
Safety valve integrated in device blows
Remove and clean inlet valve as described under
off. Inlet valve is dirty or damaged.
Maintenance. Replace damaged parts.
Vent line primes
Diaphragm suspension leaking or
Dismantle device and check all parts.
constantly air.
diaphragm torn.
Reassemble very carefully.
Water in the device.
Ejector non-return valve defective.
Remove and dismantle non-return valve.
Clean it and replace defective parts. Install
motor ball cock (see flow diagram, item 12).
End of vent line not protected
Lay vent line correctly. Line end must show down.
against entry of water.
Re-liquefied chlorine
Temperature in eqiupment room too low
Increase temperature in the equipment room.
indicated by yellow
in comparison to chlorine storage room.
Install heating block or pressure reducing valve.
liquid in measuring
Install drop separator.
glass and decomposed
PVC parts.
Icing.
Chlorine consumption too high.
Connect more chlorine barrels.
Troubleshooting
Lutz-Jesco GmbH
Improved changes are always reserved without notice.